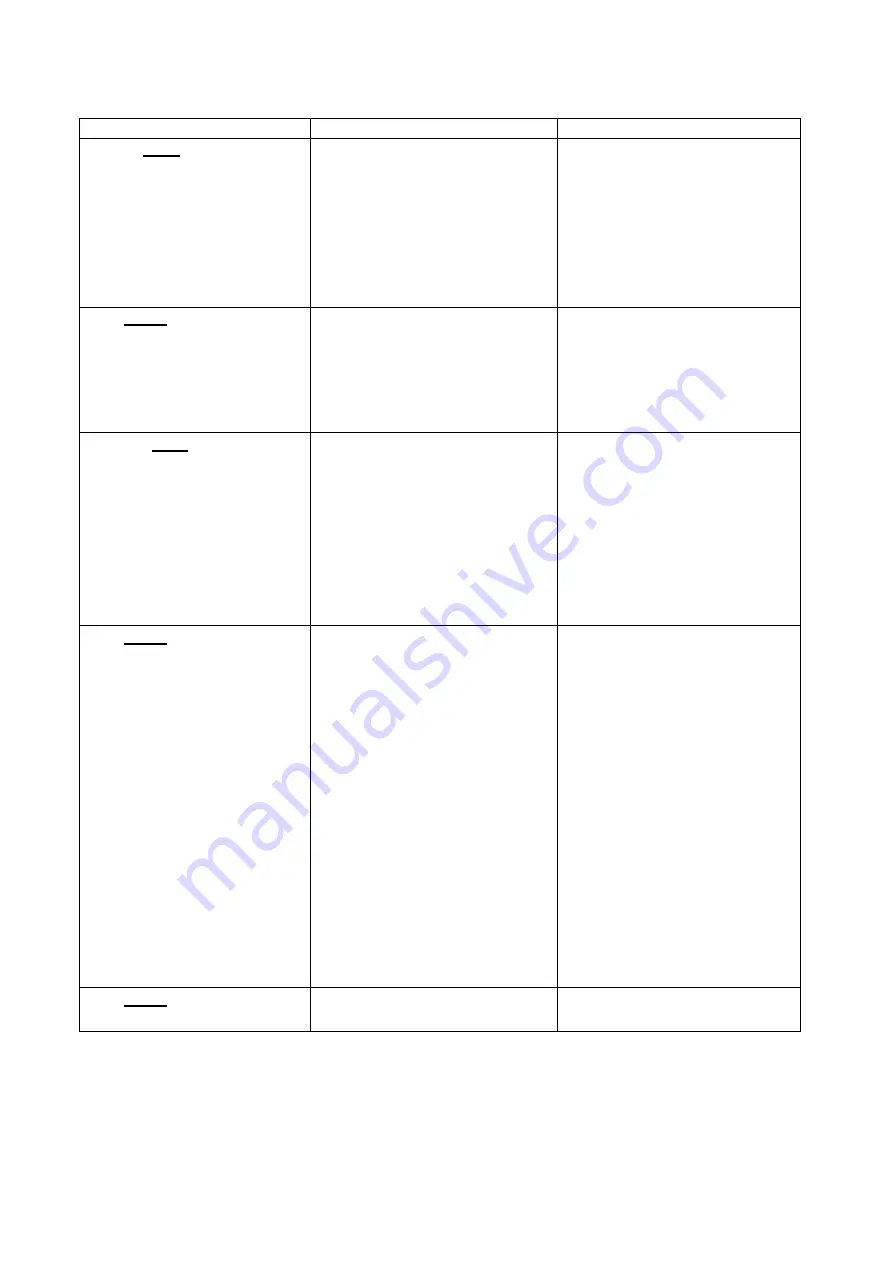
22
Fig. 12
Time schedule/frequency
Checkpoint/Lubrication point
Method
Prior to
each
use
-
Check for loose bolts / nuts.
-
Presence and legibility of
the safety stickers.
(Fig. 5)
-
Check the tension of the V-
belts.
-
Tighten the loose bolts /
nuts with the correct
moment.
-
Replace if not
present/damaged.
-
Adjust the tension of the V-
belts. Or replace the V-belts
where necessary.
After
every
use
-
Clean the machine.
-
Lubricate the rotor and
gearing bearings. (1) (See
fig.12)
-
Caution required with the
bearings if a high pressure
washer is used.
-
1 shot EP2
After the
first
20 operational
hours
(new or repaired)
-
Grease all lubricating points
(1&2) (See fig.12 )
-
Check the roller bearings
and the drive line.
-
Check for loose bolts / nuts.
-
Check the tension of the V-
belts.
-
1 shot EP2.
-
Check and replace if
necessary.
-
Tighten the loose nuts /
bolts.
-
Adjust the tension of the V-
belts. Or replace the V-belts
where necessary.
After
every
100 operation
hours or annually
-
Check the roller bearings
and the drive line.
-
Clean the sliding tubes (3)
and grease them.
-
Check for loose bolts / nuts.
-
Check the hydraulic
components are working
properly and for any
damage.
-
Check the tension of the V-
belts.
-
Check for oil leaks.
-
Check the oil level in the
gearbox.
-
Use EP2 lubricating grease
Replace if necessary.
-
Use lubricating grease
-
Tighten the loose nuts /
bolts.
-
Check and replace if
necessary.
-
Adjust the tension of the V-
belts. Or replace the V-belts
where necessary.
-
Repair or replace.
-
Use SAE 80W90 for the
gearbox.
After
every
500 operational
hours
-
Replace the oil in the
gearbox.
-
Use 1.7l (0.45 gallon) SAE
80W90
Used oil / grease constitutes an environmental hazard and must be disposed in accordance
with current regulations.
Содержание Turf Tidy 2300
Страница 10: ...10...
Страница 26: ...26 12 11 6 7 8 9 9 3 4 5 1 2 10 Fig 14...
Страница 29: ...29 Fig 16...