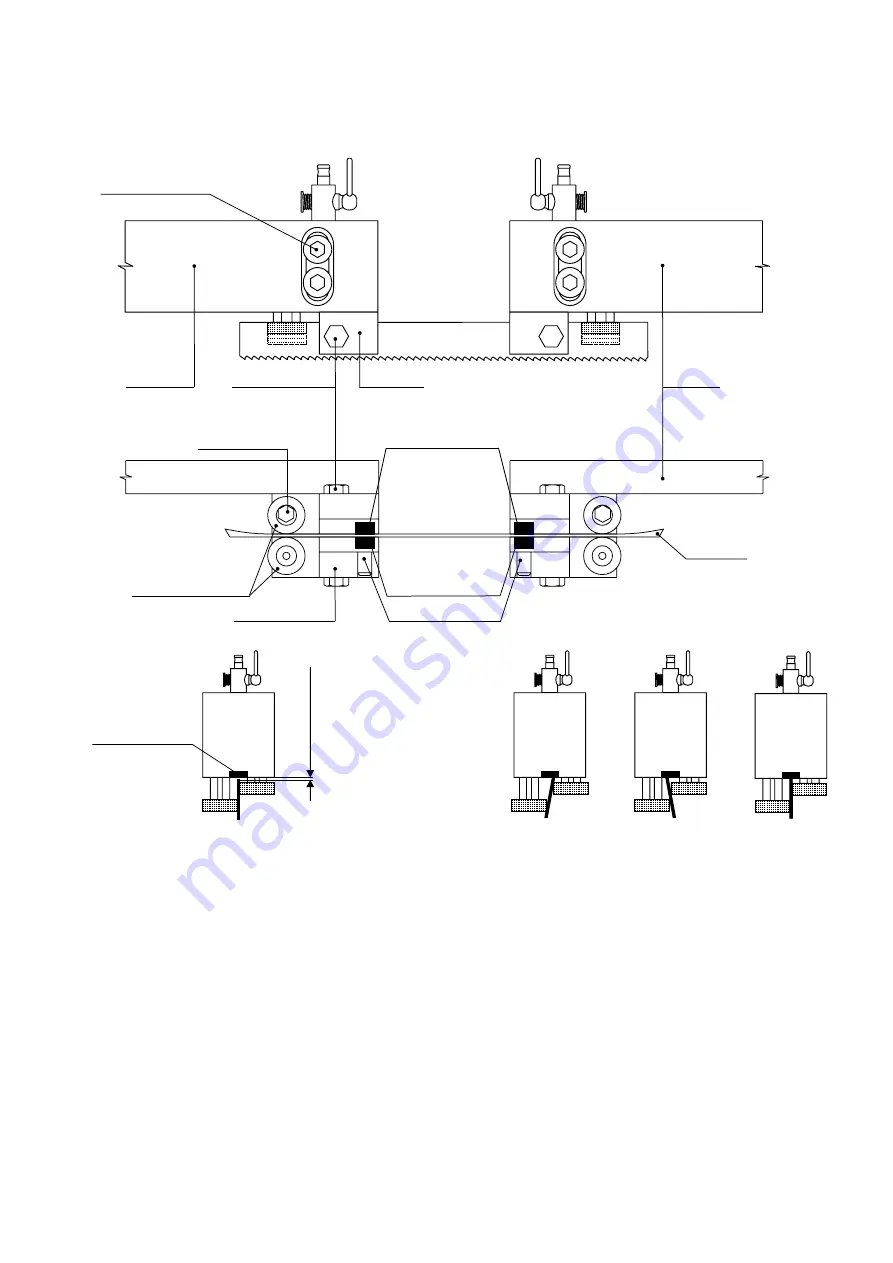
EXCENTR SCREW
HARDMETAL GUIDANCE
WITH SETTING SCREW
EXCENTRIC BEARINGS
HARDMETAL SCREW
HARDMETAL SCREW
PRESSING HARDMETAL
GUIDANCE
FIXED HARDMETAL
GUIDANCE
ADJUSTABLE
GUIDE BAR
FIXED BAR
GUIDE HEAD
GUIDING HEAD SCREW
SAW BAND
5.4. Guide heads - adjustment
The correct adjustment of the bearings and hard-metal guides principally influences the band life and the quality of the cut. The
eccentrically arranged bearings of the guide heads must be so set that the band surface is parallel to the surface of the hard-metal
plates and that there is minimum clearance between these plates and the band.
Guide Head Setting
Close hydraulic damper valve (see Chapter 5.9.) and elevate the saw blade approx. 20 mm above the fixed gripping jaw of the vice
(see chapter 7.2.). Switch off the master switch, isolate the machine from supply and secure it against restarting. Adjust the moving
guide head so that the guide heads are approx. 20 cm from each other. Disconnect the supply hoses of the coolant valves. Unscrew
the guide heads gradually from the fixed and moving guide bars, turn them through 180° (bearing and carbide guide upward) and
screw to the bars again. Observe the perpendicularity of the guide heads to the bars and the identical height of the guide heads.
Check the tightening of the fixed carbide guides. Insert approx. 30 cm of an old saw blade in the guide heads between the carbide
guide and the bearings. Set the pressure carbide guides with the width setting screw of the carbide guides so that the saw blade
moves without clearance between the carbide guides, but does not seize. When the saw blade is correctly set, adjust the
eccentrically arranged bearings to prevent the bearings from "cutting" the saw blade but there must not be big clearance between the
bearings. When the saw blade moves, the bearings are carried along by the saw blade. Check all the bolt connections for tightening.
Unscrew the guide heads from the bars. Fit the saw blade on the moving wheels, checks its correct alignment on the moving wheels
and tension the saw blade. Install both guide heads on the saw blade in the space between the bars and adjust their correct position
on the bars. Than we move guiding heads up, so that the space between fixed carbide guides and upper part of saw band was
approx. 0,5-1mm. In this way, the correct guide head height towards the bars is set. Adjust the guide heads perpendicularly to the
bars and tighten them. Close the rear head protective enclosure, switch on the master switch or connect the machine to the network.
Carry out a short test run of the saw blade. Switch off the master switch, isolate the machine from supply, open the rear head
protective enclosure and check the saw blade fitting on the moving wheels and in guiding heads. Make corrections, if required (see
Chapter 5.4.). For casual checking of blade position can be used CONTROL HOLE OF BAND GUIDANCE. Close the rear head
protective enclosure, connect the machine to supply, switch on the master switch and hydraulic unit. Carry out the first cut.
Incorrect band guidance
Correct band guidance
between bearings into middle
approx. 0,5-1 mm
FIXED HARDMETAL
GUIDANCE
Содержание ARG 250 plus S.A.F.
Страница 34: ...11 3 2 Table turning table pivot and vice assembly ARG 250 plus S A F ARG 300 plus S A F...
Страница 44: ......
Страница 45: ......
Страница 47: ......