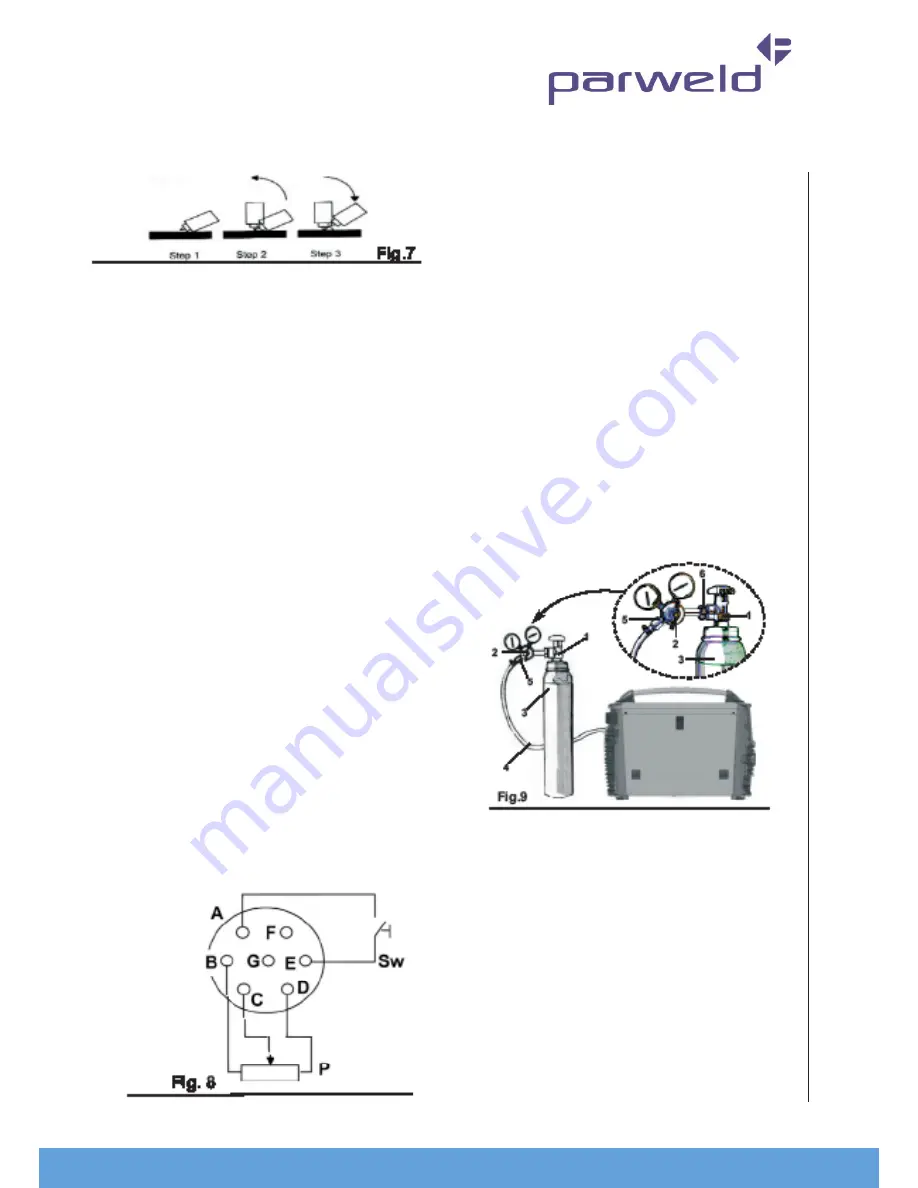
www.parweld.com
At this stage, ignite the arc by moving the electrode
away from the workpiece a few millimetres (step 3
of fig.7). Weld maintaining the same distance from
the weld pool, whilst keeping the torch trigger held
down. Release the button to interrupt the welding
process.
16.POWER CONNECTOR
Before connecting the
machine check the tension, number of phases and
the power supply frequency. The admissible power
supply is indicated in the ‘Specific Techniques’
section on page 5 of this manual and on the
information plate on the machine. Check that the
earth of the welder has been connected correctly.
Furthermore, make sure that the plug provided
with the equipment is compatible with the local grid
sockets. Make sure that the power supply provides
sufficient power for the machine to function (tension
ranges) The power supply grid protection devices
to be used are listed in the ‘Specific techniques’
section of the present manual.
The machine is provided with a specific power cable
that does not usually require an extension lead; in
the event an extension lead is required, use one of
the same capacity [Length/Cross section] or higher
than the machine in use, according to the length of
the cable. A 2.5 mm² three-pole cable + earth, of the
same size or larger.
17. REMOTE CONNECTION
Figure 8 shows the connections of the remote
connector (20 of fig 1).
Where: Sw is the torch trigger
P is the potentiometer for controlling the current.
17.1 REMOTE CONTROL OF THE WELDING
CURRENT
With remote connector 20 in Fig. 1, it is possible to
adjust the current near to the point where the welding
is being carried out. To do so, it is necessary to create
a connection with potentiometer P, shown in figure 8.
The value of the potentiometer is not a critical factor:
between 2.2kOhm and 10kOhm 1/2W can be used.
Turn the potentiometer and select the welding current
in a range between zero and the set value.
18. CONNECTING THE OUTPUTS
Connection of
the welding cables occurs via a Dinse quick-connect
system with appropriate connectors
19. CONNECTING THE GAS CYLINDER AND THE
GAS REGULATOR
For TIG and MIG welding only. For MMA welding, skip
this paragraph entirely.
1. Connect the pressure regulator (2) to the cylinder
(3). Make sure the regulator is suitable for the cylinder
pressure. Attach the connector nut (6) of the regulator
(2) to the cylinder (3). (Do not screw too tightly;
excessive force could damage the valve (1) of the
cylinder (3).)
2. Connect the gas tube (4) to the regulator (2) and
secure with a cable tie (5).
3. Make sure that the gas tube is connected to the
welder correctly.
4. Open the valve (1) of the cylinder (3). Press the
torch trigger and check the gas is flowing correctly. To
carry out this operation release the clutch of the motor.
20
Содержание DP323C
Страница 1: ...ISSUE 2 User Manual DP323C...
Страница 3: ...CONTENTS 2...
Страница 4: ...www parweld com 3...
Страница 5: ...www parweld com 4...
Страница 6: ...www parweld com 5...
Страница 9: ...www parweld com 8 3 LOADING THE WELDING WIRE To load the welding wire follow these instructions...
Страница 24: ...www parweld com 23...
Страница 26: ...www parweld com 25...
Страница 27: ...www parweld com 26 Spare Parts 26...