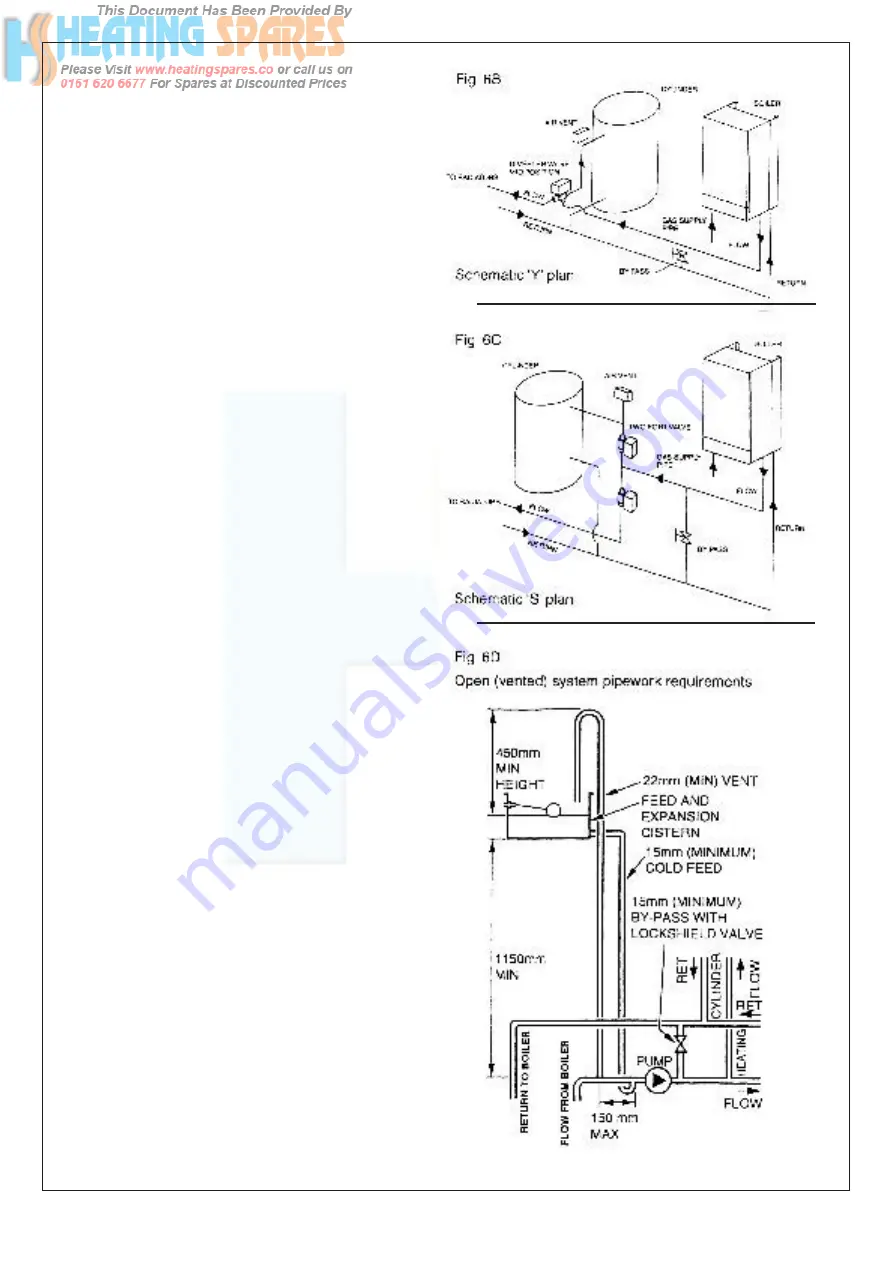
Supplied By www.heating spares.co Tel. 0161 620 6677
12
WATER
SYSTEM
4.8.2.1
WATER SYSTEM
For an open (vented) system the boiler
must be supplied from an unrestricted
water supply taken from a feed and expan-
sion tank (minimum 22 litre 5 gall)
capacity situated at a maximum
height of 27 5 metre (90ft) above
the boiler The cold feed supply must
be 15 mm minimum size It is impor-
tant that the relative positions of the
pump, cold feed and open vent See Fig
6D
4.8.2.2
CILINDER
The hot water cylinder must be a
double feed (fully indirect) type
4.8.2.3
SEALED WATER SYSTEMS
The installation should comply with
the appropriate requirements of BS5449
Part 1 and BS6798, see Fig 6E All valves
and fi t tings must be suitable for use on
sealed systems
4.8.2.4
SAFETY VALVE
The safety valve must be fi tted in a sealed
system The safety valve must conform
to BS6759 Part 1 and be fitted to the
require ments of BS6798
4.8.2.5
EXPANSION VESSEL
A diaphragm type expansion vessel,
con forming to BS4814 must be connected
at a point close to the inlet side of the
circulating pump, see Fig 6E or as laid
down by the manufacturer
The expansion vessel must suit the volume
of water in the system, see
BS5449 Part 1
clause 25 for details The charge pressure
must not be less than static head i e
the height of the highest point of the
system ABOVE the expansion vessel
The expansion vessel should have
suffi cient capacity to accept the volume
change when the water is heated from 10
°C to 110 °C Refer to BS5449 Part 1
for specific details See Table 3
4.8.2.6
PRESSURE GAUGE
A pressure gauge with set pointer and cov-
ering at least the range 0 to 4 bar (0 to 60
lb/in
2
) shall be permanently fi tted to the sys-
tem in a position it can be seen when carry-
ing out the fi lling operation
4.8.2.7
SYSTEM DESIGN
Fig 6A illustrates typical heating only lay -
out Figs 6B and 6C illustrate typical layout
with ‘Y’ or ‘S’ plan system
4.8.3
The water through the appliance heat
exchanger circuit must exceed the min 1 84
gals min (503 It/h) when the burner is fi ring
It is important to ensure that this rate is
achieved when sections of the system are
shut off either manually or bu automatic
Содержание HE Primary AAA
Страница 16: ...Supplied By www heating spares co Tel 0161 620 6677 17 Fig 18...
Страница 31: ...Supplied By www heating spares co Tel 0161 620 6677 Fig 58 32 Fig 56 Fig 57...
Страница 33: ...Supplied By www heating spares co Tel 0161 620 6677 34 Fig 60 Fig 61 Fig 62 Fig 63...
Страница 36: ...Supplied By www heating spares co Tel 0161 620 6677 Section 9 ELECTRICAL SYSTEM DIAGRAM Fig 94 37...
Страница 42: ...Supplied By www heating spares co Tel 0161 620 6677 section 10 EXPLODED PARTS DIAGRAM 43...