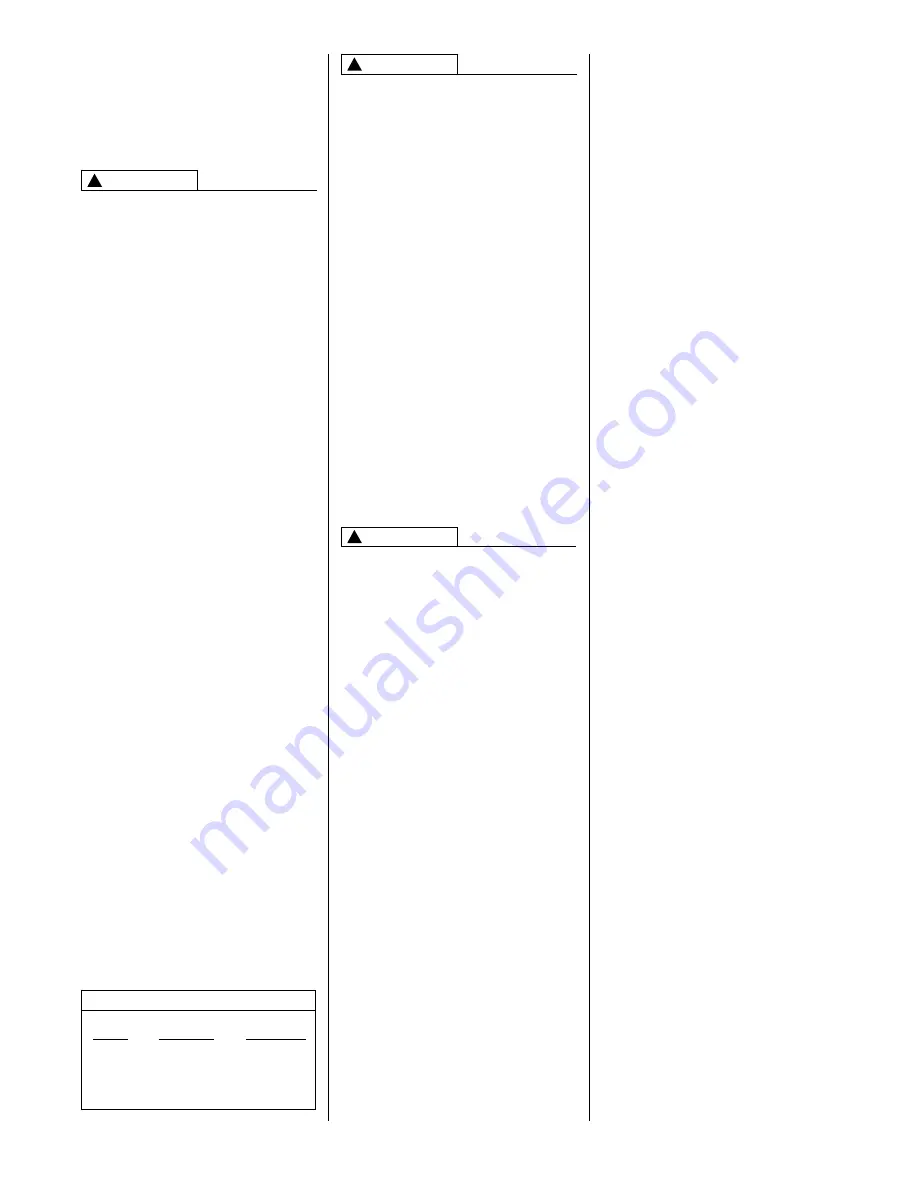
ACCESSIBILITY CLEARANCES,
WHERE GREATER, MUST TAKE
PRECEDENCE OVER FIRE
PROTECTION CLEARANCES.
UPFLOW AND HORIZONTAL
INSTALLATION —
Certified for use on
combustible floor.
FURNACES MUST NOT BE
INSTALLED DIRECTLY ON
CARPETING, TILE OR OTHER
COMBUSTIBLE MATERIAL OTHER
THAN WOOD FLOORING.
INSTALLATION ON A COMBUSTIBLE
MATERIAL CAN RESULT IN FIRE
CAUSING PROPERTY DAMAGE,
SEVERE PERSONAL INJURY OR
DEATH.
UNIT DESIGN IS CERTIFIED FOR
INSTALLATION ON NON-
COMBUSTIBLE FLOOR. A SPECIAL
COMBUSTIBLE FLOOR SUB-BASE IS
REQUIRED WHEN INSTALLING ON A
COMBUSTIBLE FLOOR. FAILURE TO
INSTALL THE SUB-BASE MAY
RESULT IN FIRE, PROPERTY
DAMAGE, PERSONAL INJURY OR
DEATH. THIS SPECIAL BASE IS
OFFERED AS AN ACCESSORY
FROM THE FACTORY. SEE THE
CLEARANCE LABEL LOCATED
INSIDE THE FURNACE FOR THE
APPROPRIATE MODEL NUMBER.
THE SPECIAL BASE IS NOT
REQUIRED WHEN THE FURNACE IS
INSTALLED ON TOP OF AN AIR
CONDITIONING PLENUM.
A gas-fired furnace for installation in a
residential garage must be installed so
that the burner(s) and the ignition source
are located not less than 18
(
above the
floor and the furnace is located or
protected to avoid physical damage by
vehicles.
UPFLOW UNIT DESIGN REQUIRES A
SOLID METAL BASE PLATE (SEE
TABLE ON PAGE 8 OR FURNACE
CLEARANCE LABEL FOR PART
NUMBER) MUST BE IN PLACE WHEN
THE FURNACE IS INSTALLED WITH
SIDE OR REAR AIR RETURN DUCTS.
FAILURE TO INSTALL A BASE PLATE
COULD CAUSE PRODUCTS OF
COMBUSTION TO BE CIRCULATED
INTO THE LIVING SPACE AND
CREATE POTENTIALLY
HAZARDOUS CONDITIONS,
INCLUDING CARBON MONOXIDE
POISONING.
furnace equals that which would
normally enter through the return air
intake of the furnace. Any duct opening
pulling return air from the outside must
not be any higher nor closer than 10 feet
to the furnace exhaust vent.
Install plenum chambers and air ducts in
accordance with the
Standard for the
Installation of Air Conditioning and
Ventilating Systems, NFPA No. 90A,
or
the
Standard for the Installation of Warm
Air Heating and Air Conditioning
Systems, NFPA No. 90B.
If the supply ducts carry air circulated by
the furnace to areas outside the space
containing the furnace, the return air
duct or ducts must be sealed to the
furnace casing and terminate outside the
space containing the furnace. If there is
no complete return air duct system, the
return air connection must be sealed to
the furnace casing and run full size to a
location outside the utility room or space
housing the furnace to prevent a
negative pressure on the venting
system.
DO NOT take return air from a
confined utility room containing
combustion producing appliances.
Any evaporator cooling coil must be
installed downstream of the furnace (at
the outlet end of the furnace) or in
parallel with the furnace to avoid
condensation on the heat exchanger.
If the furnace is installed parallel with a
cooling unit, a damper or other air flow
control must be installed to prevent
chilled air from entering the furnace. If
this device is manually operated, it must
have a means to prevent operation of
the other unit unless the damper is in the
full heat or cool position.
IMPORTANT:
One of the most common
causes of forced air heating problems is
insufficient return air to the furnace. The
return system area should be
approximately equal to or greater than
the area of the warm air discharge.
CONSULT LOCAL CODES FOR
SPECIAL REQUIREMENTS. Adjust the
blower speed to maintain the air
temperature rise range shown on the
rating plate.
NOTE:
The outlet duct from the furnace
should have a removable access panel.
It should be accessible after installation
to visually check the heat exchanger. It
also enables a service person to visually
check the air inlet side of an evaporator
coil for dirt, dust or other obstructions.
The total static pressure drop of the
entire system should not exceed 0.5
(
w.c.
IMPORTANT:
Some high efficiency
filters have a greater than normal
resistance to air flow. This can adversely
affect furnace operation. BE SURE TO
CHECK AIR FLOW if using any filter
other than the factory-provided filter.
When coils are used with air handlers
or furnaces and installed above a
finished ceiling or living area, it is
recommended that an auxiliary sheet
metal condensate drain pan be
fabricated and installed under entire
unit. Failure to do so can result in
property damage.
SITE SELECTION
1. Select a site in the building near the
center of the proposed, or existing,
duct system.
2. Give consideration to the vent
system piping when selecting the
furnace location. Be sure the venting
system can get from the furnace to
the termination with minimal length
and elbows.
3. Locate the furnace near the existing
gas piping. Or, if running a new gas
line, locate the furnace to minimize
the length and elbows in the gas
piping.
4. Locate the furnace to maintain
proper clearance to combustibles as
shown in the preceding tables.
COMBUSTIBLE MATERIAL MUST
NOT BE PLACED ON OR AGAINST
THE FURNACE JACKET OR WITHIN
THE SPECIFIED CLEARANCES OF
THE VENT PIPE. THE AREA
AROUND THE FURNACE MUST BE
KEPT CLEAR AND FREE OF ALL
COMBUSTIBLE MATERIALS
INCLUDING GASOLINE AND OTHER
FLAMMABLE VAPORS AND
LIQUIDS. PLACEMENT OF
COMBUSTIBLE MATERIALS ON,
AGAINST OR AROUND THE
FURNACE JACKET CAN CAUSE AN
EXPLOSION OR FIRE RESULTING IN
PROPERTY DAMAGE, PERSONAL
INJURY OR DEATH. THE
HOMEOWNER SHOULD BE
CAUTIONED THAT THE FURNACE
AREA MUST NOT BE USED AS A
BROOM CLOSET OR FOR ANY
OTHER STORAGE PURPOSES.
RETURN AIR DUCTING
AND SUPPLY
Return air may come from:
(1) outside the building, (2) return air
ducting from several inside rooms, or (3)
a combination of the two. When using
outside air, design and adjust the system
to maintain a return air temperature
above 50°F
during the heating season.
If return air comes from both inside and
outside the building, design the ducting
system with a diverting damper so that
the volume of return air entering the
7
CAUTION
!
WARNING
!
WARNING
!
TABLE 1
FURNACE
BASE
BASE
WIDTH
PLATE NO.
PLATE SIZE
14
(
RXGB-D14
11
5
⁄
8
(
x 23
9
⁄
16
(
17
1
⁄
2
(
RXGB-D17
15
1
⁄
8
(
x 23
9
⁄
16
(
21
(
RXGB-D21
18
5
⁄
8
(
x 23
9
⁄
16
(
24
1
⁄
2
(
RXGB-D24
25
5
⁄
8
(
x 23
9
⁄
16
(
Содержание 1x2000
Страница 20: ...20 FIGURE 16 UTEC NO 1095 100 CONTROL BOARD TWINNING CONNECTION SINGLE STAGE OPERATION I685 ...
Страница 21: ...21 FIGURE 17 UTEC NO 1095 100 CONTROL BOARD TWINNING CONNECTION TWO STAGE OPERATION I684 ...
Страница 29: ...29 FIGURE 25 FILTER RETAINING RODS SIDE RETURN FIGURE 26 DOWNFLOW FILTER INSTALLATION ...
Страница 31: ... FIGURE 27 INTEGRATED FURNACE CONTROL IFC TROUBLESHOOTING GUIDE FOR UTEC 1095 101 31 ...
Страница 32: ...32 ...
Страница 33: ... FIGURE 28 UTEC 1095 101 INTEGRATED FURNACE CONTROL 33 ...
Страница 34: ...34 ...
Страница 35: ...35 ...
Страница 36: ...36 CM 599 Rheem Manufacturing Company Air Conditioning Division Fort Smith Arkansas ...