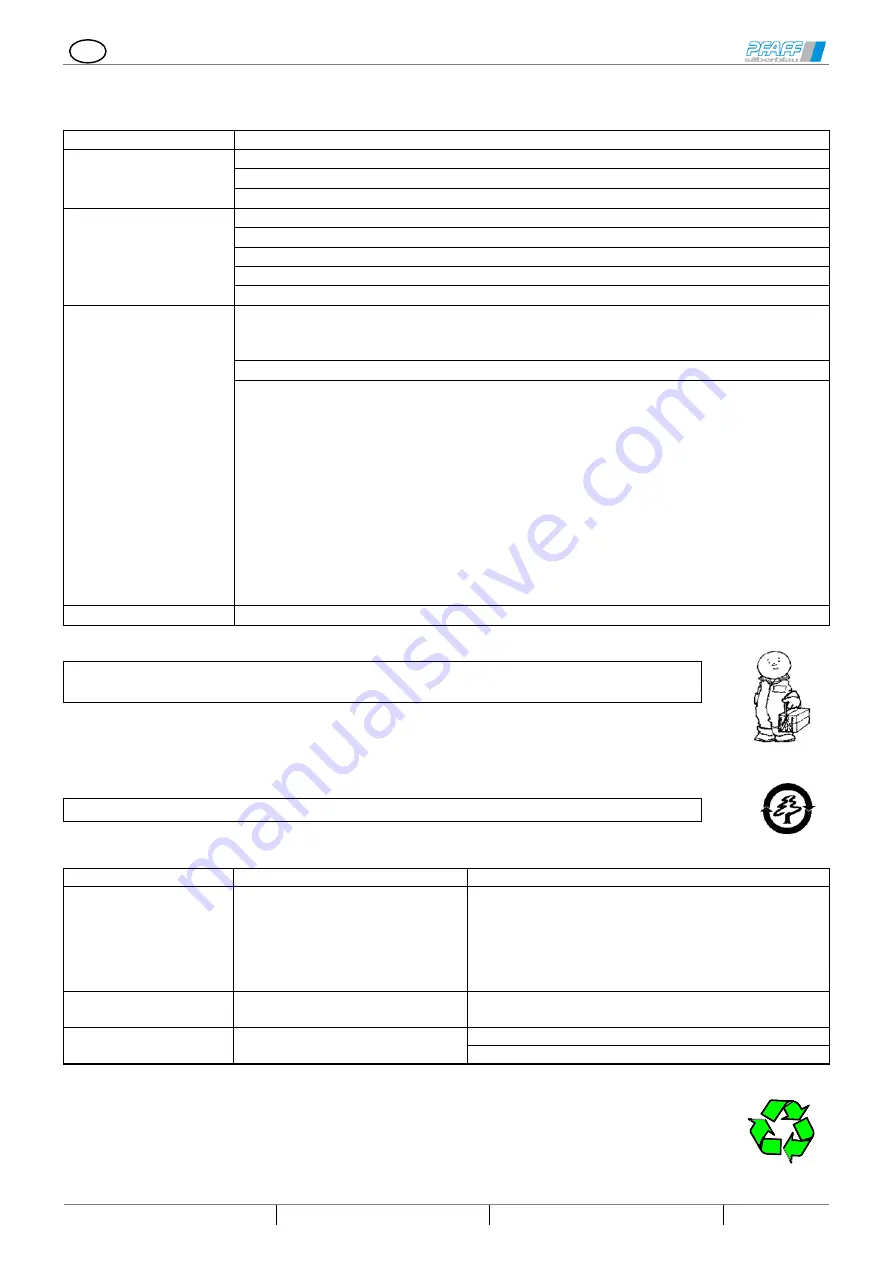
English
Wire rope winch >LAMBDA< BGV C1 for stages and studios
04.04.014
technische Änderungen vorbehalten
design changes under reserve
changements techniques sous réserve
10 / 10
Inspection- and Maintenance Instructions
Before carrying out inspection and maintenance works, unload the winch appropriately.
Inspection Intervals
Maintenance- Inspection Works
daily
resp.
before each use
Visual examination of rope-hook (carrying device).
Function of the winch.
Function of brake
quarterly
Lubricate drive pinion
Grease gearing
Check the safety spring crank -ratchet for brake function and wear.
Examine the rope for wear acc. to DIN15020 page 2 and execute maintenance works.
Check the fixing screws for firm seat.
annually
Arrange for an examination by a competent person.
1)
Check all parts of the winch and crank for wear. If necessary, replace defect parts and
grease them. Only use the grease recommended by us.
Check name plate for legibility
Brake test (acc. to DIN 56950-1:2012-05)
No-load torque (without load) of double safety spring loaded brake with torque
measuring device test.
No-load torque minimum
3 Nm
resp. manual hands force
12 N
with
250 mm
crank arm
length.
With a low deviation from
Mmin
results in an erosion border of the brake spring and
brake drum, the braking mechanism must be exchanged.
When the nominal crank pressure is exceeded in the torque in any direction, the brake
will break.
Nominal manual crank pressure with full load
180 N
with crank arm length from
250 mm
Nominal operation torque
45 Nm
Re-lubrication of the double safety spring crank and double safety spring locking device
only by authorised personnel
1)
.
every 4 years
A competent person should examine the entire installation.
1)
for example by Pfaff-silberblau service department.
The working life of the winch is limited, wearing parts have to be replaced in
good time.
Operating material / Recommended lubricant
Recommended lubricant
for all grease lubricating points: multipurpose grease according to
DIN 51825 T1 K 2 K
for all oil lubricating points: machine or gear oil
CLP - DIN 51517 T3 ISO VG 100
Waste lubricant has to be disposed acc. to legal regulations!
Operating failures and their causes
Failure
Cause
Elimination
In unloaded state, it is
difficult to turn the
crank.
Lubricant in bearing points and
gearing is missing.
Dirt or something similar has ac-
cumulated in the gearing.
Winch was distorted during
mounting
Execute maintenance works.
Check the fixing.
Is the mounting surface even, are the screws tight-
ened correctly?
Load is not held.
Brake is worn out or defect.
Examine brake parts (see examination) and replace
worn out parts (safety spring crank).
Crank force excessive
(like closed brake)
One brake spring is broken
Replace double safety spring crank.
Arrange for an examination by a competent person
Disposal
After having placed out of service, the parts of the hand winch have to be recycled
or disposed according to legal regulations!