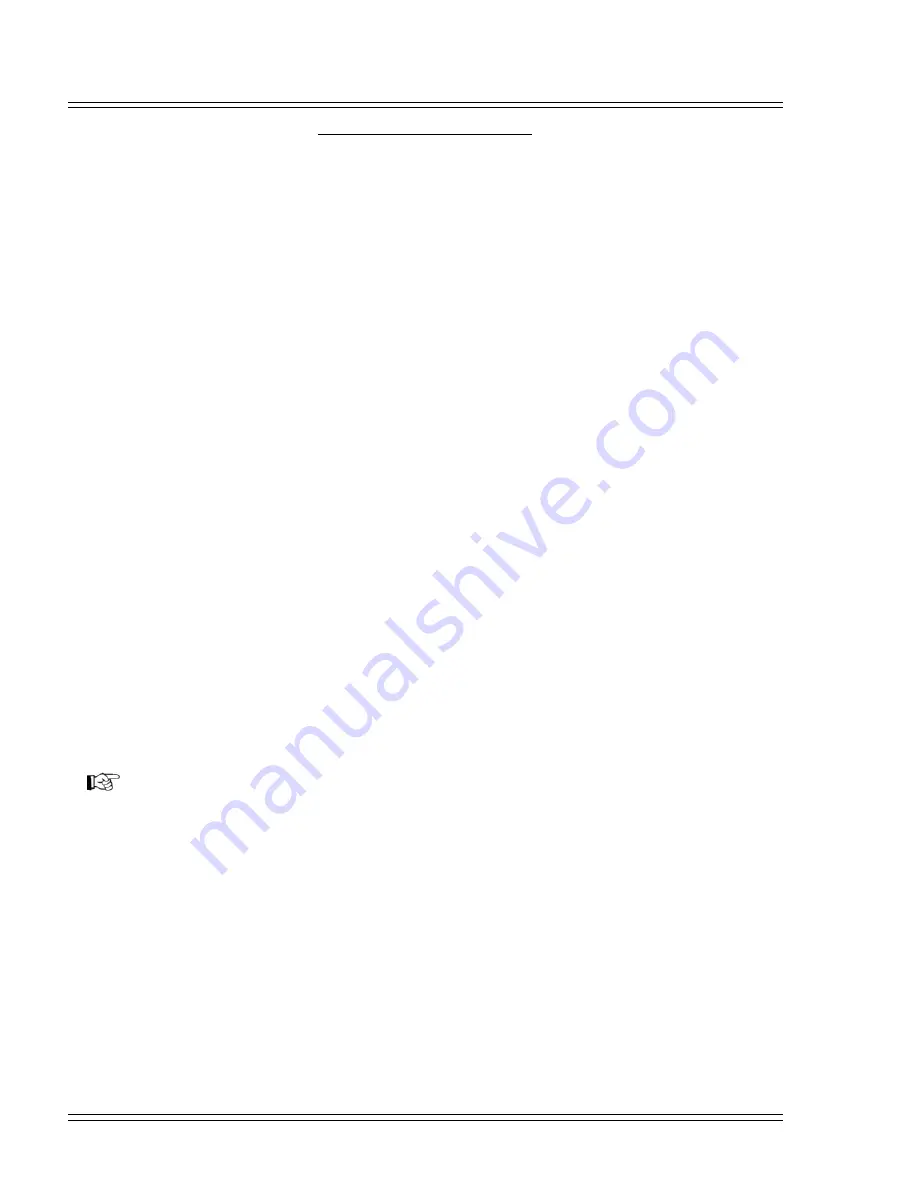
Section I - General
1A
Quincy Compressor-QSI
®
Royal Blue Warranty (continued)
Seller’s sole obligation on this warranty shall be, at
its option, to repair, replace or refund the purchase
price of any product or part thereof which proves to
be defective. If requested by Seller, such product
or part thereof must be promptly returned to Seller,
freight collect for inspection.
Seller warrants factory repaired or replaced parts of
its own manufacture against defects in material and
workmanship under normal use and service for ninety
(90) days or for the remainder of the warranty on the
product being repaired, whichever is longer.
This warranty shall not apply and Seller shall not be
responsible nor liable for:
a) Consequential, collateral or special losses or
damages;
b) Equipment conditions caused by fair wear and
tear, abnormal conditions of use, accident,
neglect or misuse of equipment, improper stor-
age or damages resulting during shipment;
c) Deviation from operating instructions, specifi-
cations, or other special terms of sales;
d) Labor charges, loss or damage resulting from
improper operation, maintenance or repairs
made by person(s) other than Seller or Seller’s
authorized service station.
e) Improper application of product.
In no event shall Seller be liable for any claims,
whether arising from breach of contract or warranty
of claims of negligence or negligent manufacture, in
excess of the purchase price.
Only genuine Quincy Compressor maintenance and
replacement parts may be used on the compressor.
Normal rules of warranty apply regardless of coverage
length. Inlet valves, fluid pumps and shaft seals are
covered by the standard (1 year) warranty terms and
are not included in the Royal Blue Warranty program.
The Royal Blue Warranty is non-transferable.
The customer and/or Quincy Distributor must keep
copies of all maintenance records, parts purchases
and sampling reports. The following records will be
required for warranty airend replacement and/or
warranty claim consideration and should be submitted
to the Quincy Compressor Customer Service
Department:
Ø
A completed Airend Failure Information form.
Ø
A copy of the Royal Blue Warranty Registration/
Agreement form.
Ø
Copies of all maintenance logs for the unit.
Ø
Proof of purchase of genuine Quincy parts and
fluids.
Ø
Copies of all fluid analysis reports.
Notice of the alleged defect must be given to Seller
in writing with all identifying details including serial
number, model number, type of equipment and date
of purchase, within thirty (30) days of the discovery of
same during the warranty period.
NOTICE!
Quincy Compressor reserves the right to modify or withdraw this Royal Blue Warranty program at any
time on units not already covered by this ROYAL BLUE WARRANTY program.
Updated Warranty 10/01/2008.
Содержание QSI 1000
Страница 2: ......
Страница 7: ...This page intentionally left blank ...
Страница 11: ...Section I General Quincy Compressor QSI 5 MODEL IDENTIFICATION ...
Страница 25: ...Quincy Compressor QSI 19 THIS PAGE INTENTIONALLY LEFT BLANK ...
Страница 65: ...Quincy Compressor QSI 59 THIS PAGE INTENTIONALLY LEFT BLANK ...
Страница 66: ...Appendix A Dimensional Drawings 60 Quincy Compressor QSI QSI 220 245 air cooled ...
Страница 67: ...Appendix A Dimensional Drawings Quincy Compressor QSI 61 QSI 220 245 water cooled ...
Страница 68: ...Appendix A Dimensional Drawings 62 Quincy Compressor QSI QSI 250 300 air cooled ...
Страница 69: ...Appendix A Dimensional Drawings Quincy Compressor QSI 63 QSI 250 300 water cooled ...
Страница 70: ...Appendix A Dimensional Drawings 64 Quincy Compressor QSI QSI 335 370 air cooled ...
Страница 71: ...Appendix A Dimensional Drawings Quincy Compressor QSI 65 QSI 335 370 water cooled ...
Страница 72: ...Appendix A Dimensional Drawings 66 Quincy Compressor QSI QSI 440 500 air cooled ...
Страница 73: ...Appendix A Dimensional Drawings Quincy Compressor QSI 67 QSI 440 500 water cooled ...
Страница 74: ...Appendix A Dimensional Drawings 68 Quincy Compressor QSI QSI 540 600 air cooled ...
Страница 75: ...Appendix A Dimensional Drawings Quincy Compressor QSI 69 QSI 540 600 water cooled ...
Страница 76: ...Appendix A Dimensional Drawings 70 Quincy Compressor QSI QSI 675 750 air cooled ...
Страница 77: ...Appendix A Dimensional Drawings Quincy Compressor QSI 71 QSI 675 750 water cooled ...
Страница 78: ...Appendix A Dimensional Drawings 72 Quincy Compressor QSI QSI 925 1000 air cooled ...
Страница 79: ...Appendix A Dimensional Drawings Quincy Compressor QSI 73 QSI 925 1000 water cooled ...
Страница 80: ...Appendix A Dimensional Drawings 74 Quincy Compressor QSI QSI 1175 1250 1400 1500 air cooled ...
Страница 81: ...Appendix A Dimensional Drawings Quincy Compressor QSI 75 QSI 1175 1250 1400 1500 water cooled ...
Страница 99: ......