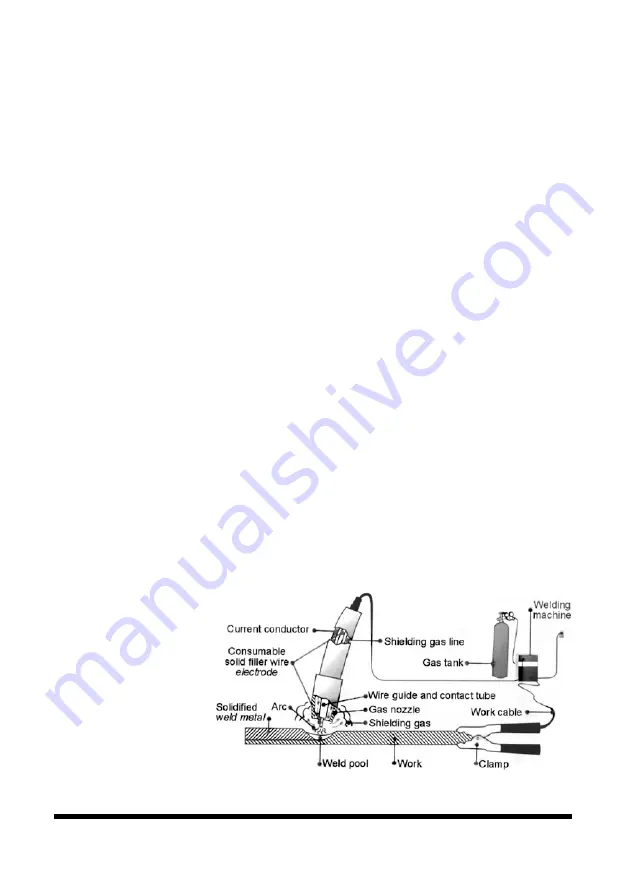
8785115
200A Multi-Process Welder with LCD Display
V4.0
32
For technical questions call 1-800-665-8685
ELECTRODE ANGLE
The angle that the electrode has in relation to the work is important to ensure a
smooth, even transfer of metal. When welding down hand, fillet, horizontal or
overhead the angle of the electrode is generally between 5 and 15 degrees towards
the direction of travel. When vertical up welding the angle of the electrode should be
between 80 and 90 degrees to the workpiece.
TRAVEL SPEED
Move the electrode along the joint length at a speed that allows the weld to penetrate the
base metal and form a good weld pool. Feed the electrode downwards at the same time
to maintain the correct arc length. Excessive travel speeds lead to poor fusion, lack of
penetration etc., while too slow a rate of travel will frequently lead to arc instability, slag
inclusions and poor mechanical properties.
MATERIAL AND JOINT PREPARATION
Clean the material being welded. Remove any moisture, paint, oil, grease, mill
scale, rust or other material that will hinder the arc and contaminate the weld
material. Joint preparation will depend on the method used include sawing,
punching, shearing, machining, flame cutting and others. In all cases, edges
should be clean and free of any contaminates. The type of joint will be
determined by the chosen application.
MIG (METAL INERT GAS) WELDING
MIG (metal inert gas) welding, also known as GMAW (gas metal arc welding) or
MAG (metal active gas welding), is a semi-automatic or automatic arc welding
process in which a
continuous and
consumable wire
electrode and a
shielding gas are fed
through a welding
torch. A constant
voltage, direct current
power source is most
commonly used with
MIG welding.
Fig. 17