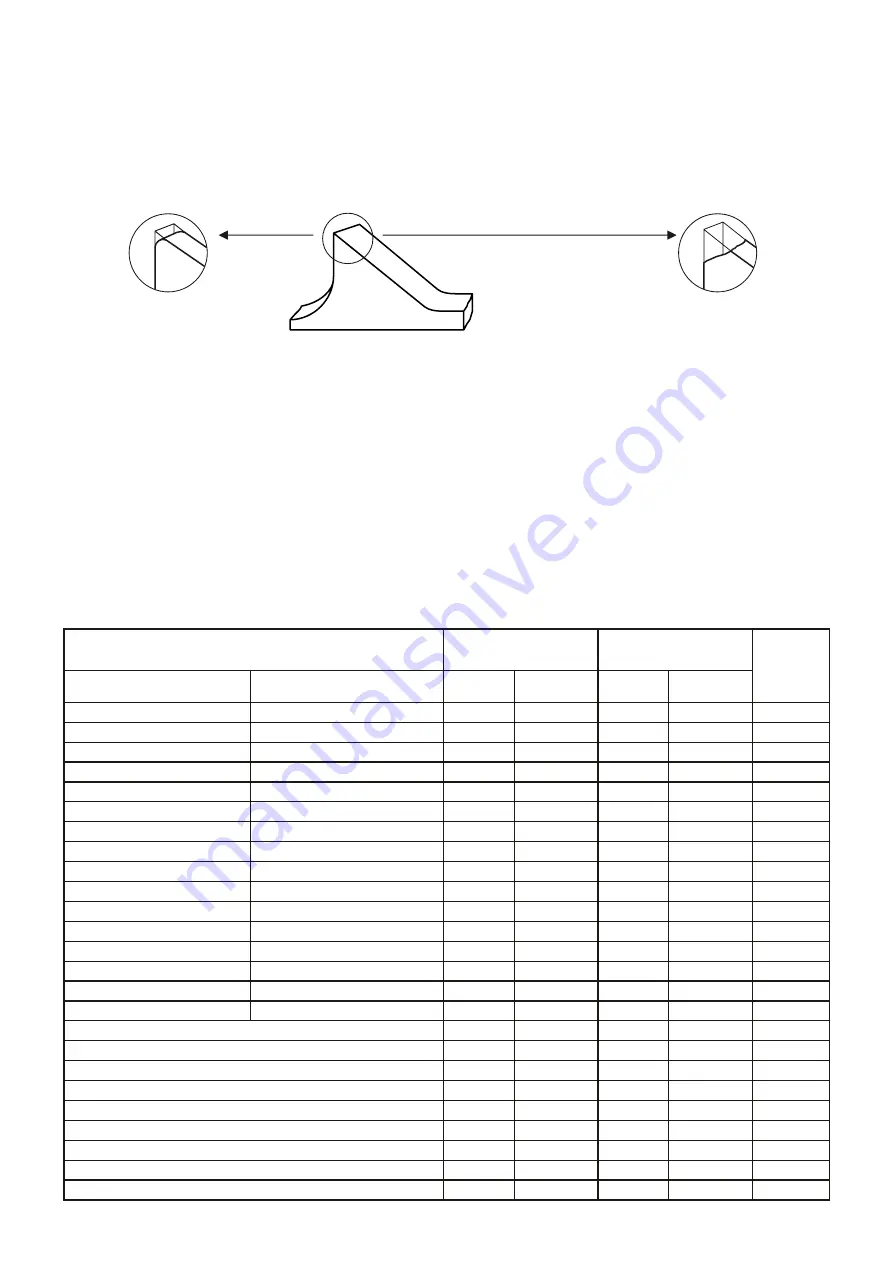
8.5. Factors Influencing Saw Blade Service Life
Inappropriate saw blade tooth size • inappropriate saw blade speed and saw blade descent speed to the cutting position • the saw
blade (the whole band saw arm) leans against the workpiece when the band saw is not in the cutting position • the workpiece is not
clamped as recommended • saw blade tension is not correct (mostly too little tension) • the saw blade is not correctly fitted on the
guide wheels (the saw blade touches the wheel shoulder) • the saw blade guide heads are not correctly adjusted • the distance
between the saw blade guide heads and the workpiece is too big • the oil content of the coolant is too low • the saw blade is not
correctly run in • saw blade maintenance is insufficient, metal chips have not been removed from the band saw.
The above mentioned faults lead to inaccurate cut, reduction of the saw blade service life and/or its destruction.
8.6. Values Recommended for Cutting
The selection of values depends on the material class and the material section. The data in the table are only illustrative; they have to
be adjusted to the material for certain ranges. The numbers of the CSN-Standards serve for information only. They define only the
guide for the material properties for which the respective saw blade type is designed.
8
.
4
.
Running-in New Saw Blades
The running-in applies to new saw blades. The sharp cutting edges with extremely small edge radii enable high cutting power. In
order to achieve maximum tool service life, you have to run in (optimum) the new saw blade. Given the correct cutting speed, the
workpiece feed and the quality of its material, the saw blade must be run in only with 50% of currently used feed. Such measure will
help you prevent breaking extremely sharp edges particularly in big workpiece sections. These micro-fragments cause destruction of
other teeth. Should vibrations or noise due to oscillations manifest themselves when a new saw blade has been fitted, reduce the
cutting speed slightly. In small workpiece sections it is recommended to run in the saw blade with a reduced power for 15 minutes, in
big sections for 30 minutes. Then increase the feed slowly to the optimum value.
Correctly run-in cutting edge
Micro-chips in high starting feed
Observe the saw blade running-in at all times!
11 107 - 11 110
11 500 - 11 600 / 12 020 - 12 060
13 250 / 14 260 / 15 260
14 100 / 15 220
14 220 / 15 124
17 020 - 17 042
17 115
17 253 - 17 255
19 150 / 19 192 - 19 312
19 422 / 19 452 / 19 721 / 19 740
19 436
19 662
19 721
19 802 - 19 860
INCONEL, HASELLOY, NIMONIC, INCOLOY
Heat-treated steel
Cast steel
Grey cast iron
Copper, bronze, tin bronze
Red bronze
Aluminium bronze
Aluminium alloy castings
Al 99%, thermoplastics, plastics
11 301 - 11 420 / 12 010 - 12 020
19 063 - 19 083 / 15 142 / 16 142
ČSN
Material
Cooling
oil
volume
(%)
10-15
10
10-15
5-10
3
10-15
10-15
5-10
15
5-10
5-10
3
do not
15-20
5
3
15-20
5
40
25
3
10
10-15
do not
do not
Arm descent speed
into the cut
(mm/min)
ø 100-330 mm
55-20
30-20
35-25
28-15
28-15
55-30
12-4
18-2
6-1
30-25
20-8
21-10
14-5
4-2
16-6
21-10
4-2
23-12
55-25
140-55
85-55
70-45
70-45
55-30
140-55
ø 0-100 mm
190-60
125-35
125-38
125-30
125-30
190-60
75-15
100-20
40-7
125-35
120-25
90-23
62-15
25-5
70-1
90-23
25-5
76-25
190-60
450-150
300-90
230-75
230-75
190-60
450-150
Recommended blade speed
(m/min)
ø 100-330 mm
70-90
40-70
50-70
40-60
30-60
60-80
30-40
30-50
30
40-70
30-60
30-50
30-40
30
30
30-50
30
30-40
30-60
80-90
60-90
60-90
30-60
30-70
50-80
ø 0-100 mm
70-90
50-80
60-90
50-70
50-70
60-90
40-50
40-50
30-40
60-90
50-70
40-60
30-40
30
30-40
40-60
30
40-50
30-70
80-90
70-90
70-90
40-70
40-80
50-90
In general
Free-cutting steel
Structure/construction steel
Cementing steel
Spring steel
Bearing steel
Alloy steel
NIRO steel
Valve steel
Heat-resistant steel
Refining steel
Non-alloy tool steel
Alloy steel
Hammer steel
Nitriding steel
Tool steel for hot processing
High speed steel
Содержание ARG 105 mobil
Страница 2: ......