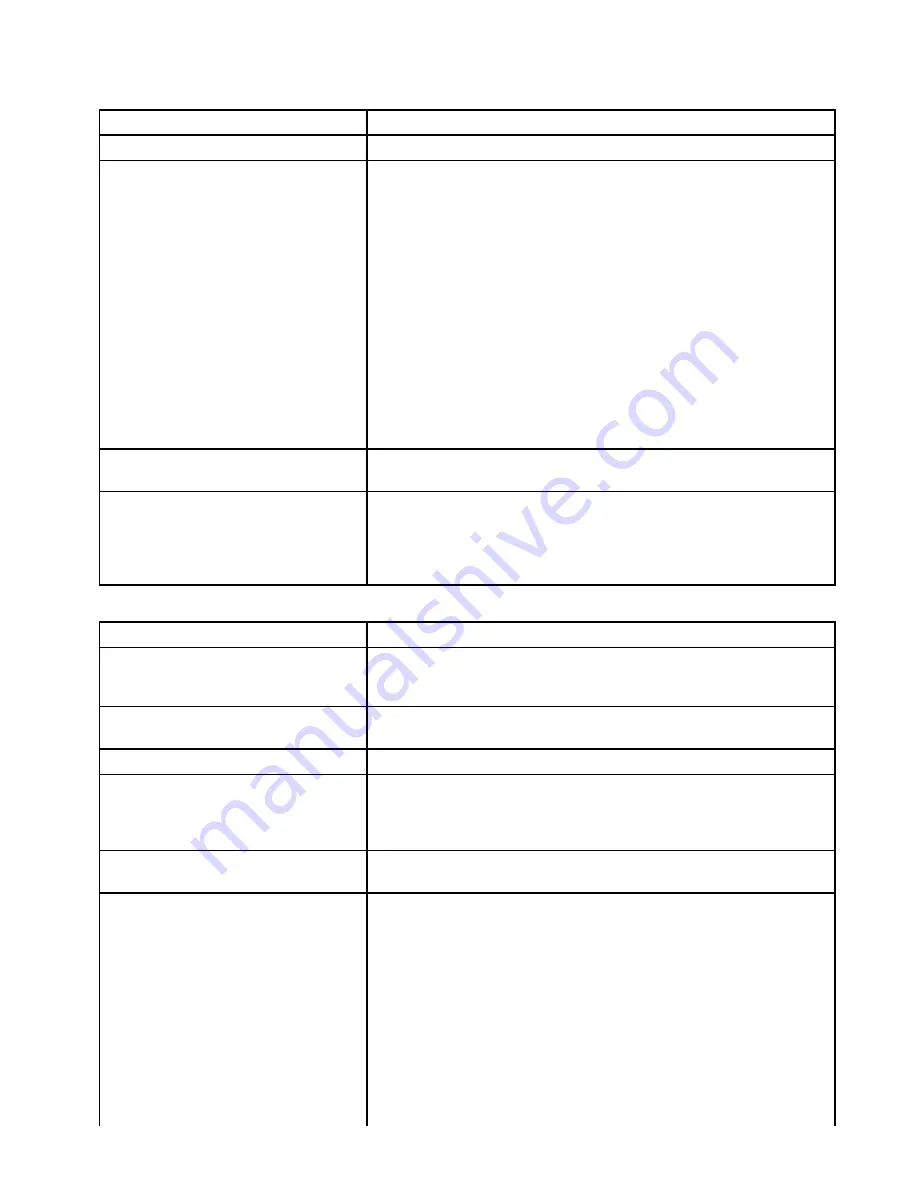
13.4 Sonar / DownVision troubleshooting
Problems with the Sonar or DownVision and their possible causes and solutions are described here.
Scrolling image is not being displayed
Possible causes
Possible solutions
Sonar disabled
Select
Enable Sonar
from the Shortcuts page.
Damaged cables
1.
Check the unit’s connector for broken or bent pins.
2.
Check that the cable connector is fully inserted into the unit and that the
locking collar is in the locked position.
3.
Check the power supply cable and connectors for signs of damage or
corrosion, replace if necessary.
4.
With the unit turned on, try flexing the power cable near to the display
connector to see if this causes the unit to re-boot/loose power, replace
if necessary.
5.
Check the vessel’s battery voltage, the condition of the battery terminals
and power supply cables, ensuring connections are secure, clean and free
from corrosion, replace if necessary.
6.
With the product under load, using a multi-meter, check for high voltage drop
across all connectors/fuses etc (this can cause the Fishfinder applications to
stop scrolling or the unit to reset/turn off), replace if necessary.
Damaged or fouled transducer
Check the condition of the transducer ensuring it is not damaged and is free from
debris/fouling, clean or replace as necessary.
Wrong transducer fitted
The
CPT-DV
transducer is a
DownVision
™
only transducer, you cannot use the
Sonar application with a
CPT-DV
transducer connected. If you have a
DVS
or
Pro
variant display ensure you are using a dual element transducer such
as the
CPT-DVS
.
Refer to
3.5
DownVision
™
transducer compatibility
for transducer compatibility.
No depth reading / lost bottom lock
Possible causes
Possible solutions
Transducer location
Check that the transducer has been installed in accordance with the transducer
location requirements (refer to
3.10 Selecting a location for the transducer
of
the manual for details).
Transducer angle
If the transducer angle is too great the beam can miss the bottom, adjust
transducer angle and recheck.
Transducer kicked-up
Check that the transducer hasn't kicked up due to hitting an object.
Power source insufficient
With the product under load, using a multi-meter, check the power supply
voltage as close to the unit as possible to establish actual voltage when the
current is flowing. (Refer to
Chapter 15 Technical specification
for power supply
requirements.)
Damaged or fouled transducer
Check the condition of the transducer ensuring it is not damaged and is free
from debris / fouling.
Damaged cables
1.
Check the unit’s connector for broken or bent pins.
2.
Check that the cable connector is fully inserted into the unit and that the
locking collar is in the locked position.
3.
Check the power supply cable and connectors for signs of damage or
corrosion, replace if necessary.
4.
With the unit turned on, try flexing the power cable near to the display
connector to see if this causes the unit to re-boot/loose power, replace
if necessary.
5.
Check the vessel’s battery voltage, the condition of the battery terminals
and power supply cables, ensuring connections are secure, clean and free
from corrosion, replace if necessary.
Troubleshooting
117