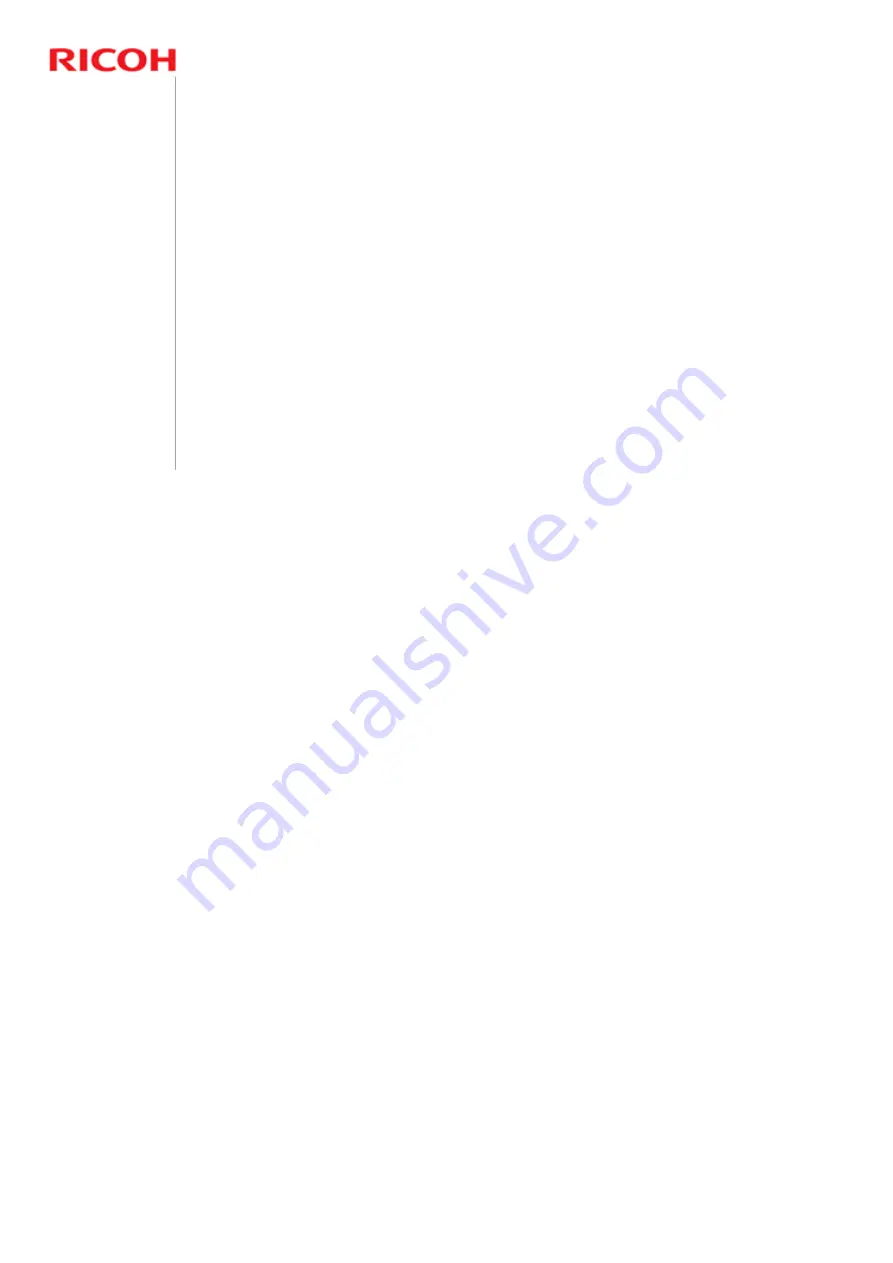
77
PE-MF3/PE-P2 Training
Slide 77
Process Control Summary
What is done?
The machine calibrates the TM sensors
The machine makes a 9-grade pattern on the
belt, and the central TM sensor scans these
patterns.
The machine can then calculate the correct
development bias and laser diode power.
MUSIC: The machine then checks for color
registration errors. To do this it makes lines at the
left, center, and right of the transfer belt and
scans these lines with the TM sensors.
Process control uses these components:
Central TM (Toner Mark) sensors
Temperature/humidity sensor at the rear right of the machine. This is used to
determine whether the conditions have changed significantly enough so that
process control must be done.
Process control flow
1. TM sensor correction (Vsg adjustment)
¾
The center TM sensor checks the bare transfer belt's reflectivity and the
machine calibrates the TM sensors.
2. Development bias control
¾
The machine makes a 7-gradation pattern on the transfer belt for each
toner color. The pattern has 9 squares (the sequence is as follows: 7 yellow
squares, 7 cyan squares, 7 magenta squares and 7 black squares). Each of
the squares is 10 mm x 17 mm, and is a solid-color square. To make the
squares, the machine changes the development bias and charge roller
voltage. The difference between development bias and charge roller
voltage is always the same.
¾
The center TM sensor detects the densities of the 7 solid-color squares for
each color. The machine calculates an appropriate development bias from
this data.
¾
This process takes about 33 seconds to be completed.
3. LD power control
¾
For LD power control, the machine does the same sequence described in
"2 Development bias control". Finally, the machine calculates an
appropriate LD power.
4. MUSIC (Mirror Unit Skew and Interval Control)
¾
The machine uses the TM sensors to measure sample lines deposited on
the ITB, and corrects color image registration adjustment based on the
sensor readings. Sample lines are made on the left, center and right of the
ITB.
¾
This process takes about 22 seconds to be completed.
Содержание M095
Страница 42: ...42 PE MF3 PE P2 Training Slide 42 Service Training M099 M100 M095 M096 Installation No additional notes ...
Страница 45: ...45 PE MF3 PE P2 Training Slide 45 Service Training M099 M100 M095 M096 Service Mode No additional notes ...
Страница 53: ...53 PE MF3 PE P2 Training Slide 53 Service Training M099 M100 M095 M096 Maintenance No additional notes ...
Страница 58: ...58 PE MF3 PE P2 Training Slide 58 Service Training M099 M100 M095 M096 Machine Overview No additional notes ...
Страница 69: ...69 PE MF3 PE P2 Training Slide 69 Original Feed Path 1 Original feed path ...
Страница 92: ...92 PE MF3 PE P2 Training Slide 92 Service Training M099 M100 M095 M096 Laser Unit No additional notes ...
Страница 104: ...104 PE MF3 PE P2 Training Slide 104 Service Training M099 M100 M095 M096 AIO Cartridge No additional notes ...
Страница 116: ...116 PE MF3 PE P2 Training Slide 116 Service Training M099 M100 M095 M096 Paper Feed No additional notes ...
Страница 125: ...125 PE MF3 PE P2 Training Slide 125 Service Training M099 M100 M095 M096 Image Transfer No additional notes ...
Страница 141: ...141 PE MF3 PE P2 Training Slide 141 Service Training M099 M100 M095 M096 Fusing No additional notes ...
Страница 153: ...153 PE MF3 PE P2 Training Slide 153 Stripper Pawl Solenoid This is a new component for this series No additional notes ...
Страница 184: ...184 PE MF3 PE P2 Training Slide 184 No additional notes ...