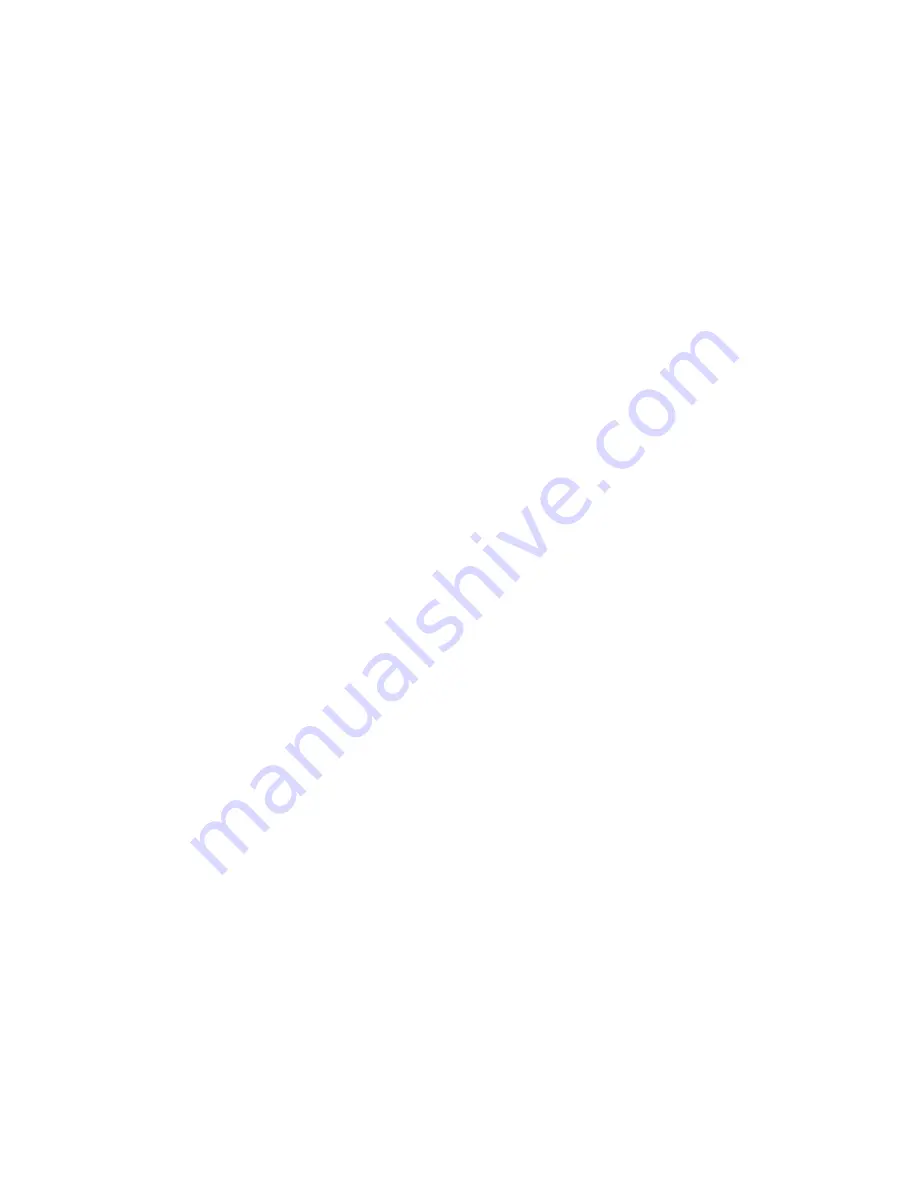
the appropriate Parker Fittings and properly grounded in order to dis-
sipate dangerous static charge buildup, which occurs in, for example,
high velocity CNG dispensing or transfer. Do not use any other Hose
for CNG applications where static charge buildup may occur, even
if electrically conductive. Use of other Hoses in CNG applications or
failure to properly connect or ground this Hose can cause a fire or an
explosion resulting in death, personal injury, and property damage.
Care must also be taken to protect against CNG permeation through
the Hose wall. See section 2.6, Permeation, for more information.
Parker CNG Hose is intended for dispenser and vehicle use within the
specified temperature range. Parker CNG Hose should not be used in
confined spaces or unventilated areas or areas exceeding the specified
temperature range. Final assemblies must be tested for leaks. CNG
Hose Assemblies should be tested on a monthly basis for conductivity
per ANSI/IAS NGV 4.2; CSA 12.52.
Parker manufactures special Hose for aerospace in-flight applica-
tions. Aerospace in-flight applications employing Hose to transmit fuel,
lubricating fluids and hydraulic fluids require a special Hose with a
conductive inner tube. This Hose for in-flight applications is available
only from Parker’s Stratoflex Products Division. Do not use any other
Parker Hose for in-flight applications, even if electrically conductive.
Use of other Hoses for in-flight applications or failure to properly con-
nect or ground this Hose can cause a fire or an explosion resulting in
death, personal injury and property damage. These Hose assemblies
for in-flight applications must meet all applicable aerospace industry,
aircraft engine and aircraft requirements .
2.2 Pressure: Hose, Tube and Fitting selection must be made so that
the published maximum working pressure of the Hose, Tube and
Fittings are equal to or greater than the maximum system pressure.
The maximum working pressure of a Hose, or Tube Assembly is the
lower of the respective published maximum working pressures of the
Hose, Tube and the Fittings used. Surge pressures or peak transient
pressures in the system must be below the published maximum
working pressure for the Hose, Tube and Fitting. Surge pressures and
peak pressures can usually only be determined by sensitive electrical
instrumentation that measures and indicates pressures at millisecond
intervals. Mechanical pressure gauges indicate only average pressures
and cannot be used to determine surge pressures or peak transient
pressures. Published burst pressure ratings for Hose is for manufactur-
ing test purposes only and is no indication that the Product can be used
in applications at the burst pressure or otherwise above the published
maximum recommended working pressure.
2.3 Suction: Hoses used for suction applications must be selected to
insure that the Hose will withstand the vacuum and pressure of the
system. Improperly selected Hose may collapse in suction application.
2.4 Temperature: Be certain that fluid and ambient temperatures, both
steady and transient, do not exceed the limitations of the Hose, Tube,
Fitting and Seals. Temperatures below and above the recommended
limit can degrade Hose, Tube, Fittings and Seals to a point where a
failure may occur and release fluid. Tube and Fittings performances
are normally degraded at elevated temperature. Material compatibility
can also change at temperatures outside of the rated range. Properly
insulate and protect the Hose Assembly when routing near hot objects
(e.g. manifolds). Do not use any Hose in any application where failure
of the Hose could result in the conveyed fluids (or vapors or mist from
the conveyed fluids) contacting any open flame, molten metal, or other
potential fire ignition source that could cause burning or explosion of
the conveyed fluids or vapors.
2.5 Fluid Compatibility: Hose, and Tube Assembly selection must as-
sure compatibility of the Hose tube, cover, reinforcement, Tube, Plating
and Seals with the fluid media used. See the fluid compatibility chart in
the Parker publication for the product being considered or used. This
information is offered only as a guide. Actual service life can only be
determined by the end user by testing under all extreme conditions and
other analysis.
Hose, and Tube that is chemically compatible with a particular fluid
must be assembled using Fittings and adapters containing likewise
compatible seals. Flange or flare processes can change Tube material
properties that may not be compatible with certain requirements such
as NACE
2.6 Permeation: Permeation (that is, seepage through the Hose or
Seal) will occur from inside the Hose or Fitting to outside when Hose or
Fitting is used with gases, liquid and gas fuels, and refrigerants (includ-
ing but not limited to such materials as helium, diesel fuel, gasoline,
natural gas, or LPG). This permeation may result in high concentrations
of vapors which are potentially flammable, explosive, or toxic, and in
loss of fluid. Dangerous explosions, fires, and other hazards can result
when using the wrong Hose for such applications. The system designer
must take into account the fact that this permeation will take place and
must not use Hose or Fitting if this permeation could be hazardous. The
system designer must take into account all legal, government, insur-
ance, or any other special regulations which govern the use of fuels and
refrigerants. Never use a Hose or Fitting even though the fluid compat-
ibility is acceptable without considering the potential hazardous effects
that can result from permeation through the Hose or Tube Assembly.
Permeation of moisture from outside the Hose or Fitting to inside the
Hose or Fitting will also occur in Hose or Tube assemblies, regardless
of internal pressure. If this moisture permeation would have detrimental
effects (particularly, but not limited to refrigeration and air conditioning
systems), incorporation of sufficient drying capacity in the system or
other appropriate system safeguards should be selected and used. The
sudden pressure release of highly pressurized gas could also result in
Explosive Decompression failure of permeated Seals and Hoses.
2.7 Size: Transmission of power by means of pressurized fluid varies
with pressure and rate of flow. The size of the components must be
adequate to keep pressure losses to a minimum and avoid damage due
to heat generation or excessive fluid velocity.
2.8 Routing: Attention must be given to optimum routing to minimize in-
herent problems (kinking or flow restriction due to Hose collapse, twist-
ing of the Hose, proximity to hot objects or heat sources). For additional
routing recommendations see SAE J1273 and ISO 17165-2. Hose
Assemblies have a finite life and should be installed in a manner that
allows for ease of inspection and future replacement. Hose because
of its relative short life, should not be used in residential and commer-
cial buildings inside of inaccessible walls or floors, unless specifically
allowed in the product literature. Always review all product literature for
proper installation and routing instructions.
2.9 Environment: Care must be taken to insure that the Hose, Tube and
Fittings are either compatible with or protected from the environment
(that is, surrounding conditions) to which they are exposed. Envi-
ronmental conditions including but not limited to ultraviolet radiation,
sunlight, heat, ozone, moisture, water, salt water, chemicals and air
pollutants can cause degradation and premature failure.
2.10 Mechanical Loads: External forces can significantly reduce Hose,
Tube and Fitting life or cause failure. Mechanical loads which must
be considered include excessive flexing, twist, kinking, tensile or side
loads, bend radius, and vibration. Use of swivel type Fittings or adapt-
ers may be required to insure no twist is put into the Hose. Use of
proper Hose or Tube clamps may also be required to reduce external
mechanical loads. Unusual applications may require special testing
prior to Hose selection.
2.11 Physical Damage: Care must be taken to protect Hose from wear,
snagging, kinking, bending smaller that minimum bend radius and cut-
ting, any of which can cause premature Hose failure. Any Hose that has
been kinked or bent to a radius smaller than the minimum bend radius,
and any Hose that has been cut or is cracked or is otherwise damaged
should be removed and discarded. Fittings with damages such as
scratches on sealing surfaces and deformation should be replaced.
2.12 Proper End Fitting: See instructions 3.2 through 3.5. These recom-
mendations may be substantiated by testing to industry standards
such as SAE J517 for hydraulic applications, or MIL-A-5070, AS1339,
or AS3517 for Hoses from Parker’s Stratoflex Products Division for
aerospace applications.
2.13 Length: When determining the proper Hose or Tube length of
an assembly, be aware of Hose length change due to pressure, Tube
length change due to thermal expansion or contraction, and Hose or
Tube and machine tolerances and movement must be considered.
When routing short hose assemblies, it is recommended that the mini-
mum free hose length is always used. Consult the hose manufacturer
for their minimum free hose length recommendations. Hose assemblies
should be installed in such a way that any motion or flexing occurs
within the same plane.
2.14 Specifications and Standards: When selecting Hose, Tube and
Fittings, government, industry, and Parker specifications and recom-
mendations must be reviewed and followed as applicable.
2.15 Hose Cleanliness: Hose and Tube components may vary in
cleanliness levels. Care must be taken to insure that the Hose and
Tube Assembly selected has an adequate level of cleanliness for the
application.
2.16 Fire Resistant Fluids: Some fire resistant fluids that are to be con-
veyed by Hose or Tube require use of the same type of Hose or Tube
as used with petroleum base fluids. Some such fluids require a special
Hose, Tube, Fitting and Seal, while a few fluids will not work with any
Hose at all. See instructions 2.5 and 1.5. The wrong Hose, Tube, Fitting
or Seal may fail after a very short service. In addition, all liquids but
pure water may burn fiercely under certain conditions, and even pure
water leakage may be hazardous.
16
17
Содержание MiniKrimp 94C-001-PFD
Страница 1: ...MiniKrimp Crimping Machine Technical Manual...
Страница 18: ...15...
Страница 23: ...20...