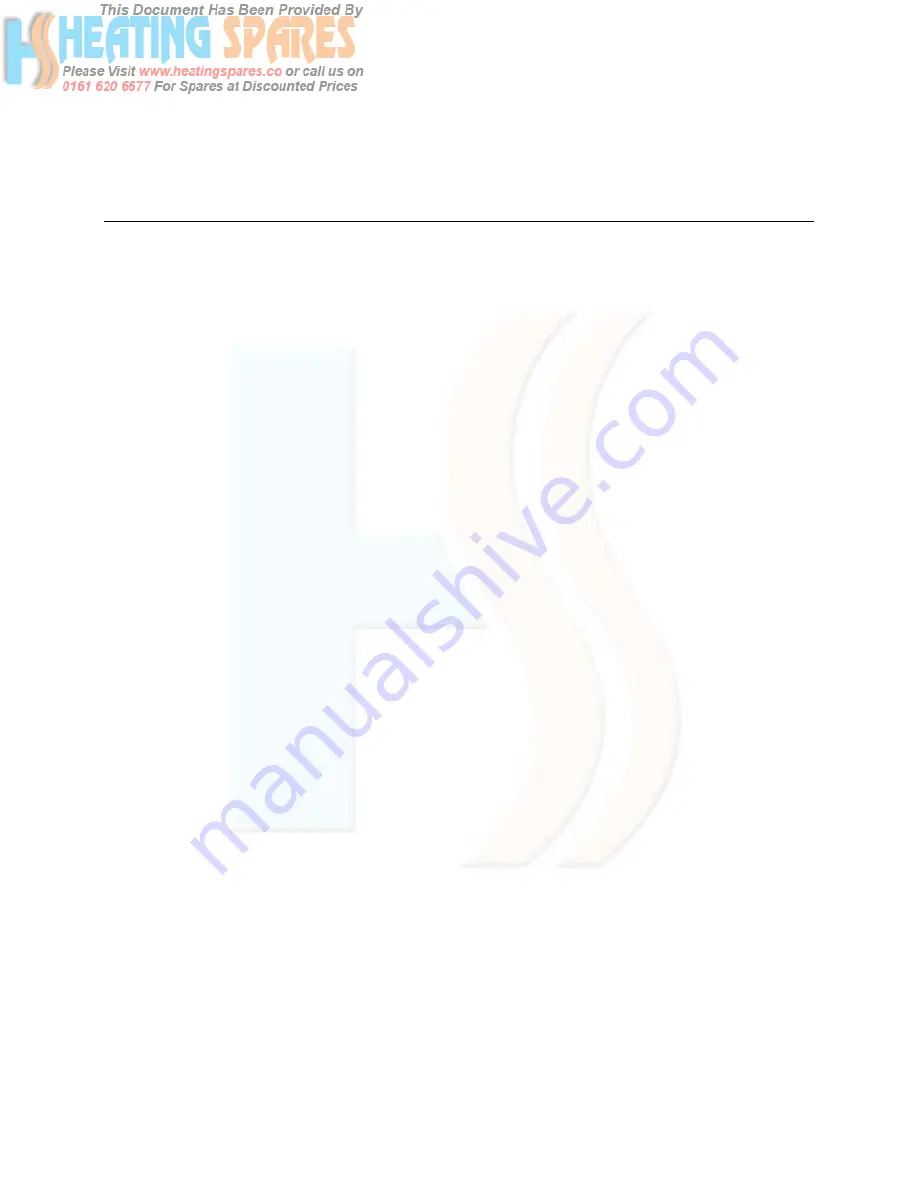
Supplied By www.heating spares.co Tel. 0161 620 6677
The following instructions are for specialised professionals only. Together with
the "Instructions for Use" and the "Service Booklet," technical instructions
for installation, setting and maintenance are provided.
Numbers and headings of the chapters are the same as in the "Instructions for Use"
3. Boiler Assembly
When servicing the boiler that is plugged into the electrical grid (even if the main switch is off), all safety precautions for work on
electric equipment must be adhered to.
The boiler casing can be dismounted. The top and front cover panels are removable, fixed by spring clamps in their corners. The
front panel is removed by pulling forward, the top panel by pulling upward. Removal requires overcoming the force of the spring
clamps. The remaining casing panels are fixed to the body by pins and bolts. All parts of the casing are connected to the boiler
electrical installation by protective wires.
The pipe connections of the boiler (water or gas) should never be used as manipulation handles!!!
3.7. Heating System – Properties and Filling
The emergency thermostat settings must be adjusted according to the type of the expansion vessel used (closed or open): for open
to 95°C, for closed to 110°C.
The HCW regulator must be pre-set to max. 85°C for open vessels, to prevent undesirable overlapping of temperature ranges
caused by value tolerances and adversary responses of the emergency thermostat.
The range of the HCW operation regulator is done by a locking wire clamp, which is in the bottom part of the regulator's knob.
The clamp is accessible when the knob is taken off the thermostat shaft. The setting must be verified by an operational test.
After filling the heating system with water, purging and setting the pressure expansion vessel (if there is one), the final HCW
pressure value is set by the red needle on the boiler pressure gauge.
3.9. Electrical Connections of Boiler
The electrical installation cabinet and the service part of the control panel are accessible when the top panel of the boiler is
removed. The front part of the cabinet consists of the control panel, fixed by two screws. When the panel is tilted forward, the
terminal board for connection of eternal equipment becomes accessible. The panel remains connected to the boiler by the wires
and tubes of the measurement devices.
If the boiler is to be operated with a room thermostat, the jumper between the contacts on the terminal board is removed;
otherwise the jumper must remain on the board.
A room thermostat is connected by a power cable to contacts No. Pr 19 and 20 – the recommended cross-section of the cable
wires is between 0.5 and 1.5 mm
2
.
The no-voltage rule must be fulfilled by the room thermostat regulator!
If a bimetal regulator is used, which requires 230 V supply for its function, then the phase (L) and null (N) contact of the regulator
are connected to Pr 19 and N contacts on the boiler terminal board; the output contact of the regulator is connected to Pr 20 on the
boiler terminal board. The minimum allowed load of the regulator's contacts should be 230 V A.C. /2A (inductive load).
Pump connection
– if the load is higher than the value allowed by the fuse of the boiler, an additional switching element
(contactor) must be used.
Connections of parts for cooperation with external DHW reservoir
(i.e., electric-motor-driven three-way valve and reservoir
thermostat) – they have to be connected to the boiler terminal board: the middle switching contact of the reservoir is connected to
TbC (No. 6). The outside contacts are connected to Tb1 and Tb2 (No. 7 and 8) so that TbC and Tb1 have conductive connection
when the DHW is cold in the reservoir. The three-way valve drive is connected to N (No. 10) and L (No. 11) contacts; the
switching contact of the three-way valve (only for 20, 30, 40, 50 KLO) is connected to W1, W2 (No. 12, 13). The contact must be
interconnected when the valve's drive has no voltage.
15