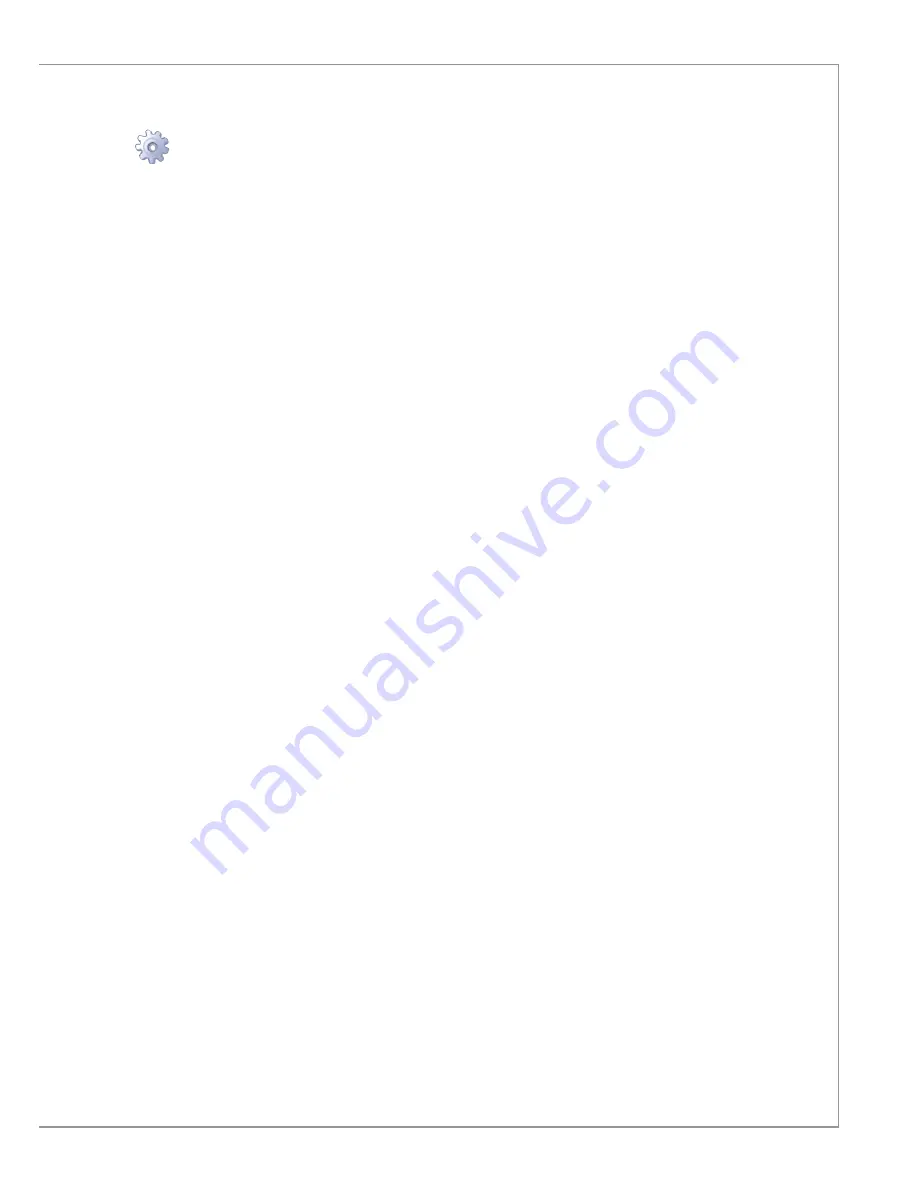
Installation, user and maintenance manual
– GAHP-A
45
To connect the CAN bus cable to a DDC:
You will need:
DDC to be electrically isolated.
1. Depending on the type of node being confi gured, set the DDC's jumpers J21
as shown in detail "A" or detail "B" in Figure 5.10 detail wires and jumpers J21 -
terminal/intermediate node DDC on page 46. If necessary, open the DDC's back
pa nel (4 screws); after jumpers J21 have been correctly positioned, close the cover
again and retighten the 4 screws.
•
If the DDC is an
intermediate node
on the network (with no. 6 wires in the orange
connector "P8"): set the jumpers "J21" as shown in detail "B" of Figure 5.10 detail
wires and jumpers J21 - terminal/intermediate node DDC on page 46: Jumpers
OPEN.
•
If the DDC is an
terminal node
on the network (with no. 3 wires in the orange con-
nector "P8"): set the jumpers "J21" as shown in detail "A" of Figure 5.10 detail wires
and jumpers J21 - terminal/intermediate node DDC on page 46: Jumpers CLOSED.
2. Prepare the orange CAN bus connector, from the supplied sleeve.
3. Cut a length of cable, long enough to allow it to be installed without kinking.
4. Remove the sheath for a length of approximately 70-80 mm, taking care not to
cut the shielding (metallic shield and/or aluminium sheet and, if present, the bare
connector in contact with the shield) and wires contained inside.
5. Roll the shielding and connect it to a 4-mm eyelet terminal, as illustrated in Figure
5.9 Connection from CAN BUS to connector P8 on page 46, details C and D. Now
proceed as follows:
6. If the DDC is an
terminal node
connect the three coloured wires to the orange
connector "P8", following the diagram provided in detail "A" of Figure 5.10 detail
wires and jumpers J21 - terminal/intermediate node DDC on page 46. Observe the
terminal markings L, H, GND (on the DDC at the base of the socket "P8") which are
given both in Table 5.2 CAN BUS cables type on page 42 and in the example.
7. If the DDC is an
intermediate node
repeat the operations from step 2 to step 4
for the other length of CAN bus cable required. Connect the six coloured wires to
the orange connector "P8", following the diagram provided in detail "B" of Figure
5.10 detail wires and jumpers J21 - terminal/intermediate node DDC on page 46.
Observe the terminal markings L, H, GND (on the DDC at the base of the socket
"P8") which are given both in Table 5.2 CAN BUS cables type on page 42 and in the
example.
8. Insert the orange connector ("P8") with the wires fi rst into the opening prepared
in the cover of the DDC, and then into the appropriate socket on the DDC itself,
making sure it is correctly inserted.
9. Use the rear cover bolts located near the CAN BUS socket to secure the 4 mm eyelet
(or 2 eyelets) (detail D, Figure 5.9 Connection from CAN BUS to connector P8 on
page 46). The cable should be secured against pulling out.