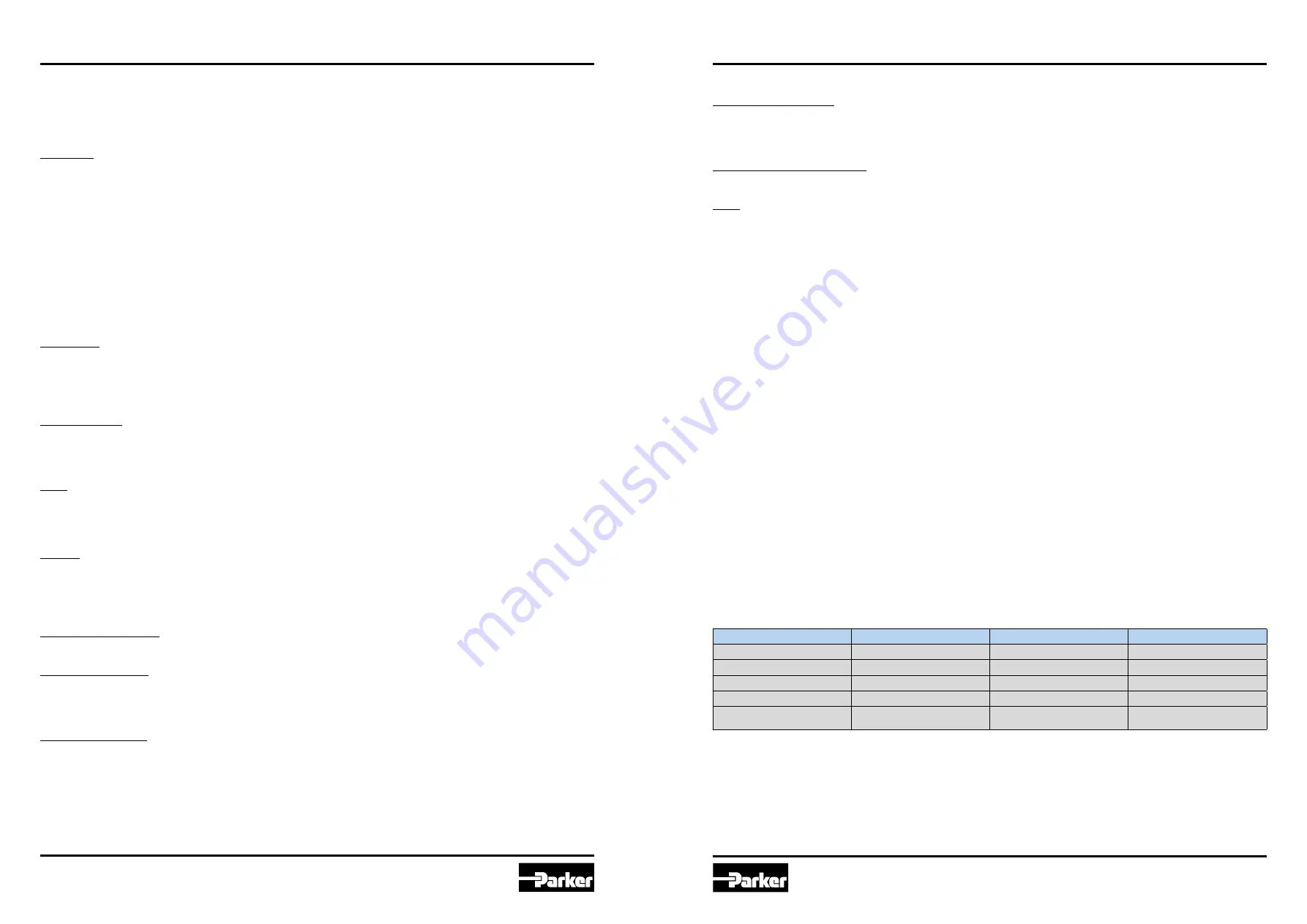
PAC120 5715-719UK.indd 05.06.20
PAC120 5715-719UK.indd 05.06.20
25
24
Parker Automation Controller
Series PAC120
Parker Automation Controller
Series PAC120
5.3.2 Menü – Configuration
5.3.2.1 Menu Item “Network”
Use this page to change various of the control unit's network settings. The new network settings will be enabled
when you restart the unit.
Host name
The host name identifies the control unit in a unique manner. In CODESYS V3, the host name is called device name
and computer name in Windows. Host names are made up of one or several labels separated by a dot. A label
consists of one or more characters.
A label may be comprised of up to 24 ASCII characters:
• a–z or A–Z (no distinction is made between upper and lower case)
• Numerals 0–9
• Hyphen/minus sign –
RFC952 disallows all other characters because they may cause problems. You may also use a Fully Qualified Do-
main Name (FQDN) such as plc24.mycompany.de as the host name.
Please note that the control unit does not run any DNS or WINS services. Accessing the control unit using the host
name therefore requires an extra configuration (e.g. an entry in the network's DNS server).
DNS server
Specify at least one valid DNS server if you wish the control unit to gain access to the domain name system (DNS),
that is to say, if you wish it to access other hosts by their name instead of their IP address. The second DNS serv-
er is a fallback name in case access to the first server fails. Retain the default for both entries (0.0.0.0) if you do
not wish to use the DNS.
Default gateway
Enter the IP address of the router or gateway if the control unit needs to be connected to the Internet. You may re-
tain the default (0.0.0.0) if the control unit will be used in the local area network only. The gateway settings only ap-
ply to the first network interface (eth0).
ETH0
ETH1 is the device name of the second network interface of the operating system. This interface supports various
modes (inactive, static, dhcp, ethercat, profinet device).
The factory setting is a static IP address for the first network interface, i.e. eth0 (mode: static).
ETH0:1
Virtual extension of network interfaces eth0 and eth1 which allows you to set a second static IP address for the net-
work interface concerned, e.g. for providing separate service access. Only supports mode: static and IP address-
es from another IP address range than that of the basic interface. It will not activate if the basic interface mode
"ethercat" is active.
Network mode: inactive
This mode entirely disables the network interface.
Network mode: static
This mode lets you set a static IP address. Apart from the static IP address you will need the net mask (called Net-
Mask or Subnetmask). This mode should also be enabled if you wish to use the interface for BACnet, Ethernet/IP
or as a Modbus/TCP interface.
Network mode: dhcp
This mode supports a DHCP server's IP address automatically assigned to the network interface when starting the
control unit. Set fields IP Address and NetMask to 0.0.0.0 (default).
Operation
Network mode: ethercat
This mode defines the network interface as an EtherCAT device. We recommend using eth1 for EtherCAT. In CODE-
SYS V3, you will then have to tell the EtherCAT master configuration that the interface selected for EtherCAT (e.g.
"eth1") is a bus interface.
Network mode: profinet device
This function is not supported by PAC120. The left-sided Profinet interface is configured within CODESYS.
ETH1
ETH1 is the device name of the second network interface of the operating system. This network interface is per-
manently set up as a EtherCAT device (mode: ethercat).
5.3.2.2 Menu Item “CAN”
The settings on this page allow you to omit CODESYS V3 and still operate the CAN interfaces at a specific baud
rate. By default ("set by codesys"), the interface remains inactive until initialised by the CODESYS V3 application.
If you tick one of the available baud rates, the CODESYS V3 application will be ignored when booting the system
and the CAN interface will be enabled at the set baud rate. The application can still access the interface.
5.3.2.3 Menu Item „Time and Date“
Use this page to set time of the control unit's real-time clock (RTC) and the time zone. The default time zone on is
set to the Coordinated Universal Time (UTC). What is making this a special setting is that UTC is equivalent to the
control unit's RTC. Changing the UTC time also changes the RTC. Upon delivery, the control unit's RTC is set to
the current German time.
You will need this information to change the time zone of the control unit in order to run functions such as chang-
ing between winter and daylight saving time. Remember to change the default German time to the actual UTC time
before choosing a new time zone. The time and the changed time zone will not display correctly until you have
properly set the RTC/UTC.
Please note that some of the CODESYS V3 system libraries read the time as RTC(UTC).
To show the time and the time zone together, the time reading must first be converted into the local time.
5.3.2.4 Menu Item „VNC-Server“
Use this page to change the resolution and colour settings of the control unit's on-board VNC server. Depending
on the connected e-terminal, the values should be adapted accordingly. If images with alpha channel (e.g. trans-
parent PNGs) are used for visualization, 32 bit colour depth is recommended.
5.3.2.5 Menu Item „FTP-Server“
Use this page to enable or disable the control unit's on-board FTP server which uses TCP port 21. The following
users are privileged to log in to the FTP server:
User name
Root Directory
Change Root Directory
Rights
root
/root
yes
read/write
ftpuser
/flash/ftpupload
no
read/write (ftpupload only)
ftpadm
/flash/ftpupload
yes
read/write (ftpupload only)
ftpreader
/flash/ftpupload
no
read
ftp custom user
(ftpreader/ftpuser/ftpadm)
Einstellbar
adjustable
adjustable
Operation