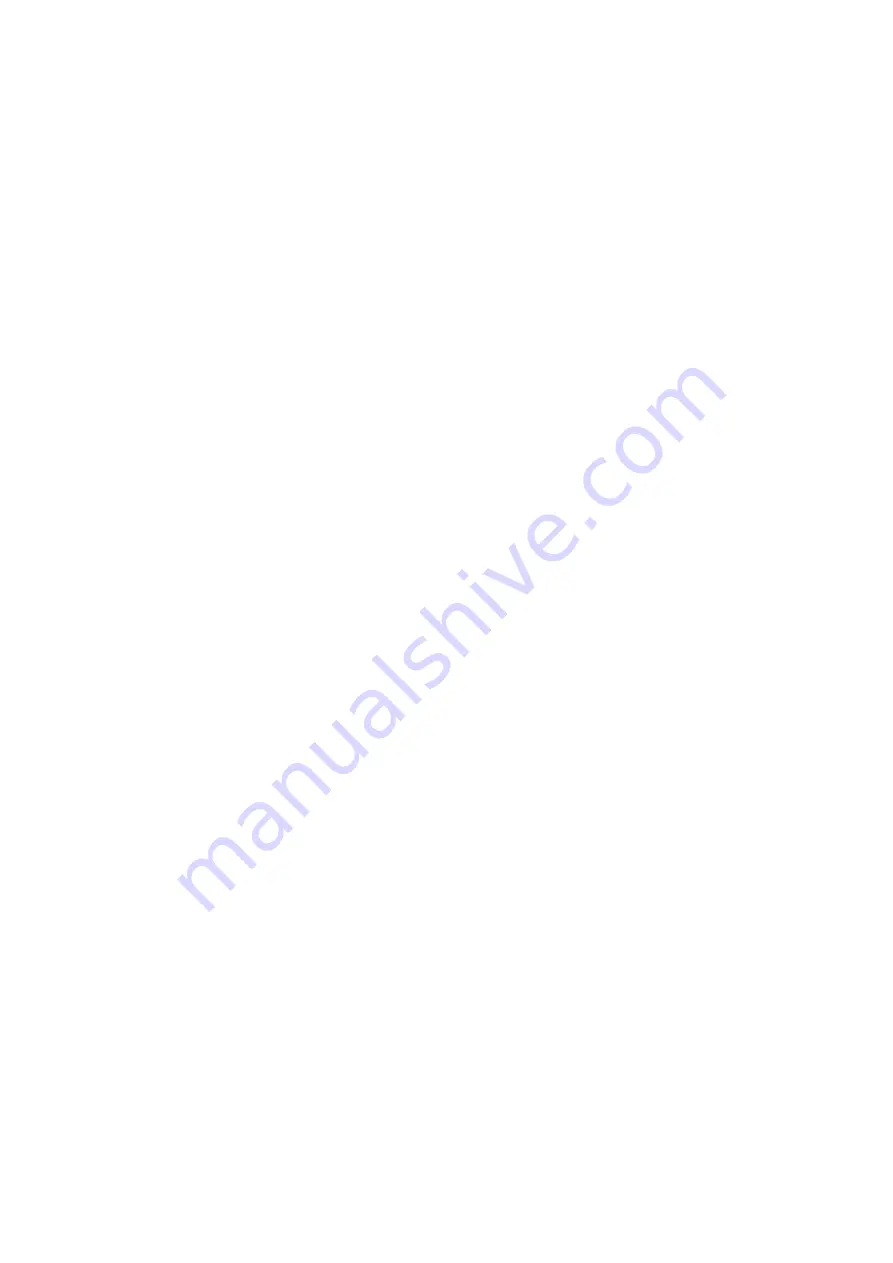
DIRECTIONS USED IN THIS OPERATOR'S MANUAL
Left side – side to the left hand of the operator facing in the direction of machine's forward
travel.
Right side – side to the right hand of the operator facing in the direction of machine's forward
travel.
REQUIRED SERVICE ACTIONS
Service actions described in the manual are marked:
Result of service/adjustment actions or comments concerning the performance of actions are
marked:
Содержание T285/1
Страница 2: ......
Страница 6: ......
Страница 11: ...SECTION 1 BASIC INFORMATION ...
Страница 26: ...Pronar T285 1 SECTION 1 1 16 ...
Страница 27: ...SECTION 2 SAFETY ADVICE ...
Страница 42: ...Pronar T285 1 SECTION 2 2 16 ...
Страница 43: ...SECTION 3 DESIGN AND OPERATING PRINCIPLE ...
Страница 64: ...Pronar T285 1 SECTION 3 3 22 ...
Страница 65: ...SECTION 4 CORRECT USE ...
Страница 91: ...SECTION 5 MAINTENANCE ...
Страница 124: ...Pronar T285 1 SECTION 5 5 34 FIG 5 13 Trailer s lubrication points part 1 ...
Страница 125: ...SECTION 5 Pronar T285 1 5 35 FIG 5 14 Trailer s lubrication points part 2 ...
Страница 134: ...Pronar T285 1 SECTION 5 5 44 ...
Страница 135: ...NOTES ...
Страница 136: ......