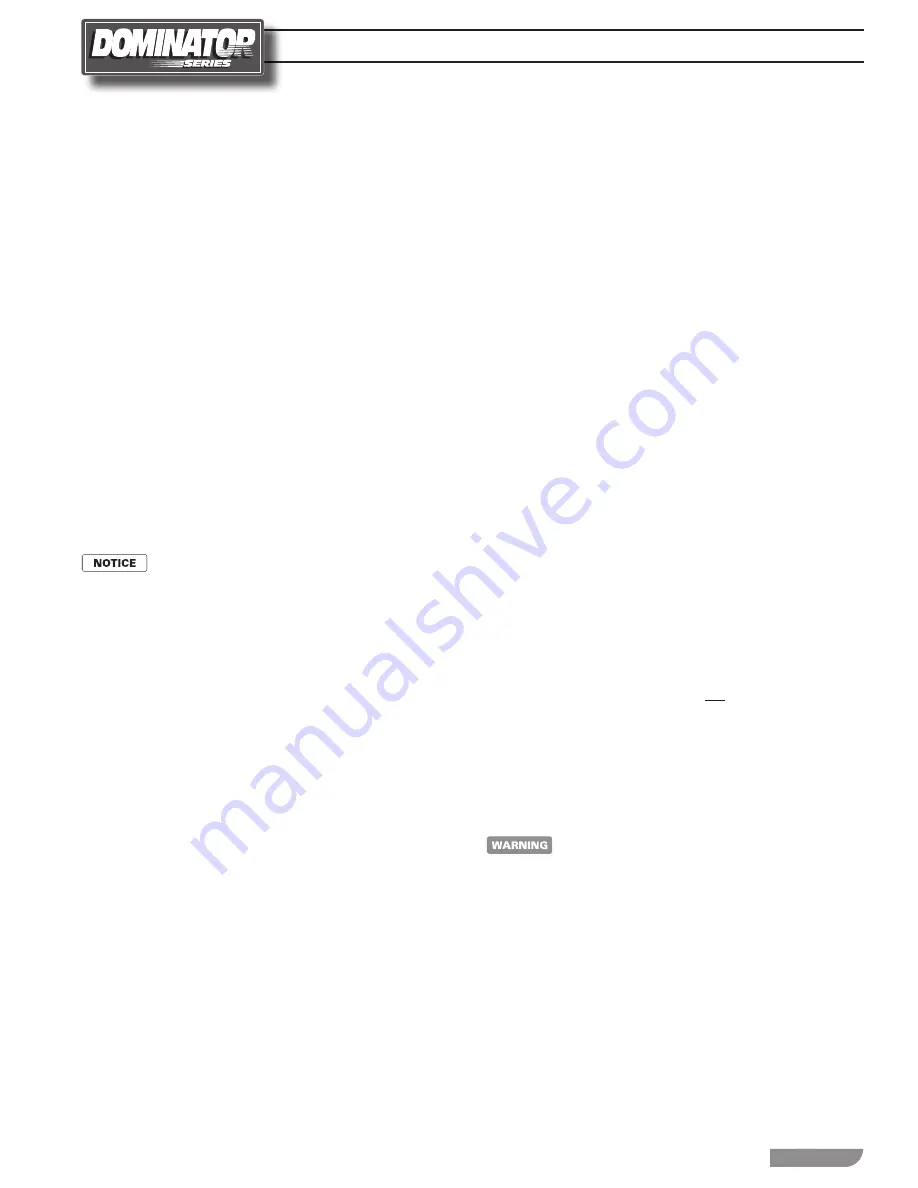
Finned copper tube gas boilers & water heaters – Boiler Manual
27
6. If the second ignition attempt is unsuccessful the gas valves will
lockout, but the blower, pump and power venter will remain
on. To reset the boiler/water heater, take one of the following
steps:
• Adjust the high limit down below the point at which the
blower shuts down, then reset the limit to its normal setting.
• Remove power from the boiler/water heater, wait 30 seconds
and re-establish power to the unit.
Main Burner:
1. Once the pilot is proved the MV terminal on (FSM) is energized
sending 24VAC to the main gas valve.
2. The main gas valve opens via action of K1.
3. The main burner indicator light illuminates. The PV terminal
remains energized and the pilot indicator remains on.
Normal Operation
• Staging will be controlled from the staging controller.
• The front control panel separately monitors limit, gas pressure,
water flow and air flow.
• If staging changes during operation, blowers, pres-sure switches
and gas valves will be switched or turned off as required.
• Stage 1 will be on first, last and whenever the boiler operates.
For a change from stage 2 to 3 or 3 to 4, 10 second
DOM time delays were added to the pressure switch
switching circuits (TDR2 and TDR3). The time delays
provide hold states that allow the blowers to reach full
speed and close the high fire pressure switches before
they are energized to confirm proper air flow.
Demand Satisfied:
1. Stage switch 1 opens, TDR1 de-energizes.
2. Power is removed from ignition module, blowers and power venter.
3. All indicators (except power) off.
4. Staging controller initiates a pump purge for 20 or more seconds,
depending on the inlet/outlet temperatures and ∆T setting in
the controller. The pump then shuts off.
Staging Control Alarms:
1. Staging control alarms are visible on the controller's LCD screen.
See the staging control documentation for details.
2. A powered alarm contact (2A max @ 24 VAC) is available to
provide an audio or visual indication of faults related only to
staging control operation. This contact is wired to the junction
box for optional remote indication. Refer to the 4-stage wiring
diagram for tie-ins.
High Limit, Low Water Flow, Low Gas Pressure, High Gas
Pressure, Power Venter Interlock Faults
1. All gas valves, the blowers and power venter will de-energize if
either alarm is tripped.
2. The manual reset high limit can be reset through a knockout
accessible in the left side jacket panel.
3. Condition indicators are visible on the control panel.
Low Air (Blocked Flue/Air Inlet)
• One of two pressure switches will monitor the airflow of each
blower.
• Air monitoring will begin at prepurge.
• If a low air condition is present on the left side, power will not be
supplied to the module. The blowers will remain on and the low
air indicator will remain on for as long as a call for heat exists.
• If a low air condition is present on the right side, power will not
be supplied to the right gas valve.
• A low air indicator for each boiler side is visible on the control
panel.
OPERATING INSTRUCTIONS
FOR YOUR SAFETY READ BEFORE OPERATING
POUR VOTRE SÉCURITÉ LISEZ AVANT DE
METTRE EN MARCHE
A. This appliance is equipped with an ignition device which
automatically lights the pilot. Do not try to light the pilot by
hand.
Cet appareil est muni d'un dispositif d'allumage qui allume
automatiquement la veilleuse. Ne tentez pas d'allumer la veilleuse
manuellement.
B. BEFORE OPERATING smell all around the appliance area
for gas. Be sure to smell next to the floor because some gas
is heavier than air and will settle on the floor.
Propane gas may not always be detected by smell.
Propane gas is heavier than air and can collect in low
areas.
Propane gas can ignite or explode if an ignition source is
present and result in death, serious injury and property
damage!