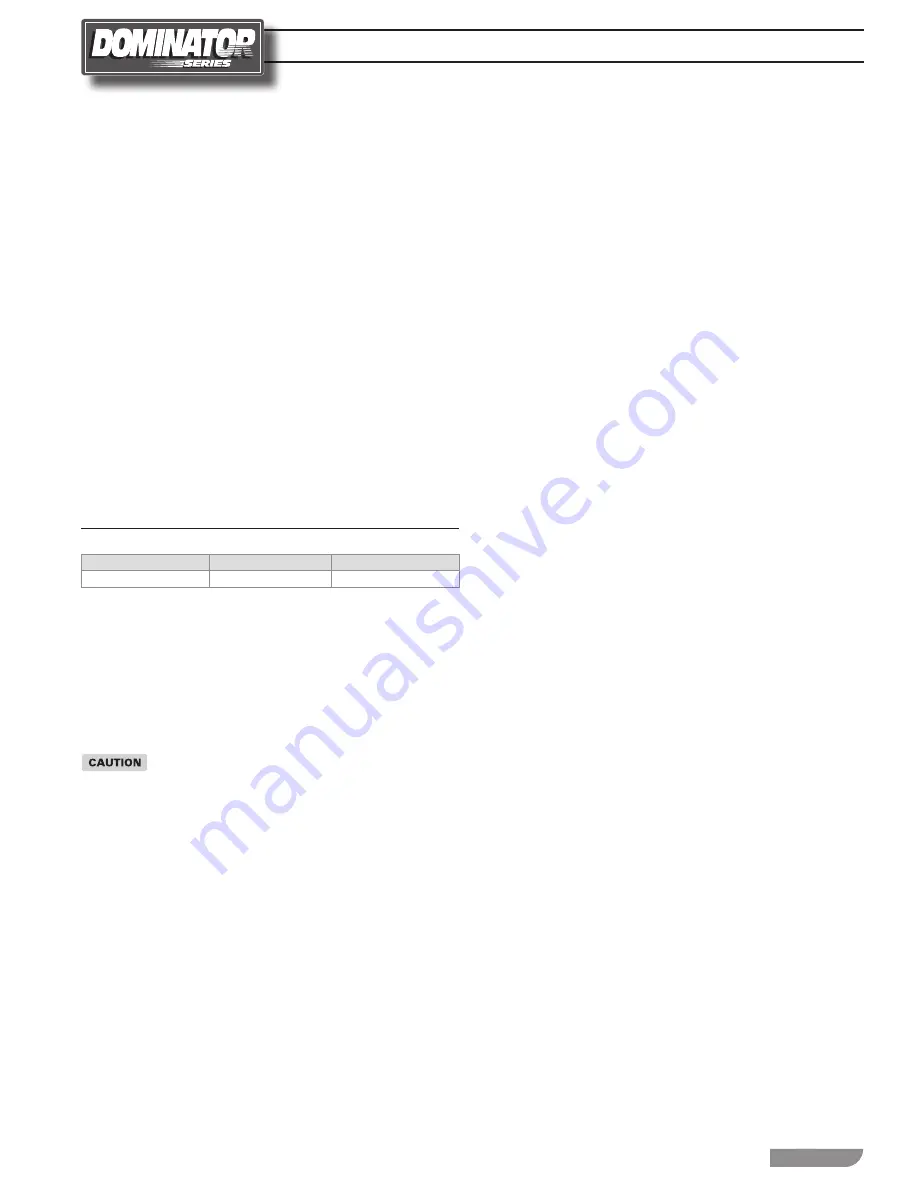
Finned copper tube gas boilers & water heaters – Boiler Manual
15
HEATING SYSTEM PIPING
General Piping Requirements
All heating system piping must be installed by a qualified technician
in accordance with the latest revision of the ANSI/ASME Boiler
and Pressure Vessel Code, Section IV, and, when required, ANSI/
ASME CSD-1, Standard for Controls and Safety Devices for
Automatically Fired Boilers. All applicable local codes and ordinances
must also be followed. A minimum clearance of
1 in
,
25 mm
must
be maintained between heating system pipes and all combustible
construction. All heating system piping must be supported by suitable
hangers not the boiler.
The thermal expansion of the system must be considered when
supporting the system. A minimum system pressure of
12 psig
,
82.7 kPa
must be maintained.
Heating Boiler Piping Connections
The supply and return piping should be sized to suit the system. The
supply and return connection sizes are listed in Table 8.
Table 8 Supply & Return Connection Sizes
Model Size
Supply Size
Return Size
300 thru 2100
2 1/2” NPT
2 1/2” NPT
Pump Requirements
This low mass boiler requires a continuous minimum water flow
for proper operation. The system pump must be sized to overcome
the head loss of the boiler and the heating system in order to achieve
the required temperature rise. Table 7 provides the heat exchanger
pressure drop and temperature rise figures. The temperature rise
across the boiler must never exceed
35°F
,
19.4°C
.
A temperature rise outside of the range listed in
Table 7 indicates that the flow rate through the
heat exchanger is incorrect which will damage the
heat exchanger voiding the warranty! The maximum
allowable temperature rise is
35°F
,
19.4°C
.
The maximum allowable flow rate through a Dominator
boiler with copper heat exchanger is
105 GPM
,
6.6 L/s
.
The cupro-nickel heat exchanger allows for
120 GPM
,
7.6 L/s
.
An adjustable pump delay is available as a feature of the staging
controller. The pump delay establishes water flow through the boiler
and heating system before the appliance starts. Consult the staging
controller manual for further details.
Low Water Cutoff
If a boiler is installed above any radiation elements it must be fitted
with a low water cutoff device.
Refer to wiring diagram supplied with the boiler/water heater for
proper wiring connections.
Expansion Tank & Air Separator
An expansion tank or other means to control thermal expansion
must be installed in the heating system. An expansion tank must
be installed close to the boiler on the suction side of the pump. An
air scoop and automatic air vent must also be installed to eliminate
air trapped in the system.
Primary/Secondary Piping
Boilers connected to heating systems using zone valves, zone pumps,
or systems that have excessive flow rates or return water temperatures
less than
125°F
,
52°C
must be isolated from these systems to protect
the boiler.
Variable Water Flows
Figure 11 shows a typical primary/secondary piping system. A
dedicated pump is used to maintain a constant water flow through
the boiler. This secondary pump is sized to overcome the head loss
of the boiler and secondary piping system while supplying the flow
rate required to maintain the desired temperature rise across the
boiler. The primary pump is sized to provide the required flow to
the heating system. The secondary piping connections to the primary
system piping must not be more than 6 pipe diameters apart to
ensure zero pressure drop in the primary system, see Figure 11.
Low Return Water Temperatures
To prevent the problems associated with condensation of the products
of combustion due to low return water temperatures a primary/
secondary piping system with a bypass and bypass valve must be
installed, see Figure 12 and 12A. The bypass and bypass valve must
be sized the same as the secondary piping. A balancing valve must
also be installed in the supply side of the secondary piping downstream
of the bypass. The balancing valve should be adjusted to divert some
of the heated discharge water into the return water until the required
inlet water temperature is achieved. The primary and secondary
pumps should be sized to provide the required flow through each
system. The secondary piping connections to the primary system
piping must not be more than 6 pipe diameters apart to ensure zero
pressure drop in the primary system, see Figure 12 and 12A.
Multiple Boiler Systems
Systems using multiple boilers can also be installed using a primary/
secondary manifold system, Figure 13.
Piping For Use With Cooling Units
The boiler, when used in connection with a refrigeration system,
must be installed so the chilled medium is piped in parallel with
the boiler. Appropriate valves must be used to prevent the chilled
water from entering the boiler.
When a boiler is connected to a heating coil that may be exposed
to refrigerated air from an air handling device, the piping system
must be equipped with flow-control valves or some other automatic
means of preventing gravity circulation of the boiler water during
the cooling cycle.