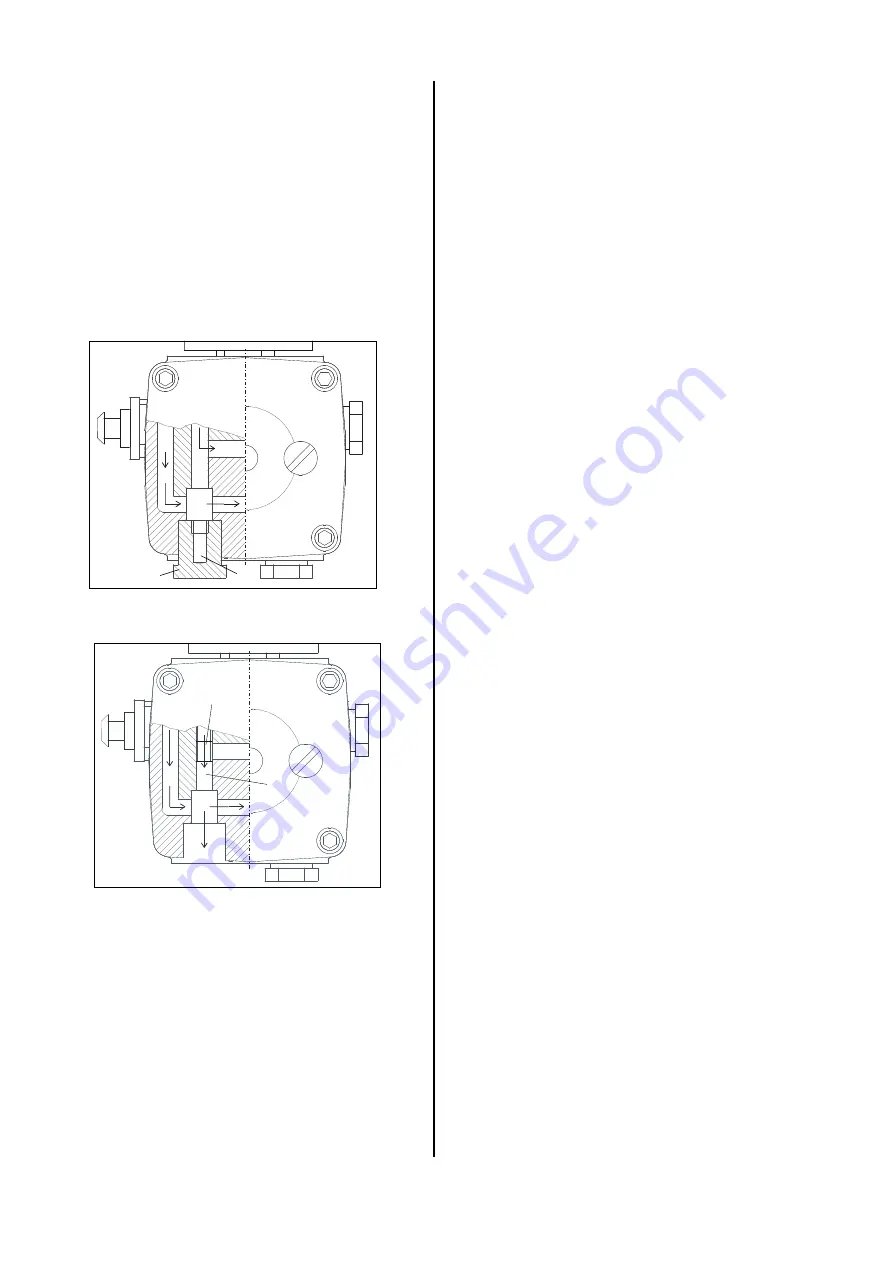
8
◊
The unit is to be kept free from dust and other de-
posits and is to be cleaned only with a dry or humid
cloth.
Do not use water jet.
◊
Do not use any aggressive cleaning agents or those
which are harmful or environmentally unfriendly.
◊
When the unit has not been used for a longer period,
the fuel tank is to be emptied, rinsed and to be filled
with clean fuel.
◊
Use only clean fuel oil EL and diesel, respectively.
Make sure to avoid paraffin formation.
◊
Empty fuel tank at least twice a year and rinse it with
clean fuel.
Do not use water!
◊
Keep burner head clean.
◊
Wearing parts such as e.g. oil filters, burner nozzle
and gaskets must be checked and, if necessary, re-
placed.
In any case, we recommend the replacement of the
oil jet before the start of each heating season.
◊
The oil filter in the filler neck of the fuel tank is to be
cleaned regularly.
◊
The main oil filter is to be replaced (take care of flow
direction) depending on the rate of pollution, but at
least before the start of every heating period.
The main filter is at the left side of the unit above the
fuel tank.
◊
Gauze oil filters have been installed in the fuel pump,
in the magnetic valve and in the burner nozzle.
These filters are to be cleaned by an expert.
◊
Check safety devices regularly.
◊
In the case of reducing heating capacity, formation of
smoke and/or bad ignition the unit is to be inspected
and the burner is to be adjusted.
◊
Observe regular maintenance and care intervals.
Maintenance and Service
The unit is to be maintained regularly whereby some
fundamental rules are to be observed to ensure a long
service life and trouble-free operation.
After each heating period or even earlier, depending on
the deployment conditions, the entire unit including
combustion chamber and burner head must be cleaned
of soot sediments, dust and dirt.
The oil filters must also be cleaned / replaced at least
once a year or, depending on the degree of contamina-
tion of the fuel, frequently.
G
Setting and maintenance is to be carried out
only by authorised personnel!
G
Prior to starting any work make sure to pull the
mains plug out of the mains socket!
Change the Pump to a 2
Pipe System
If an external fuel tank is used, the pump can be
changed to a system with 2 pipes. Fuel is fed to the
pump through the suction pipeline. Fuel which is not
needed flows back through the return pipe.
Please proceed in the following way to change to the
system with 2 trains of pipes:
1. Release fuel conduits and remove fuel pump.
2. Remove the screw
C
and screw the plug
D
out.
4. Screw the plug
D
for the bypass completely into the
opening
E
.
5. Replace the screw
C
by a connection fitting.
EDV No. 1102109.
6. Reinstall the fuel pump.
7. Replace the standard main oil filter by a special oil
filter for 2 pipes system (accessories).
8. Connect the flow and the return pipe of the fuel pipe
and link these with the 2 pipe oil filter.
For the first starting and after emptying the fuel tank the
fuel pump is automatically deaerated through the return
pipe.
D
E
D
C
3. Keep the screw
C
for a possible subsequent refitting
to a 1 pipe system.