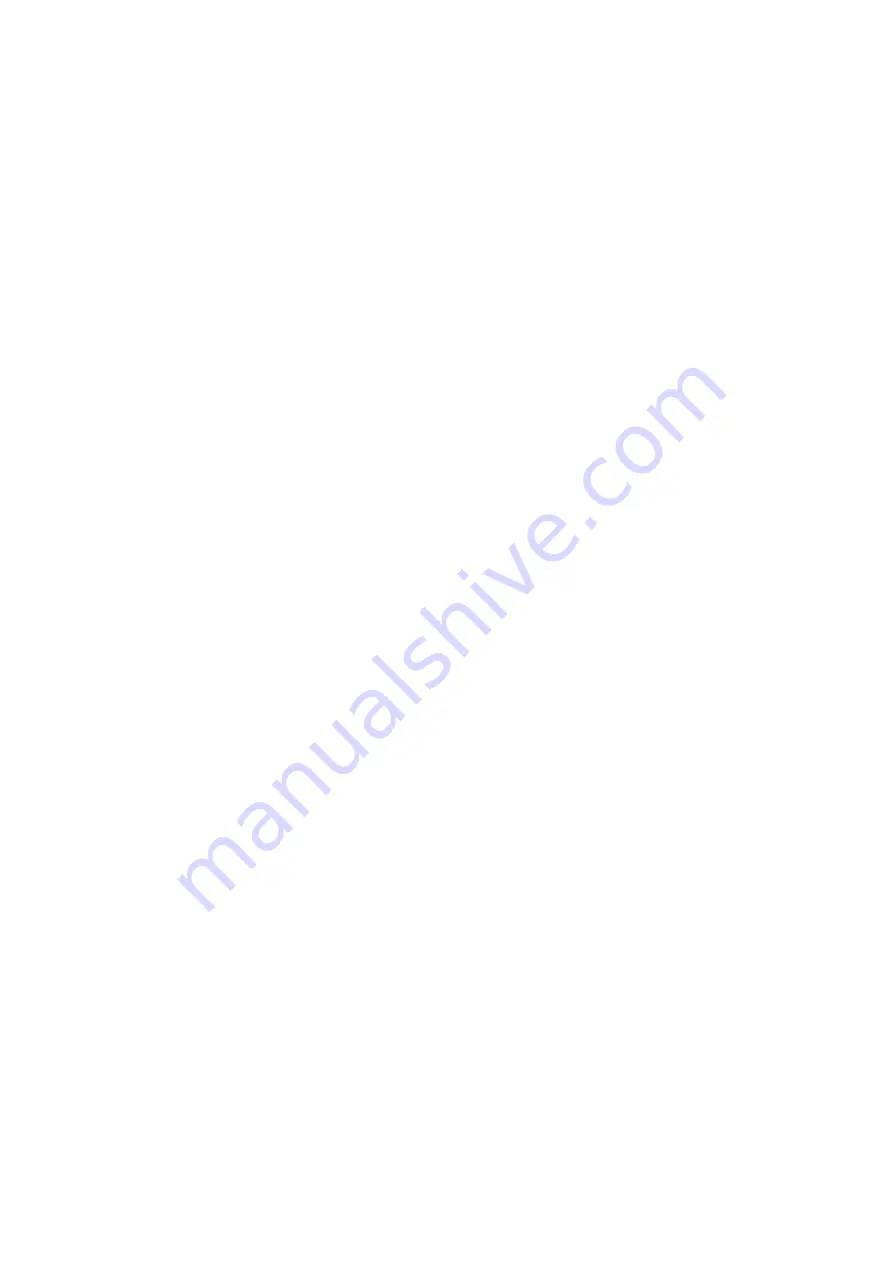
Safety at Work
If all the elements are appropriately designed, hydraulic circuits are reliable and safe even at great pressures. However, a breakdown
due to material defect or fatigue can occur in them, which could endanger the safety of the staff or contaminate the environment with
oil. Examples of defects manifesting themselves outwardly:
• oil dripping,
• destruction of pressure-loaded circuit parts.
Oil dripping from an untight connection or another spot, which collects on the floor, can cause slipping and falling of persons or floor
damage and penetrating in the environment, it can cause extensive pollution of large quantities of water. The destruction of pressure-
loaded circuit parts does not cause any explosion. If the crack is small, oil is dispersed to the environment in form of mist, if the crack
is large, mostly the whole tank will be discharged. The destruction of pressure hoses will manifest itself by oil leaking, but very
frequently also by bursting of hose socket. In such an instant, the hose can spring up and cause a serious injury. Both failures cause
pollution of the environment and a small spark can be the cause of a huge fire.
It follows that the following principles must be taken into account for designing, installing and operating hydraulic circuits:
•
do not use hydraulic elements for pressures lower than the circuit working pressure,
•
keep the machine clean, sprinkle the poured out oil with wood chips or VAPEX absorbate, sweep the floor, clean it with an
appropriate solvent and dry,
•
while dismantling, prevent oil spilling by installing suitable containers,
•
units and all hydraulic elements including hoses and pipelines must be protected against external mechanical damage and heat
resources,
•
if the circuit is under pressure, do not come close to the pipelines and hoses, particularly do not expose your face,
•
should oil be spilled into eyes, flush eyes with Ophtal or any other suitable agent immediately,
•
should a nonflammable liquid be spilled into the eyes (except for water emulsion), consult an ophthalmologist.
•
do not smoke or use open fire in the store and near the units and hydromotors,
•
shut down the hydrogenerator drive whenever you make any changes or repairs,
•
electrical equipment must comply with the ESC regulations,
•
containers with industrial petrol may only be used in reserved spaces and must be covered with a cover or a closure at all times,
•
hydromotors, which could start turning automatically in case that the driving hydrogenerator switches off (pressure drop), must be
mechanically or hydraulically locked against this possibility,
•
all hydraulic systems and circuits must be protected by a pressure valve against overloading, as well as hydromotors, which could
become overloaded after hydraulic locking,
• a person responsible for maintenance and setting of the hydraulic unit must be appointed.
The above-mentioned safety at work principles are not complete.
There are different conditions for each hydraulic circuit and different possibilities of endangering the environment. These principles,
however, should reduce the accident rate and improve the working conditions of users.
Hydraulic Liquids
The correct function, life, operational reliability and economy of the hydraulic equipment are substantially influenced by the usage of
suitable hydraulic liquids. Mineral oils, also called hydraulic oils, are the most frequently used liquids.
Hydraulic liquids fulfill
various tasks in the hydraulic equipment. The most important of them are the following:
• hydraulic energy transfer from hydrogenerator to hydromotor • lubrication of moving parts of hydraulic elements • rust protection •
discharge of impurities • water drain • air vent, etc. • removal of loss heat developed by volume losses and friction.
The hydraulic liquid quality is characterized by the following parameters:
Kinematic viscosity
is defined as resistance against flowing through lines and clearances. Higher viscosity means a thicker liquid.
2
-1
2
-1
The viscosity unit is m .s (mm .s is used in practice). Viscosity is dependent on temperature. The amount of temperature influence,
i.e. the change of viscosity with temperature, is determined by the viscosity index. The bigger the viscosity index, the smaller the
dependence of viscosity on temperature (in standard mineral oils between 85 and 90, in better quality oils 100 and higher). Viscosity
is also influenced by pressure. Viscosity increases with the pressure increase.
The compressibility
affects the rigidity of the system and thus also the precision of motion in high-pressure devices. The
compression value is relatively small. The compressibility of liquid increases with the content of air or other gases.
Foaming quality
is undesirable with regard to the function of liquid but also with regard to its ageing. Chemical additives reduce the
foaming quality. The foaming quality can be very substantially affected by the hydraulic system design (tank design, air infiltration).
Requirements for Liquid Properties
The main requirements can be put as follows:
• small dependence of viscosity on temperature change • corresponding viscosity guaranteeing good efficiency of system • good
lubricating capacity and high mechanical oil film stability • chemical stability and neutrality against materials used • operational
stability (liquid resistance against ageing) • low foaming quality • availability and reasonable price.
Specification of Hydraulic Liquids According to ISO 6743/4
HM and HV oil performance classes are particularly suitable for using in hydraulic circuits.
HM
- high-quality oils containing additives against oxidation, corrosion, foaming, for reducing wear and tear and viscosity modifier
improving also low-temperature properties. They are intended for hydrostatical mechanisms with high mechanical heat stress and
for machines operated in unprotected environment throughout the year.
Содержание ARG 250 plus S.A.F.
Страница 34: ...11 3 2 Table turning table pivot and vice assembly ARG 250 plus S A F ARG 300 plus S A F...
Страница 44: ......
Страница 45: ......
Страница 47: ......