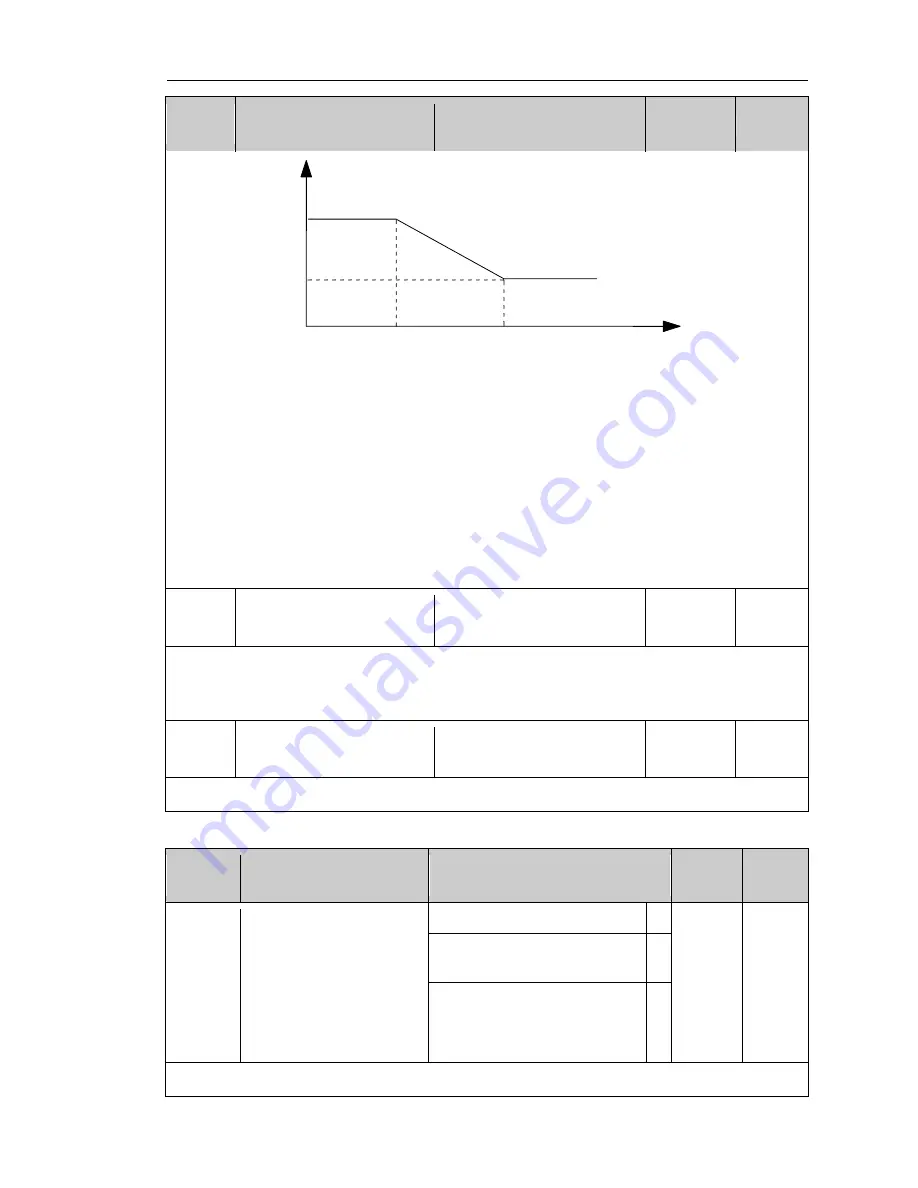
Chapter 5 Function parameter
65
Code
Parameter name
Setting range
Factory
default
Change
By setting the proportional coefficient and integral time of speed regulator, you
can adjust the characteristics of speed loop dynamic response of vector control.
Increasing the proportional gain as well as decreasing integral time, which can
accelerate the speed loop dynamic response, but the too large proportional gain is or the
too small integration time easily cause system oscillation and too large overshoot. The
too small proportional gain also easily lead to the system steady-state oscillation, and
the speed static difference may exist.
Speed loop PI parameters are closely related to and the inertia of system, shall be
adjusted based on the default PI parameters especially for different load needs, in order
to meet the needs of a variety of occasions.
F5.06
VC slip compensation
coefficient
50% to 200%
100%
☆
Slip compensation coefficient is used to adjust the slip frequency of vector control,
improve the accuracy of system speed control, if the parameter is appropriately
adjusted, the speed static difference can be effectively suppressed.
F5.07 Torque upper limit setting
0.0 to 200.0% (rated
inverter current)
150.0%
☆
Set the inverter rated output current corresponding to 100.0%.
5-2-8.F6 Group - Keyboard and display group
Code
Parameter name
Setting range
Factory
default
Change
F6.00
STOP/RESET key stop
function selection
Valid only for panel control 0
0
☆
Valid for both panel control
and terminal control
1
Valid for both panel control
and communication control
2
Valid for all control modes
3
As for fault reset, STOP/RESET key is valid at any situation.
F5.00
,
F5.01
PI
parameters
Frequency
command
F5.02
F5.05
F5.03
,
F5.04
Schematic diagram of PI parameters