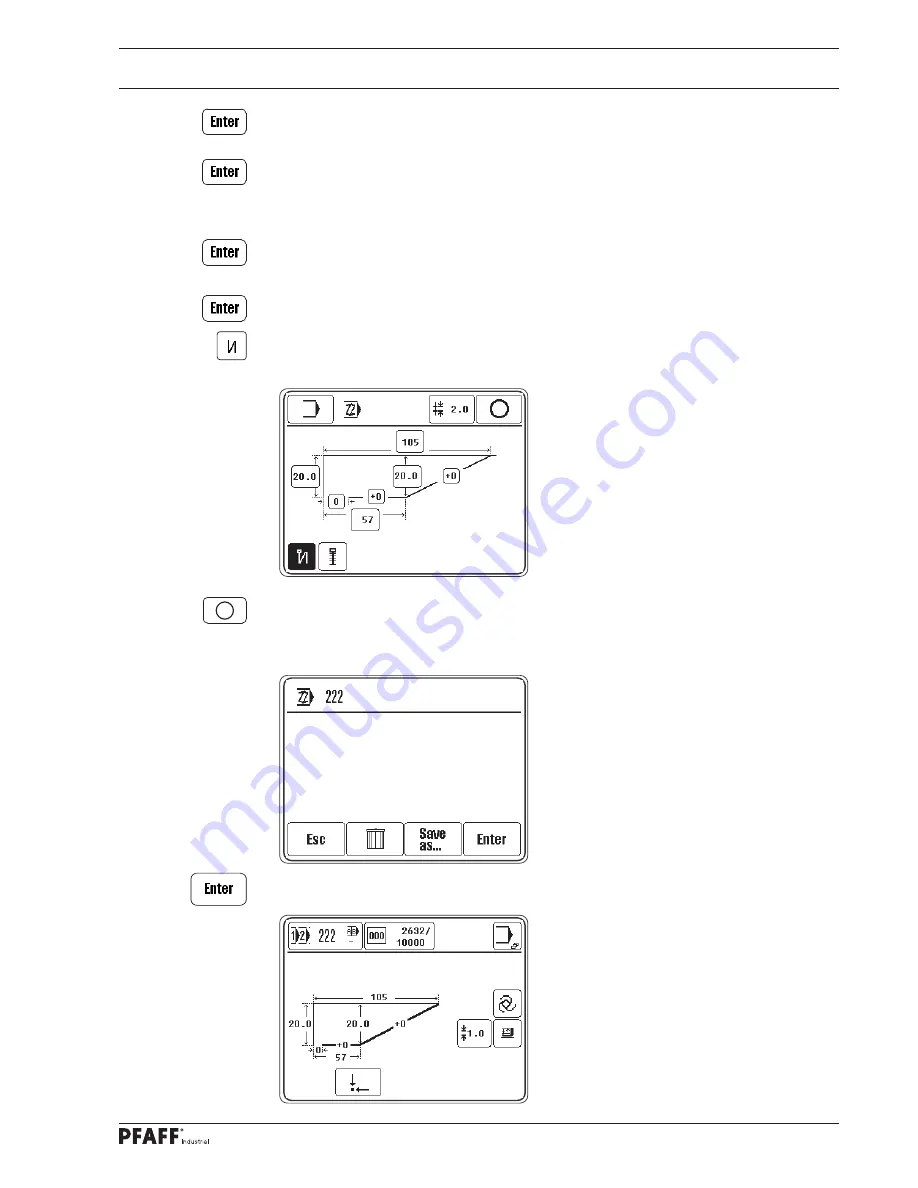
Input
65
Confi rm the input.
Call up function
2
and enter value "20" for the dart depth on the number block.
Confi rm the input.
The values for the curvature (functions
4
and
5)
remain unchanged.
Call up function
3
and enter value "20" for the waist depth on the number block.
Confi rm the input.
Call up function
7
and enter value "57" for the waist length on the number block.
Confi rm the input.
Activate the start backtack.
Conclude the seam program input.
The values are checked and the seam construction diagram is calculated. If errors are
detected, these are displayed with a corresponding message.
Save the seam program.
Содержание 3586-22/02
Страница 42: ...Set up 42...
Страница 157: ...Notizen...