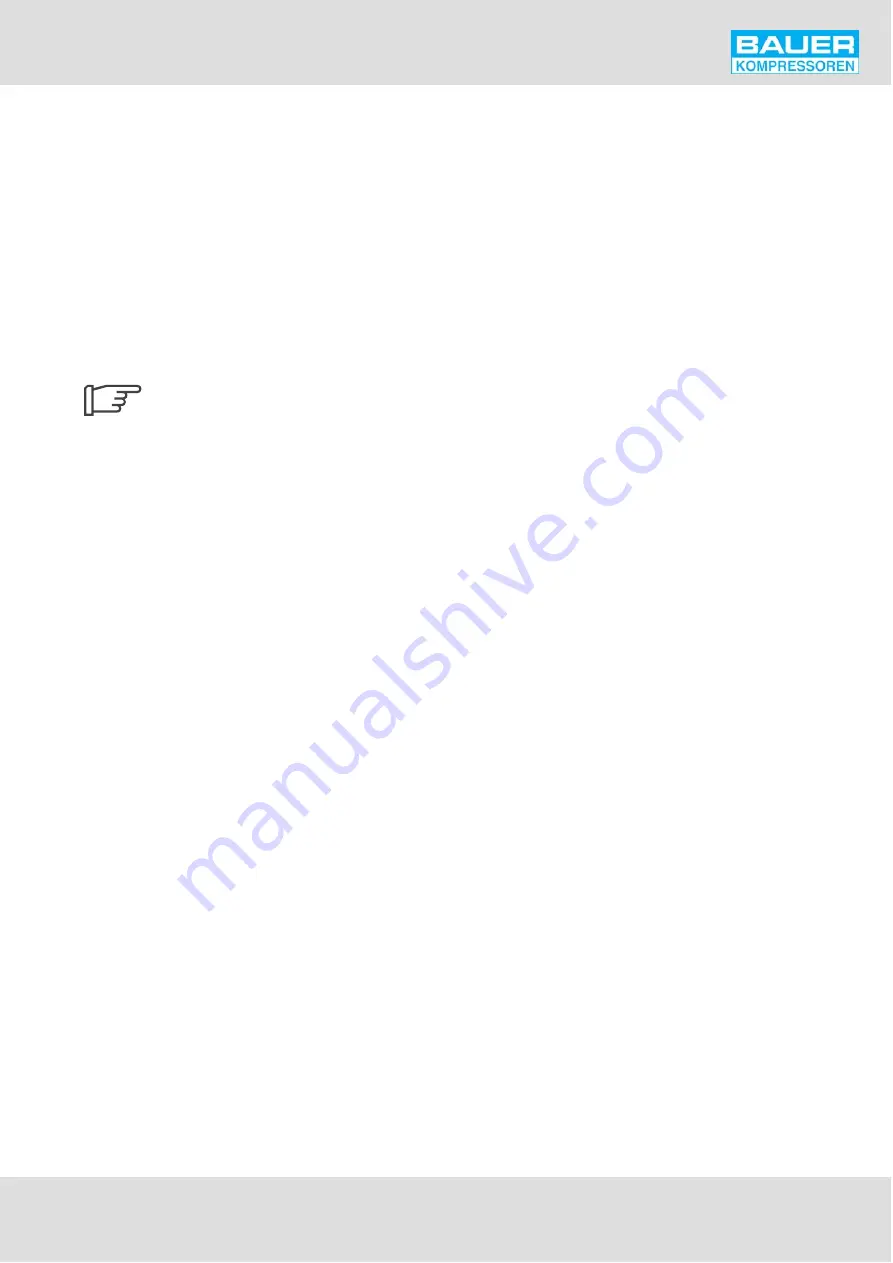
Instruction Manual
w
PE 100-T
29
5.
STORAGE, PRESERVATION
GENERAL
If the compressor is put out of service for more than six
months, the unit should be preserved in accordance with
the following instructions: Make sure the compressor is
kept indoors in a dry, dust free room. Only cover the com
pressor with plastic if it is certain that no condensation will
form under the sheet. Nevertheless, the sheet should be re
moved from time to time and the unit cleaned on the out
side. If this procedure cannot be followed and/or the com
pressor is going to be taken out of service for more than 2
years, please contact our Technical Service Department for
special instructions.
The compressor is not resistant to salt-
water! If not in use keep unit in a dry
place.
PREPARATION
Before preserving the compressor unit, run it warm and
when it reaches the specified service pressure, keep it run
ning for approx. 10 minutes.
Then carry out the following:
-
Check all pipes, filters and valves (also safety valves) for
leakage.
-
Tighten all couplings, as required.
-
After 10 minutes, open the filling valves or the outlet
valve and run the compressor at the set minimum pres
sure (pressure maintaining valve, see chapter 4.4.6.) for
approx. 5 minutes.
-
After these 5 minutes, shut the system down. Drain con
densate from separators. Depressurize unit. Shut filling
valves.
-
Open filters and grease threads.
-
Ensure that filter cartridge remains in the filter!
This will prevent oil entering filling lines as a result of
preservation procedures.
-
Remove intake filter from manifold and all intake lines
from valve heads.
-
Let compressor unit cool down.
PRESERVING THE COMPRESSOR
-
Turn the compressor on and spray a small amount (ap
prox. 10 ccm/0.6 cu. in.) of compressor oil
into the valve
head inlet port while the compressor is running. Do not
let the compressor warm up too much, to keep oil sticky.
-
Shut compressor unit off.
-
Close all valves.
-
Place the dust cap onto the inlet port.
PRESERVING THE MOTOR/ENGINE
Preserve the motor/engine according to the instructions of
the motor/engine manufacturer.
PREVENTIVE MAINTENANCE DURING STORAGE
Run the compressor
once every 6 months
as described in
the following:
-
Remove the dust cap from the inlet port and insert the
intake filter.
-
Open the filling valves or the outlet valve and let the unit
run for approx. 10 minutes or until the pressure gauges
indicate the correct values.
-
Stop the compressor.
-
Open condensate drain valves and release compressed
air. Close condensate drain valves again.
-
Carry out preservation procedure according to chapter
”preserving the compressor”
Changing the lube oil for preserving
-
After prolonged storage, the oil will age in the com
pressor and engine. It should be drained after
2 years
at the latest and replaced with fresh oil.
-
The stated period can only be attained when the crank
case is sealed during the preservation period in accord
ance with the preservation requirements.
-
After changing the oil, turn the compressor and the en
gine or run them for the required period.
-
Check the lubrication of the compressor when putting
the unit into operation once every six months or when
turning the compressor. The oil pump is functioning
properly when oil can be seen flowing through the sight
glass of the oil pressure regulator and if the oil pressure
gauge indicates the prescribed pressure.
REACTIVATING THE COMPRESSOR UNIT
-
Remove the dust cap from the inlet port and insert the
intake filter.
-
Check the oil level of the compressor.
-
Check the motor/engine according to the manufac
turer's instructions.
-
Open the purifier and change all filter cartridges.
-
Run the compressor warm with open filling valves or
outlet valve for approx. 10 minutes.
-
Check the oil pressure on the pressure gauge. If there is
any fault, check the lubrication of the compressor.
-
After 10 minutes, close the filling valves or the outlet
valve and run the unit up to final pressure until the final
pressure safety valve blows.
-
Check the inter-pressure safety valves for leakage.
-
Establish cause of any fault from the trouble-shooting
table, chapter 4.5., and take corrective action.
-
Stop the system when running properly, the compressor
is then ready for operation.
6.
REPAIR INSTRUCTIONS
GENERAL
Preventive maintenance usually involves replacing the
valves, gaskets and sealing rings as well as carrying out the
maintenance work. Repair work can be carried out on the
compressor block to a certain extent but a certain experi
ence and skill is necessary. It should be noted, however,
that
-
no repair should be carried out on the crankdrive nor on
the bearings
Содержание PE 100-T
Страница 1: ...High Pressure Breathing Air Compressors Instruction manual...
Страница 2: ......
Страница 6: ...Instruction Manual w PE 100 T iv NOTES Model Serial No Date of purchase Dealer address phone no...
Страница 39: ...Instruction Manual w PE 100 T 33...
Страница 40: ......
Страница 41: ...Instruction Manual w PE 100 T 35 8 ANNEX Schematic diagram Lubricating oil list Parts list...
Страница 42: ...Instruction Manual w PE 100 T 36...
Страница 44: ...Instruction Manual w PE 100 T 38...