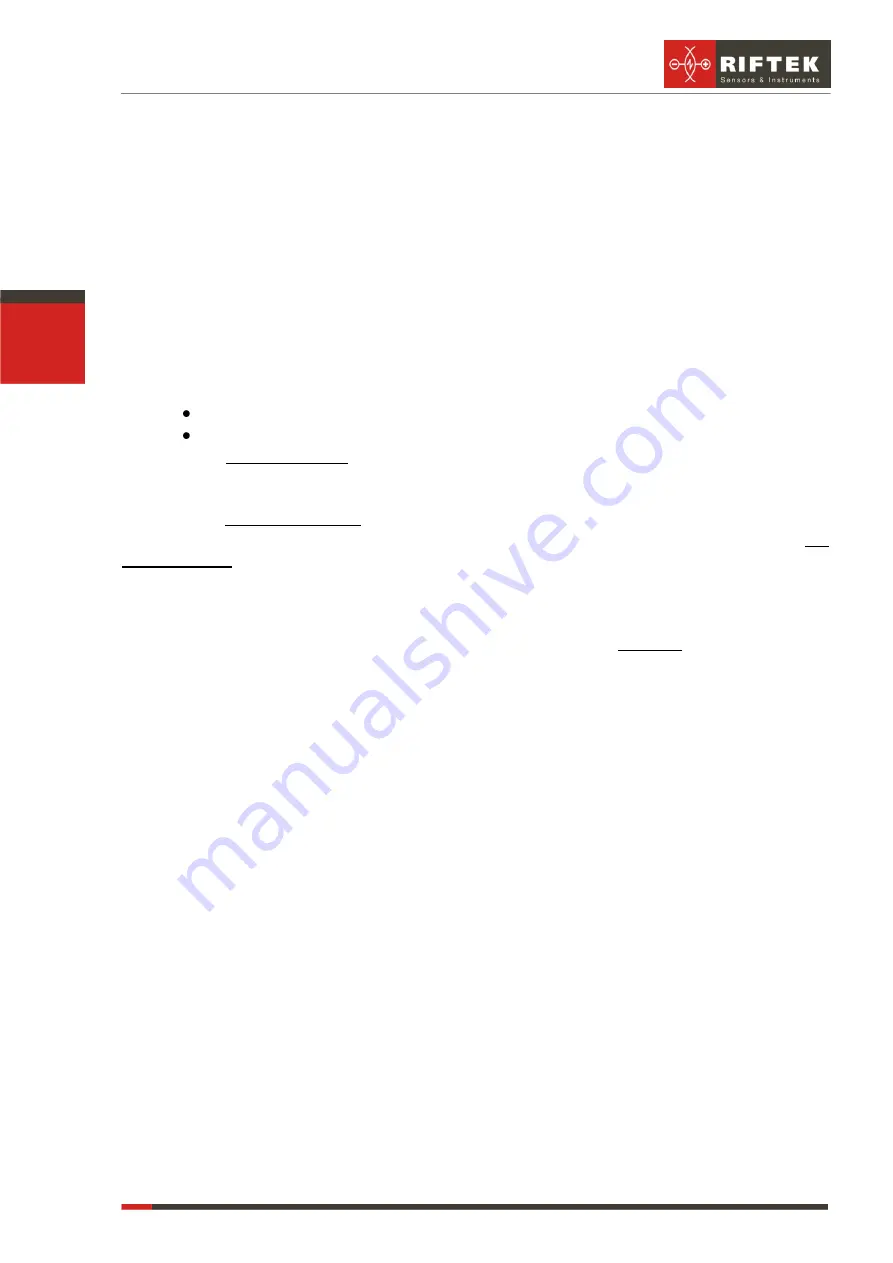
Triangulation Laser Sensors, RF605 Series
RF605 [Revision 2.0] 10th January 2011 valid for sensors with serial numbers 11000 and higher
9
Note 1.
The measurement frequency depends on the integration time of the re-
ceiving array. Maximum frequency (2 kHz) is achieved for the integration time
≤106 μs
(minimum possible integration time is 10
μs). As the integration time increases above
106
μs, the result updating time increases proportionally.
Note 2.
Increasing of this parameter expands the possibility of control of low-
reflecting (diffuse component) surfaces; at the same time this leads to reduction of mea-
surement frequency and increases the effects of exterior light (background) on the mea-
surement accuracy. Factory setting of the limiting time of integration is 3200 us.
Note 3.
Decreasing of this parameter lets to increase measurement frequency,
but can decrease measurement accuracy.
10.2. Sampling mode
This parameter specifies one of the two result sampling options in the case
where the sensor works in the data stream mode:
Time Sampling;
Trigger Sampling.
With
Time Sampling
selected, the sensor automatically transmits the measure-
ment result via serial interface in accordance with selected time interval (sampling pe-
riod).
With
Trigger sampling
is selected, the sensor transmits the measurement result
when external synchronization input (IN input of the sensor) is switched and taking
the
division factor
set into account.
10.3. Sampling period
If the Time Sampling mode is selected, the ‗sampling period‘ parameter deter-
mines the time interval in which the sensor will automatically
transmit
the measurement
result. The time interval value is set in increments of 0.01 ms.
For example,
for the pa-
rameter value equal to 100, data are transmitted through bit-serial interface with a period
of 0,01*100 = 1 ms.
If the Trigger Sampling mode is selected, the ‗sampling period‘ parameter de-
termines the division factor for the external synchronization input.
For example,
for the
parameter value equal to 100, data are transmitted through bit-serial interface when
each 100
th
synchronizing pulse arrives at IN input of the sensor
.
Note 1.
It should be noted that the ‗sampling mode‘ and ‗sampling period‘ para-
meters control only the transmission of data. The sensor operation algorithm is so built
that measurements are taken at a maximum possible rate determined by the integration
time period, the measurement results is sent to buffer and stored therein until a new re-
sult arrives. The above-mentioned parameters determine the method of the readout of
the result form the buffer.
Note 2.
If the bit-serial interface is used to receive the result, the time required
for data transmission at selected data transmission rate should be taken into account in
the case where small sampling period intervals are used. If the transmission time ex-
ceeds the sampling period, it is this time that will determine the data transmission rate.
10.4. The point of zero
This parameter sets a zero point of absolute system of coordinates in any point
within the limits of a working range. You can set this point by corresponding command or
by connecting AL input to the ground line (this input must preliminarily be set to mode 3).
When the sensor is fabricated, the base distance is set with a certain uncertainty, and, if
necessary, it is possible to define the point zero more accurately.
Содержание RF603 Series
Страница 1: ......