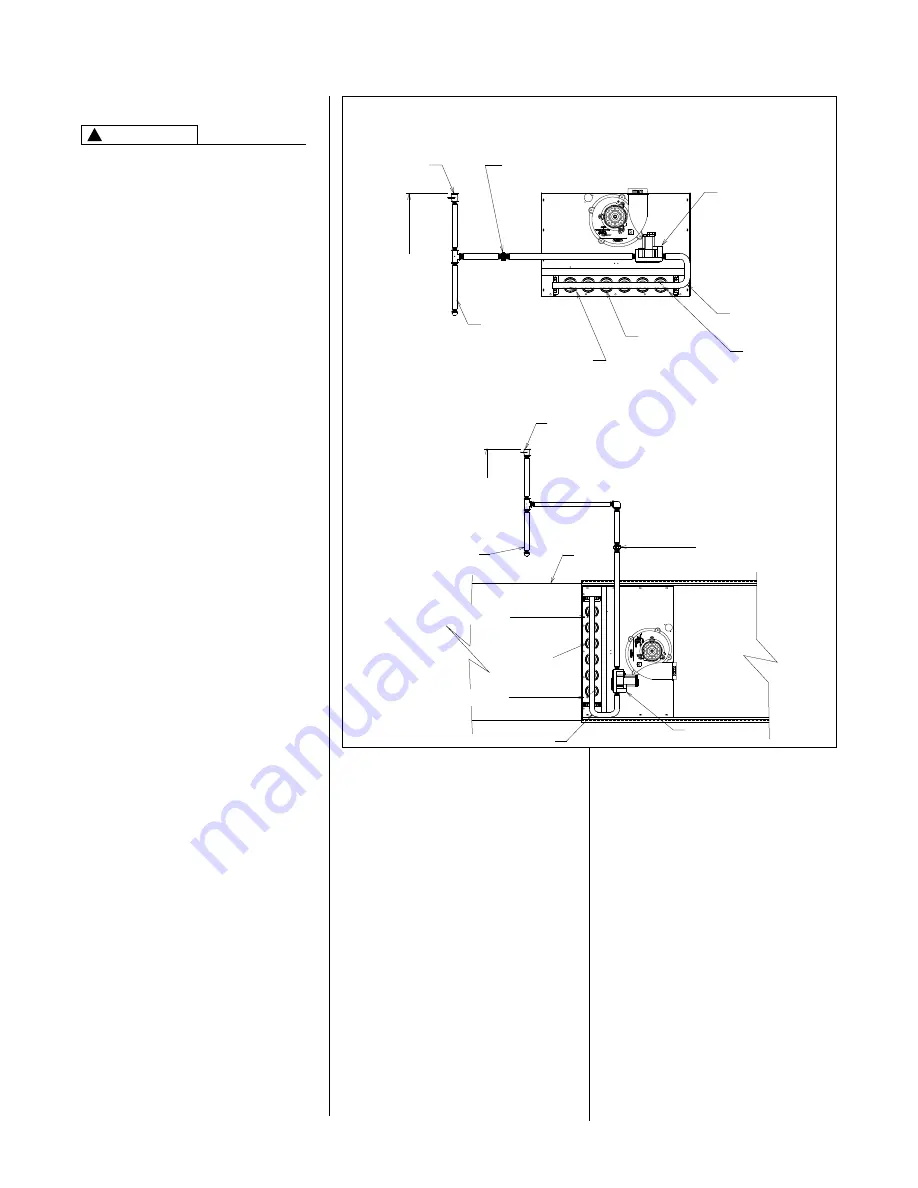
FIGURE 12
GAS PIPING INSTALLATION
UPFLOW & DOWNFLOW
15
GAS SUPPLY AND PIPING
GAS SUPPLY
THIS FURNACE IS EQUIPPED AT
THE FACTORY FOR USE ON
NATURAL GAS ONLY. CONVER-
SION TO LP GAS REQUIRES A
SPECIAL KIT SUPPLIED BY THE
DISTRIBUTOR OR MANU-
FACTURER. MAILING ADDRESSES
ARE LISTED ON THE FURNACE
RATING PLATE, PARTS LIST AND
WARRANTY. FAILURE TO USE
THE PROPER CONVERSION KIT
CAN CAUSE FIRE, CARBON
MONOXIDE POISONING,
EXPLOSION, PROPERTY
DAMAGE, PERSONAL INJURY OR
DEATH.
See the conversion kit index
supplied with the furnace. This
index identifies the proper LP Gas
Conversion Kit required for each
particular furnace.
IMPORTANT:
Any additions,
changes or conversions required for
the furnace to satisfactorily meet the
application should be made by a
qualified installer, service agency or
the gas supplier, using factory-
specified or approved parts.
IMPORTANT:
Connect this furnace
only to gas supplied by a commercial
utility.
IMPORTANT:
A U.L. recognized
fuel gas and CO detector(s) are
recommended in all applications,
and their installation should be in
accordance with the detector
manufacturer’s recommendations
and/or local laws, rules, regulations or
customs.
GAS PIPING
Install the gas piping according to all
local codes and regulations of the
utility company.
If possible, run a separate gas supply
line directly from the meter to the
furnace. Consult the local gas
company for the location of the
manual main shut-off valve.
The gas
line and manual gas valve must be
adequate in size to prevent undue
pressure drop and never smaller
than the pipe size to the com-
bination gas valve on the furnace.
Refer to Table 2 for the recom-
mended pipe size for natural gas and
Table 3 for LP gas pipe sizes.
!
WARNING
HORIZONTAL
IMPORTANT:
It is permissible to run
flexible gas connector inside the unit to
a piece of black pipe.
Install a ground joint union outside
the cabinet to easily remove the
control valve assembly. Install a
manual shut-off valve in the gas line
outside the furnace casing.
The valve
should be readily accessible to turn the
gas supply on or off. Install a drip leg in
the gas supply line as close to the
furnace as possible. Always use a pipe
compound resistant to the action of
liquefied petroleum gases on all
threaded connections.
IMPORTANT:
When making gas pipe
connections, use a back-up wrench to
prevent any twisting of the control
assembly and gas valve.
Any strains on the gas valve can
change the position of the gas orifices
in the burners. This can cause erratic
furnace operation.
IMPORTANT:
ENSURE that the
furnace gas control valve not be
subjected to high gas line supply
pressures.
DISCONNECT the furnace and its
individual shut-off valve from the gas
supply piping during
any pressure
testing that exceeds 1/2 p.s.i.g. (3.48
kPa).
MANUAL GAS
VALVE
UNION
4 TO 5 FEET
ABOVE FLOOR
REQ’D BY SOME
UTILITIES
DRIP LEG
DIRECT SPARK IGNITOR
GAS VALVE
MANIFOLD
FLAME
SENSOR
BURNERS
MANUAL GAS VALVE
4 TO 5 FEET
ABOVE FLOOR
REQ’D BY SOME
UTILITIES.
DRIP LEG
UNION
DUCT
DIRECT SPARK IGNITOR
BURNERS
FLAME SENSOR
MANIFOLD
GAS VALVE
STA-0764-01
ST-A0763-01
Содержание 1x2000
Страница 20: ...20 FIGURE 16 UTEC NO 1095 100 CONTROL BOARD TWINNING CONNECTION SINGLE STAGE OPERATION I685 ...
Страница 21: ...21 FIGURE 17 UTEC NO 1095 100 CONTROL BOARD TWINNING CONNECTION TWO STAGE OPERATION I684 ...
Страница 29: ...29 FIGURE 25 FILTER RETAINING RODS SIDE RETURN FIGURE 26 DOWNFLOW FILTER INSTALLATION ...
Страница 31: ... FIGURE 27 INTEGRATED FURNACE CONTROL IFC TROUBLESHOOTING GUIDE FOR UTEC 1095 101 31 ...
Страница 32: ...32 ...
Страница 33: ... FIGURE 28 UTEC 1095 101 INTEGRATED FURNACE CONTROL 33 ...
Страница 34: ...34 ...
Страница 35: ...35 ...
Страница 36: ...36 CM 599 Rheem Manufacturing Company Air Conditioning Division Fort Smith Arkansas ...