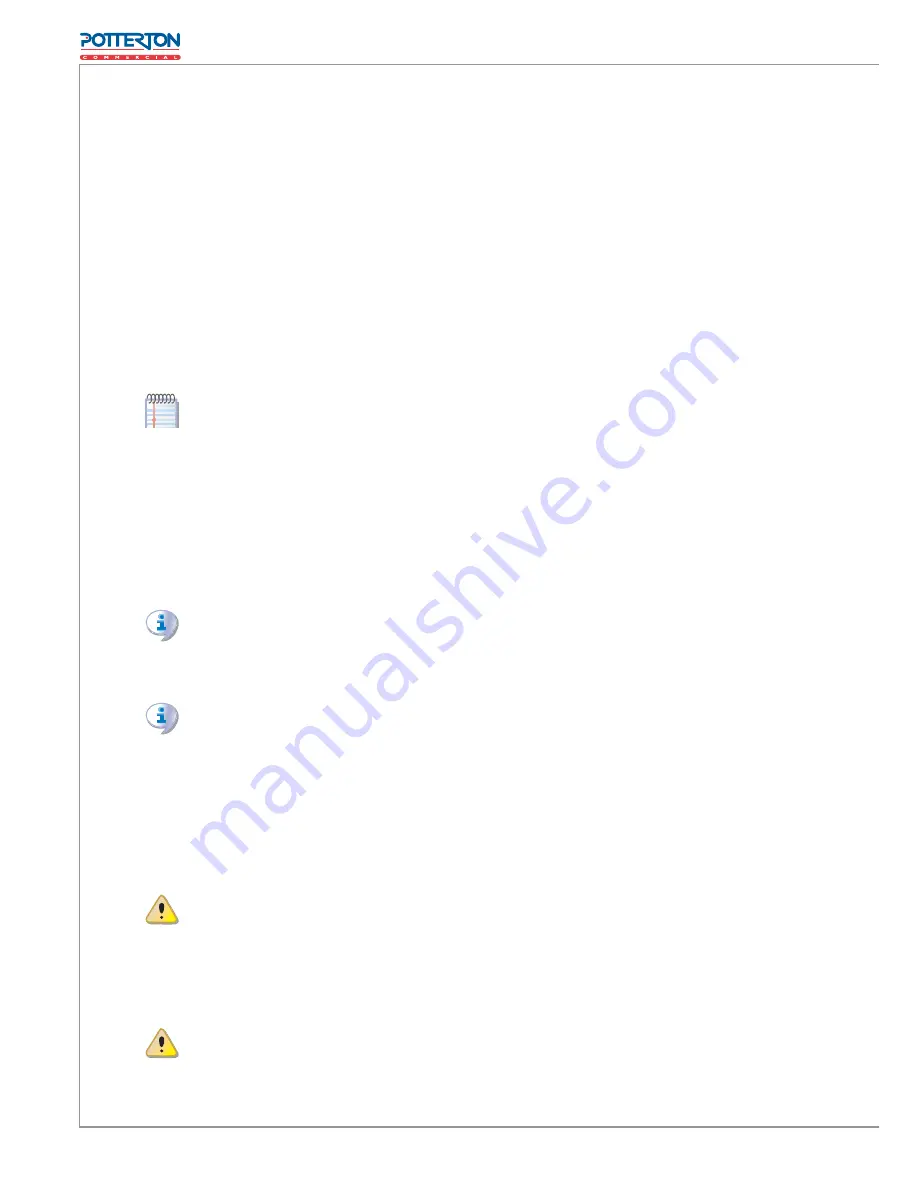
30
The components described below, are those to be always fi tted in proximity to the
appliance:
• ANTIVIBRATION JOINTS in line with the water and gas connections of the appliance.
• MANOMETERS installed in the inlet and outlet water pipes.
• INLET FLOW CALIBRATION VALVE, either of the gate valve or the overcentre valve type,
installed in the water inlet pipe of the appliance (only if the appliance is controller
by a DDC).
• WATER FILTER installed in the appliance water inlet pipe.
• ISOLATION BALL VALVE in the water and gas pipes of the plant.
• 3 BAR SAFETY VALVE installed in the appliance outlet water pipe.
• PLANT EXPANSION TANK installed in the appliance outlet water pipe.
• EXPANSION TANK for individual appliance installed in the appliance water outlet pipe
(primary side). Provide a plant expansion tank in any case (secondary side), installed
in the appliance water outlet pipe.
The appliance is not equipped with an expansion tank: therefore it is necessary to install
a suitable expansion tank, the sizing of this vessel should be calculated by a suitably
qualifi ed heating engineer.
• variable rate WATER CIRCULATION PUMP, FOR PLANT WITH A SINGLE APPLIANCE,
located on the water inlet pipe of the appliance, fl owing towards the appliance.
• variable rate WATER CIRCULATION PUMP, FOR PLANT WITH SEVERAL APPLIANCES
(each appliance should have a pump), fl owing towards the appliance.
• PLANT FILLING SYSTEM: if automatic fi lling systems are used, a seasonal check of the
percentage of monoethylene glycol in the plant is recommended.
The operations necessary for commissioning the appliance must be carried out exclusively
by Potterton Commercial. These operations are described in Section 6 INITIAL ACTIVATION
AND MAINTENANCE on page 57.
The products' warranty is void if commissioning is not carried out by a Potterton
Commercial Engineer.
4.4
GAS SUPPLY SYSTEM
The installation of gas supply pipes must be carried out in compliance with current
regulations in force.
The gas mains pressure must be in the range given in Table 6.1 Network gas pressure on
page 59.
Supplying gas to the appliance at higher pressures than those indicated above can
damage the gas valve.
For LPG systems fi t a fi rst stage pressure reducer of the fl ow necessary near the liquid gas
tank to reduce the pressure to 1.5 bar and a second stage pressure reducer from 1.5 to
0.03 bar near the appliance.
LPG may cause corrosion. The connectors between the pipes must be made of a material
that is resistant to this corrosive action.