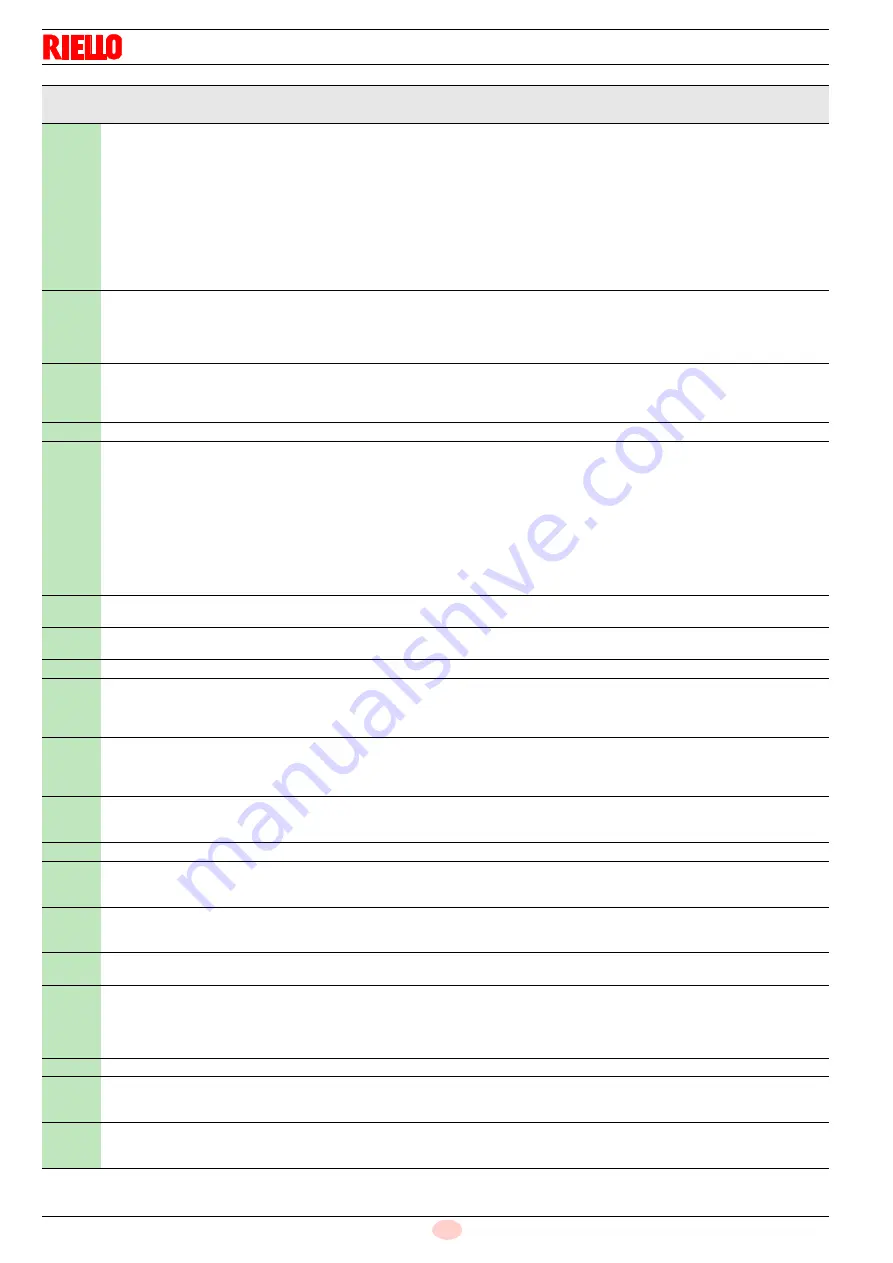
20095002
58
GB
Faults - Probable causes - Solutions
Bit 3
Valence
8
Curve too steep in terms of train speed
The speed was not reached because the curve was too steep.
1. With a train REC3... of 20 s, the speed variation between 2
points of the curve (in modulating mode) cannot exceed 10%.
With a train REC3... of 10 s, the speed variation between 2
points of the curve (in modulating mode) cannot exceed 20%.
With a train REC3... of 5 s, the speed variation between 2
points of the curve (in modulating mode) cannot exceed 40%.
---> Between the ignition point (P0) and the low flame point
(P1), the speed in modulating mode may vary by a maximum of
40%, regardless of the train REC3….
2. The VSD train must be about 20% faster than the train of the
standard unit (parameters 522, 523).
Bit 4
Valence
16
Speed signal interruption
No speed detected, despite the control.
1. Check the motor is rotating.
2. Check whether the speed sensor provides a signal (LED /
check the distance from the sensor disc).
3. Check the VSD wiring.
Bit 5
Valence
32
Quick switch-off due to excessive speed deviation
For about 1 s, the speed deviation was >10% outside the
envisaged range.
1. Check the train times of REC3.... and VSD.
2. Check the VSD wiring.
84
#
Servomotors curve slope
Bit 0
Valence
1
VSD: Curve too steep in terms of train speed
1. With a train REC3... of 20 s, the speed variation between
points of the curve (in modulating mode) cannot exceed 10%
.With a train REC3... of 10 s, the speed variation between
points of the curve (in modulating mode) cannot exceed 20%
2. With a train REC3... of 5 s, the speed variation between
points of the curve (in modulating mode) cannot exceed 40%
---> Between the ignition point (P0) and the low flame point
(P1), the speed in modulating mode may vary by a maximum of
40%, regardless of the train REC3….
The VSD train must be about 20% faster than the train of the
standard unit (parameters 522, 523)
Bit 1
Valence 2..3
Fuel servomotor: Curve too steep in terms of train ratio
The slope of the curve can correspond to a maximum position
variation of 31° between 2 points of the modulation curve
Bit 2
Valence 4..7
Air servomotor: Curve too steep in terms of train ratio
The slope of the curve can correspond to a maximum position
variation of 31° between 2 points of the modulation curve
85
#
Reference error of a servomotor
0
Reference error of the fuel servomotor
The reference of the fuel servomotor was not successful.
It was not possible to reach the reference point.
1. Check if the servomotors have been inverted.
2. Check if the servomotor is blocked or overloaded.
1
Reference error of the air servomotor
The reference of the air servomotor was not successful.
It was not possible to reach the reference point.
1. Check if the servomotors have been inverted.
2. Check if the servomotor is blocked or overloaded.
Bit 7
Valence
128
Reference error owing to parameter modification
The parameterisation of an actuator (e.g. the reference
position) has been modified. This error will be visualised to start
up a new reference.
86
#
Fuel servomotor error
0
Position error
It was not possible to reach the target position within the
required range ---> Check to see if the servomotor is blocked or
overloaded.
Bit 0
Valence 1
Circuit open
Open circuit detected on the connection of the servomotor
---> Check the wiring (voltage between pins 5 or 6 and 2 of the
X54 connector should be > 0.5 V).
Bit 3
Valence
8
Curve too steep in terms of train ratio
The slope of the curve can correspond to a maximum position
modification of 31° between 2 points of the modulation curve.
Bit 4
Valence
16
Deviation of section compared with the last reference
Overloading of the servomotor or servomotor subjected to
mechanical torsion.
1. Check if the servomotor is blocked in any point along its
range of action.
2. Check if the torque is sufficient for the application.
87
#
Air servomotor error
0
Position error
It was not possible to reach the target position within the
requested tolerance range.
1. Check if the servomotor is blocked or overloaded.
Bit 0
Valence 1
Circuit open
Open circuit detected on the connection of the servomotor
---> Check the wiring (voltage between pins 5 or 6 and 2 of the
X54 connector should be > 0.5 V).
Error
code
Diagnostic code
Meaning of the REC 27.100A2 system
Recommended measures
Содержание RS 160/EV BLU TC
Страница 2: ...Original instructions...
Страница 69: ...67 20095002 GB Appendix Electrical panel layout 0 1 2 2 2 3 2 4 2 2 2 2 2 2 2 52 5 5 2 2 3 2 67 8 9...
Страница 70: ...20095002 68 GB Appendix Electrical panel layout 0 1 1 0 2 0 00 0 1 3 414 56 2 7 8 03 59 3 A...
Страница 71: ...69 20095002 GB Appendix Electrical panel layout...
Страница 72: ...20095002 70 GB Appendix Electrical panel layout 0 1 1 2 1 1 1 1 1 3 3 3 1 1 0 1 1 4 4 1 4 41 1 1 5 6 4 4 768 9...