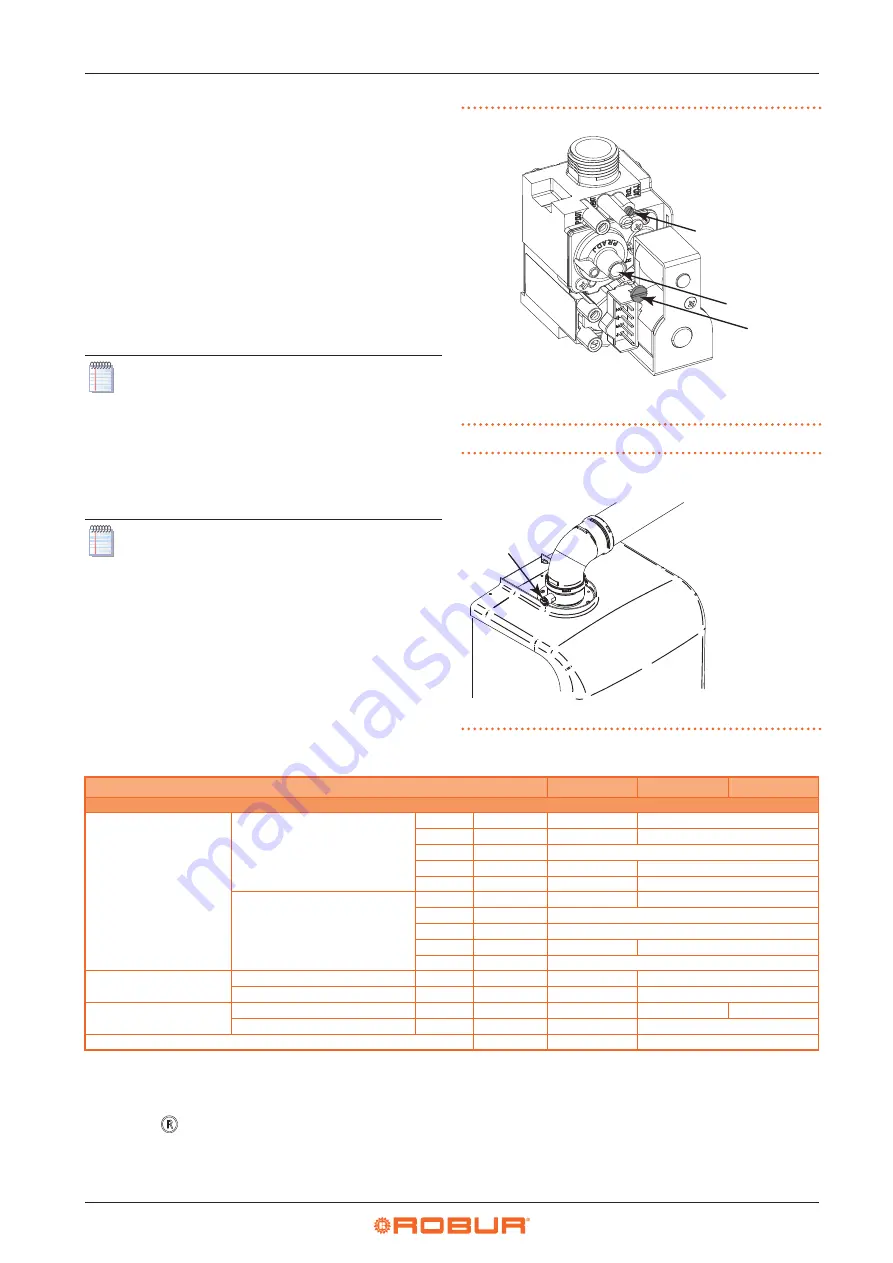
First start-up
44
5
ignition request is disabled. The regular operation of the
boiler is allowed only when the operation is completed.
To check and calibrate the CO
2
value at maximum and minimum
power, proceed as follows, referring to Figure 5.9
The CO
2
values and other parameters useful to verify combus-
tion are summarized in Table 5.5
▶
Power the boiler.
▶
Open the gas valve on the boiler and check that the valves
connecting to the system are open.
▶
Activate the heating request to the boiler, through the con-
trol devices provided, and provide an adequate thermal load
for carrying out the verification operations.
▶
Insert the flue gas analyser into the flue gas analyser socket
and turn it on.
For the Caldaria 35 and Caldaria 55.1 models, the flue gas
analysis socket is positioned on the flanged socket (de-
tail PF, Figure 5.10
p. 44), or on the optional rainproof
terminal (code OTRM031).
If you want to use the flue gas analysis socket positioned
on the flanged socket, to access the socket it is necessary
to remove the upper flange and the upper casing of the
boiler (Paragraph 5.2
For the Caldaria 100.2 model, the flue gas analysis socket
must be provided on the flue gas exhaust pipe. It is al-
ready provided on the rainproof terminal, available as
optional OTRM009.
Figure 5.9
Gas valve
A
Protection screw
1
Gas flow adjustment screw
2
Offset adjustment screw
1
2
A
Figure 5.10
Socket for flue gas analysis for Caldaria 35 and 55.1
PF
Flue gas
analysis socket
PF
Table 5.5
Caldaria combustion parameters
Caldaria 35
Caldaria 55.1
Caldaria 100.2
Installation data
CO
2
percentage in fumes
Nominal heat input
G20
%
9,45 ÷ 9,25
9,3 ÷ 9,1
G25
%
9,35 ÷ 9,15
9,3 ÷ 9,1
G25.3
%
9,3 ÷ 9,1
G30
%
11,4 ÷ 11,2
11,3 ÷ 11,1
G31
%
10,55 ÷ 10,35
10,3 ÷ 10,1
Minimal heat input
G20
%
9,05 ÷ 8,85
9,0 ÷ 8,8
G25
%
9,0 ÷ 8,8
G25.3
%
9,0 ÷ 8,8
G30
%
10,75 ÷ 10,55
10,9 ÷ 10,7
G31
%
9,9 ÷ 9,7
Flue temperature
Nominal heat input
G20
°C
69,4
66,4
Minimal heat input
G20
°C
61,3
56,8
Fumes flow rate
Nominal heat input
G20
kg/h
54
80
161
Minimal heat input
G20
kg/h
7
8
CO emission
ppm
75,0
68,0
5.5.1
Minimum heating power
1. Activate the chimney sweep function by pressing for 7 sec-
onds the
key (Figure 6.1
p. 47). The maximum time be-
fore being forced out of the function is 15 minutes.
2. Check that the CO
2
value conforms to that reported in Table
5.5
3. If this is not the case, unscrew the protection screw A and ad-
just with a 4 hex key the screw 2 of the offset adjuster (Figure
5.9
p. 44). To increase the value of CO
2
turn the screw
clockwise and vice-versa if you want to decrease it.
4. Once completed the adjustment, tighten the protection
screw A on the offset adjuster.
Содержание Caldaria 100.2 Condensing+ export
Страница 55: ......