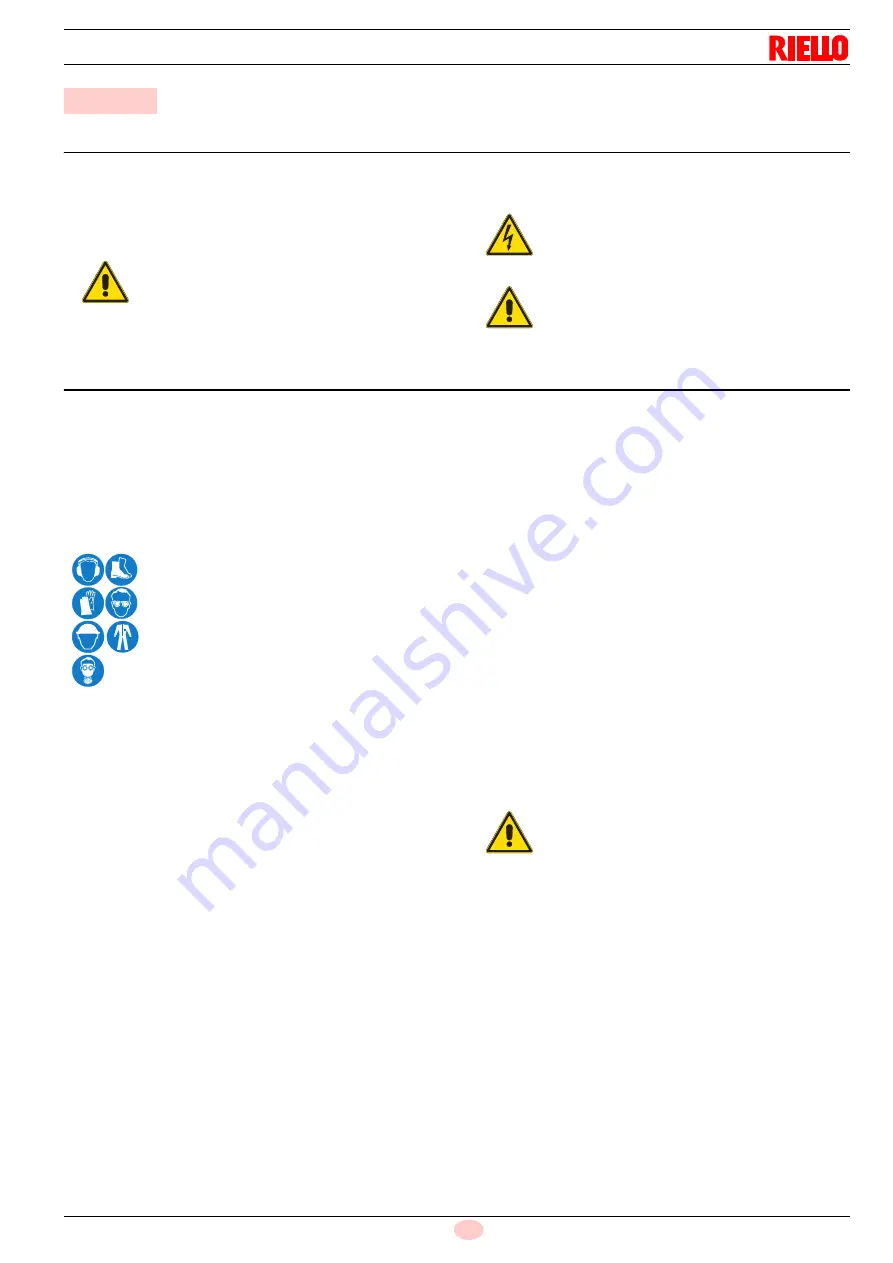
23
20158125
GB
Maintenance
9.1
Notes on safety for the maintenance
The periodic maintenance is essential for the good operation,
safety, yield and duration of the burner.
It allows you to reduce consumption and polluting emissions and
to keep the product in a reliable state over time.
Before carrying out any maintenance, cleaning or checking oper-
ations:
9.2
Maintenance programme
9.2.1
Maintenance frequency
The combustion system should be checked at least once a
year by a representative of the manufacturer or another
specialised technician.
9.2.2
Checking and cleaning
Combustion head
Open the burner and make sure that all components of the
combustion head are in good condition, not deformed by the
high temperatures, free of impurities from the surroundings
and correctly positioned.
Clean the combustion head in the fuel exit area, on the diffuser
disc.
Burner
Check for excess wear or loose screws and clean the outside of
the burner.
Fan
Check to make sure that no dust has accumulated inside the fan
or on its blades, as this condition will cause a reduction in the air
flow rate and provoke polluting combustion.
Flame sensor
Clean the flame sensor.
Electrodes
Check the correct position of electrodes
Nozzles
It is advisable to replace nozzles every year during regular
maintenance operations.
Do not clean the nozzle openings; do not even open them.
Filters
Check the filtering baskets on line and at nozzle present in the
system. Clean or replace if necessary.
If rust or other impurities are observed inside the pump, use a
separate pump to lift any water and other impurities that may
have deposited on the bottom of the tank.
Pump
Delivery pressure must correspond with the table on Tab. H on
page 20. Please check that the supply line and filters are clear.
The use of a pump vacuum gauge will assist in this.
This measure permits the cause of the anomaly to be traced to
either the suction line or the pump.
If the problem lies in the suction line, check to make sure that the
filter is clean and that air is not entering the piping.
Hoses
Check periodically the flexible pipes conditions. They have
to be replaced at least
every 2 years
.
In case of use of gas oil and bio fuel blends, it is strongly rec-
ommended to inspect
even more frequently
the hoses and
replace them where contamination has occurred.
Check to make sure that the hoses are still in good condi-
tion.
Fuel tank
If water or contamination is present within the fuel tank, it is es-
sential that this is removed before the equipment is to be used.
This is extremely important when gas oil containing Bio diesel is
in use.
If in doubt about how to achieve this then please contact the fuel
or oil tank supplier.
Boiler
Clean the boiler as indicated in the appliance accompanying in-
structions in order to maintain all the original combustion charac-
teristics intact, especially the flue gas temperature and
combustion chamber pressure.
9
Maintenance
DANGER
The maintenance interventions and the calibration
of the burner must only be carried out by qualified,
authorised personnel, in accordance with the con-
tents of this manual and in compliance with the
standards and regulations of current laws.
DANGER
disconnect the electricity supply from the burner
by means of the main switch of the system;
DANGER
isolate the fuel supply.
The operator must use the required equipment
during maintenance.
WARNING
The hoses supplied with this burner set for
Kerosene use are not suitable for use with Gas oil
containing a Bio blend.
Please refer to the spare part list for the specific
hoses suitable for bio fuel use.
In case of use with gas oil containing up to 30%
Bio blend, it will be essential to use flexible oil
lines suitable for bio fuel use.
Please contact Riello for further information.
Содержание RDB 3.2 BT 58/70
Страница 2: ...Original instructions...