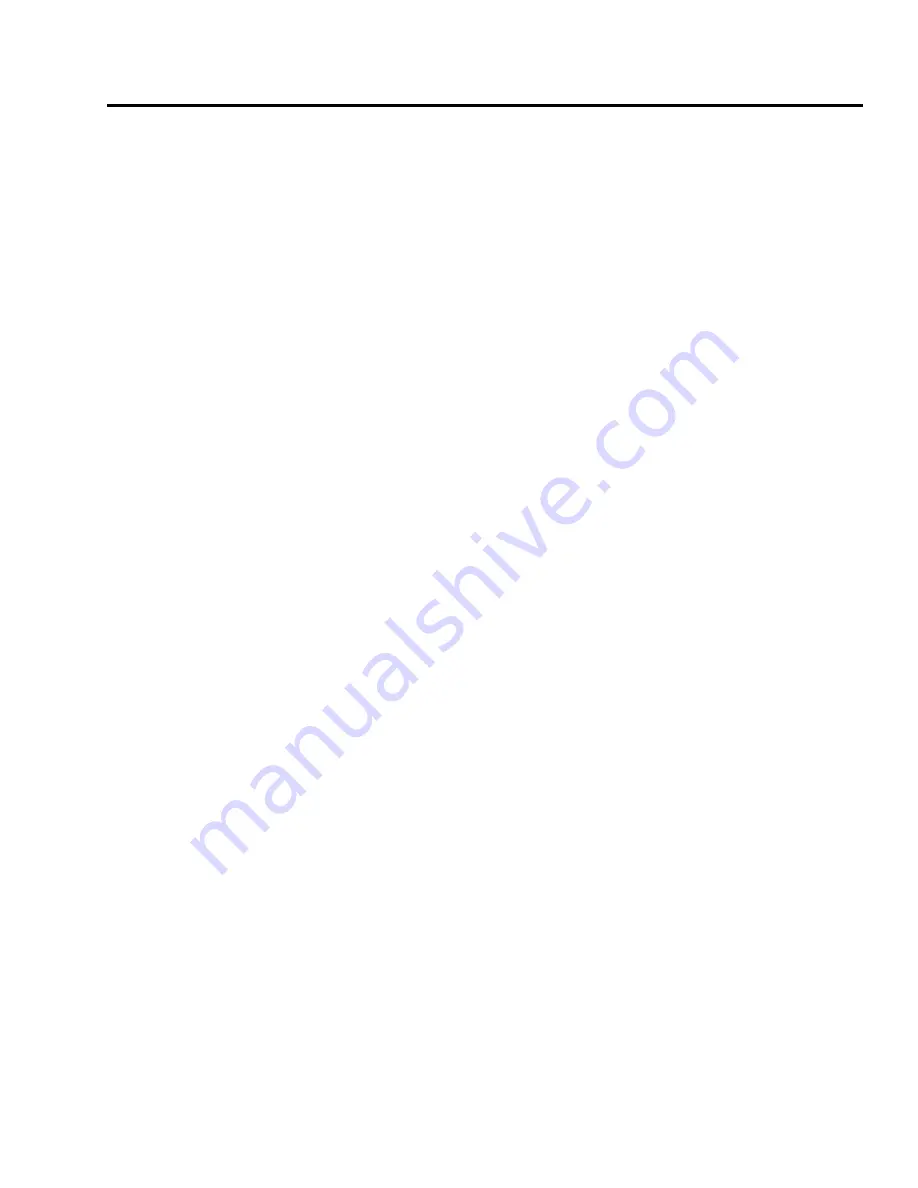
2-79. AREAS PRONE TO CORROSION. Certain areas are more prone to corrosion than others. The following
list is intended to be a general guide to areas where corrosion is frequently found:
a. Areas around steel fasteners are susceptible to corrosion. The paint on these areas cracks which allows
moisture to seep in and corrode the under-lying metal. Each time the fastener is removed, it should be coated
with zinc chromate before reinstallation. The paint should be wet when fasteners are installed.
b. Fluids tend to seep into faying surfaces, seams and joints due to capillary action. The effect of this type of
intrusion is usually detectable by irregularities in the skin's surface.
c. Spot welded assemblies are particularly prone to corrosion. The only means to prevent this type of
corrosion is by keeping potential moisture entry points in the spotweld filled with a sealant or preservative
compound.
d. Areas which are exposed to exhaust gases may have their finish damaged by deposits. These deposits may
result in an aggressive attack on the metal by corrosion. Heat from the exhaust may also blister or otherwise
damage the paint. Gaps, seams, hinges and fairings are some places where exhaust gas deposits may be trapped
and not reached by normal cleaning methods.
e. The wheel well and landing gear are the most exposed parts of the aircraft. Due to the complexity of its
shape, maintaining a protective coverage is difficult. The especially troublesome areas are: magnesium wheels,
around boltheads, lugs and wheel well areas; exposed rigid tubing, B-nuts, ferrules; under clamps and tubing
identification tape; exposed position indicator switches and other electrical equipment; crevices between
stiffeners, ribs and lower skin surfaces.
f. Flaps, flight controls and equipment installed in these areas may corrode unnoticed unless a careful
surveillance is maintained.
g. Engine frontal areas, air inlet ducts and the leading edge of wings, because they are constantly exposed to
abrasion by dirt, dust, gravel and rain, should be checked frequently for the beginning of corrosion.
h. Hinges (piano hinges especially) are extremely vulnerable to corrosion due to the wearing away of their
protective coating and their being a natural trap for dirt, salt and moisture.
i. Control cables may have bare spots in their preservative coating which could lead to corrosion. Cables
having external corrosion should be checked for internal corrosion. If internal corrosion is present, replace the
cable. If only external corrosion is present, remove corrosion with a wire brush and recoat cable with
preservative.
j. Any area where water may be trapped is a trouble spot for corrosion. Drain holes should be checked and
cleaned regularly.
k. Battery compartment and vent openings are particularly prone to corrosion due to spilled electrolyte.
Fumes from overheated battery electrolyte will spread to adjacent areas and cause rapid corrosion of unprotected
surfaces. Frequent cleaning and neutralization of deposits will minimize corrosion from this cause.
l. Due to magnesium parts being prone to corrosion. Special attention should be given to their surface
treatment, proper insulation (due to dissimilar metal corrosion) and paint coatings.
m. Electrical components and connectors should be checked. Their inspection frequency should be based on
their operational environment and past trouble with them.
n. Skin joints and lap-overs are two areas which may contain moisture. Corrosion in these areas may go
unnoticed unless particular attention is paid to them during inspection.
o. Hoses having an internal wire braid which are located in a position where they are frequently water soaked
need a protective treatment.
p. Drilled holes and the trimmed end of sandwich panels should be protected. An inhibitor solution and/or
sealant application is recommended. Any gaps or cavities which allow dirt or moisture to enter should be filled
with a sealant.
PIPER AIRCRAFT
PA-28-161 CADET
AIRPLANE MAINTENANCE MANUAL
Issued: FEBRUARY 28, 1989
HANDLING AND SERV I C I N G
1C14