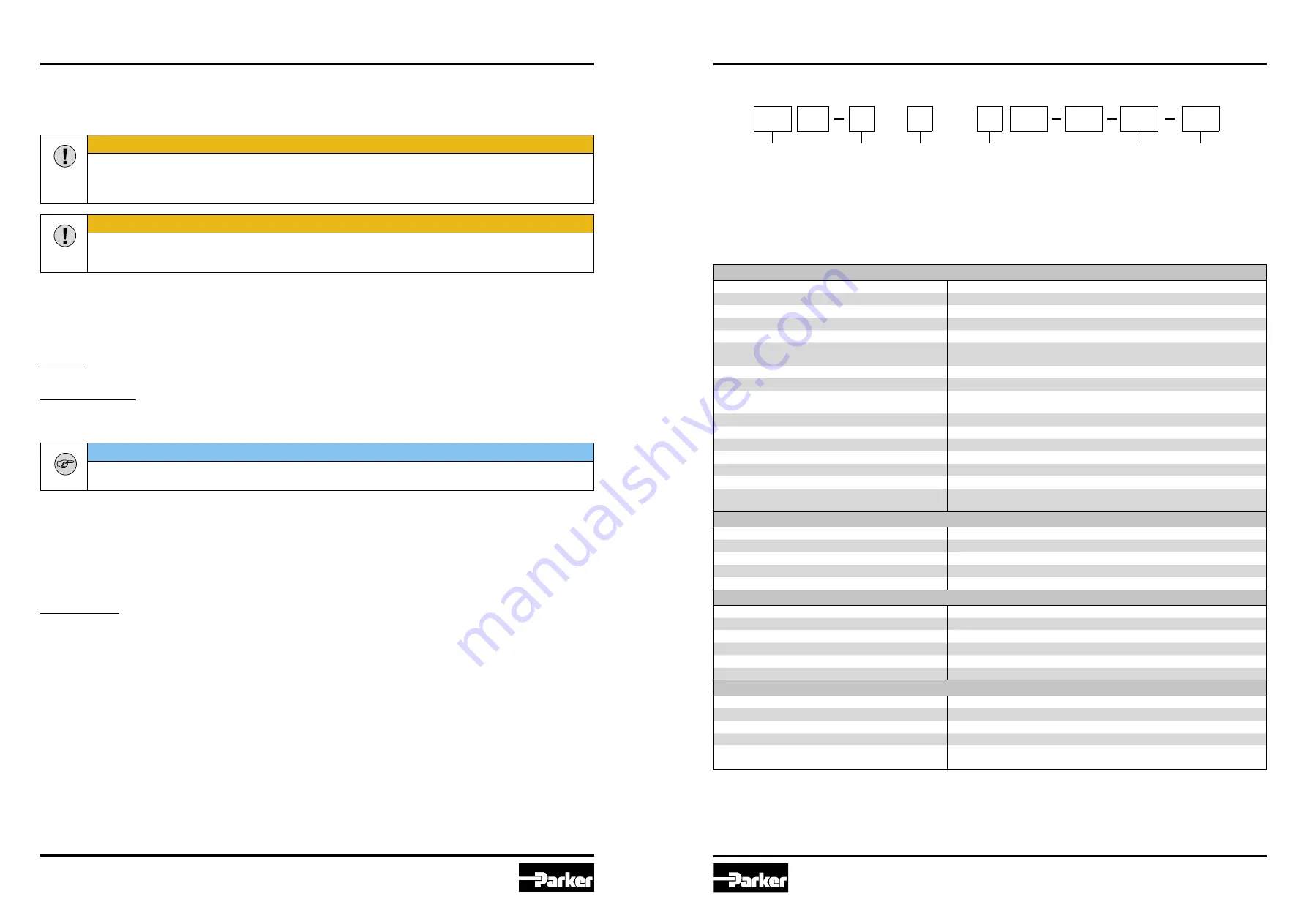
PAC120 5715-719UK.indd 05.06.20
PAC120 5715-719UK.indd 05.06.20
55
54
Parker Automation Controller
Series PAC120
Parker Automation Controller
Series PAC120
Maintenance / Service
7. Maintenance / Servicing
7.1 General
Only qualified persons may work on PAC120.
CAUTION
Do not plug, unplug, mount or touch the connectors during operation.
Doing so may destroy the unit or provoke malfunctions
à
Before working on the unit, turn off all power sources including those feeding power to peripherals such as externally fed
sensors, programming devices etc.
CAUTION
Overheating
Overheating may destroy the unit or provoke malfunctions
à
Verify that the unit's ventilation slots are not covered and that air can circulate.
7.2 Servicing
PAC120 requires neither servicing for the specified service life nor any action if it is kept and operated at the ad-
missible ambient conditions specified in section Technical Data.
7.3 Maintenance
Cleaning
Prevent inadmissible contamination while operating and storing PAC120.
To replace modules
Refer to section 5.1.1 Mechanical Installation
7.4 Repairs / Customer Service
Note
Only the manufacturer or customer service providers authorized by the manufacturer may do repairs and perform corrective main-
tenance.
7.5 Warranty
The statutory period and conditions of warranty apply. Warranty expires if unauthorized attempts are made to re-
pair the unit / product or any other intervention is performed.
7.6 Taking out of Service
Before disposing of PAC120 you must disassemble it and completely take it apart. All metal components can be
given to metal recycling.
Electronic scrap
Sort and dispose of electronic components by type. For details on proper disposal please check your national laws
and regulations making sure that your method of disposal complies with them.
Treat the packaging as recyclable paper and cardboard.
Technical Date
General data
Product indication
PAC120
Item number
PAC120-MWP01-1A
CPU
i.MX6 SoloX Freescale 1 GHz
RAM / remanent memory
256 MB / buffering in flash
Drives
256 MB internal flash memory, SD (HC) card slot
Software
Application: CODESYS V3 Soft SPS optional with SoftMotion
WebVisu, TargetVisu and SoftMotion CNC + Robotics on request
Interfaces
1 x RS232, 1 x USB 2.0
Network
1 x Ethernet 10/100MBit – RJ45
Field bus interfaces
1 x CAN galvanic isolated
EtherCAT
®
internal via E-Bus interface, external via extender modul
Integrated I/Os
1x DI 1 ms
Clock
Real time clock with battery buffering
Power supply
24 V DC (19.2… 28.8)
E-bus current supply
3 A
Output
ca. 3.5 W (@ 24 V DC)
Potential separation
Modules are potential separated against each other and bus
Noise stability
Zone B according to EN 61131-2,
Mounting on grounded rail in grounded control cabinet
Environmental conditions
Protection class
IP20
Mounting position
vertical, stackable
Storage temperature
-25 °C...+70 °C
Operation temperature
0 °C...+55 °C
Relative humidity
5 % … 95 % w/o dew
Mechanical features
Mounting
35 mm DIN rail
Connection IO/power
36-pol spring-type connector with mech. ejector
Signal display
LEDs next to interface
Diagnostics
LED: bus state, module state
Housing (B x H x T)
Aluminum strap, plastic 25 x 120 x 90 mm
Shielding connection
Straight to housing
9. Technical Data
Konformität
2004/108/EC
According to CE
UL
E506274
RoHS
According to RoHS
2014/30/EU
Electro magnetic compatibility EMC
2011/65/EU
Restriction of use of certain hazardous substances in electrical and electronic
equipment (RoHS-2)
8. Ordering Code
Elektro-
hydraulic
controller
120
PAC
Software
IEC
3X
Extended
software
01
00
P
Web
visualization
W
Communication
Profinet IRT
P
01
Extended
communication
OPC UA