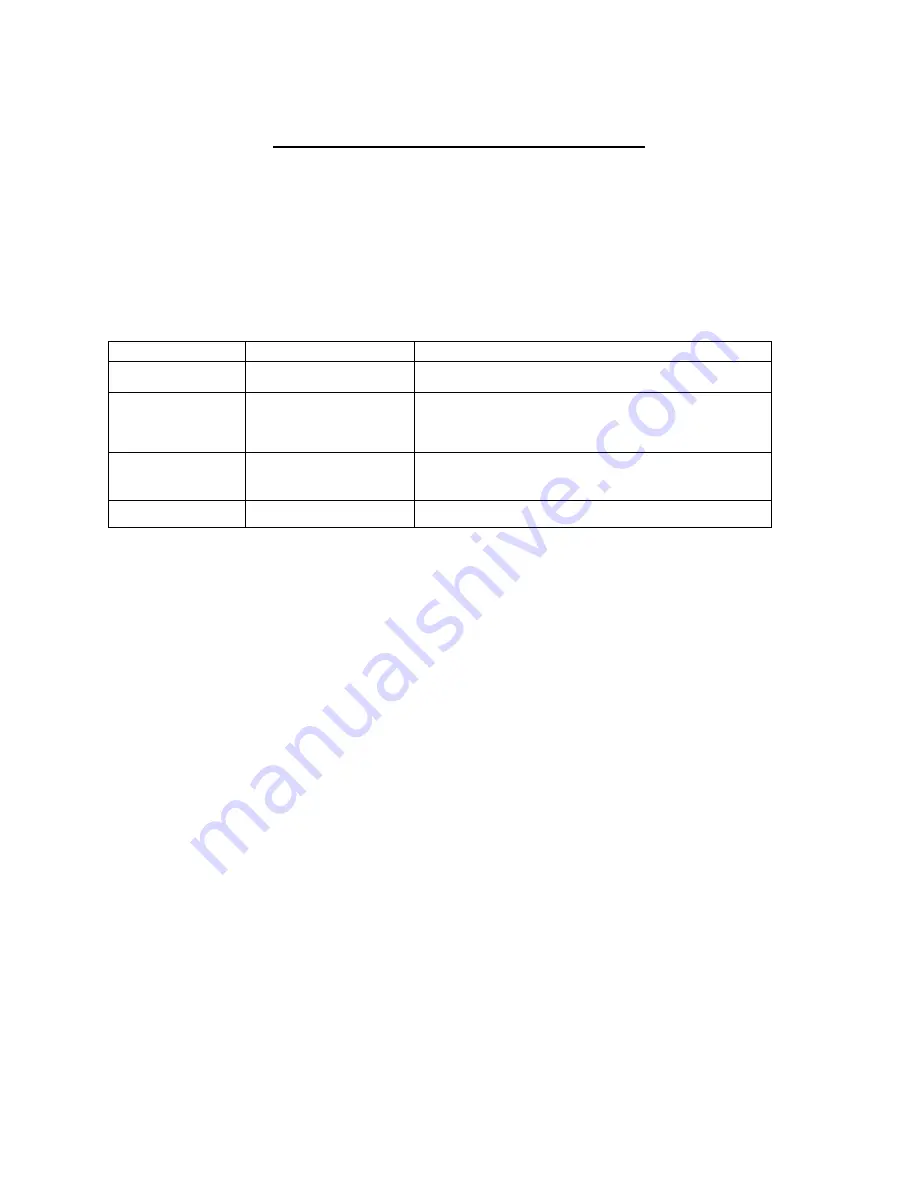
18
Maintenance and Cleaning
The HYPROLYSER
®
Compact Units are manufactured to the highest quality standards and have along service life. However,
some parts are subject to operational wear. This means that regular visual inspections are necessary to ensure a long service
life. Regular maintenance will protect the system from operational interruptions.
Maintenance Intervals
The system requires regular maintenance to prevent errors, poor performance and even failure. This table gives an overview of
maintenance work and the intervals at which you must carry it out. The Operation Manual contains instructions for carrying out
this work.
Interval
Level
Maintenance
On demand
Operator
Replace softener cartridge if fitted
Annual
Technician
Clean water flow restrictor
Check water & brine solenoid valve integrity
Check & Test hydrogen gas sensor
2 yrs. (or >10,000
operating hours)
Technician
Replace pipe gaskets
Check, Test & Replace hydrogen gas sensor
5 yrs.
Technician
Major overhaul
Clean Water Flow Restrictor
The flow restrictor may occasionally be compromised due to sediment fouling carried in via the water supply. One of the reasons
the HYPROLYSER
®
may alarm on “NO WATER FLOW” could be a result of a blockage at the point of the restrictor.
Precondition for action:
Isolate the power supply to the HYPROLYSER
®
via the rotary isolator switch.
Isolate the feed water supply to the HYPROLYSER
®
.
Perform the following working steps:
1.
Remove the HYPROLYSER
®
front outer red plastic protective mechanical cover by removing the black protective nut cap.
Unscrew the single retaining nut and remove the red cover.
2.
Push back the tube fitting collar with finger and thumb and pull out the red restrictor from the assembly. Check the internal
orifice is clean and free of debris.
3.
Replace the restrictor in reverse operation to above ensuring that the restrictor fully engages into the tube fittings to make a
water tight seal.
4.
Refit the red mechanical cover.
5.
Start-up the system.
The restrictor has been successfully checked.