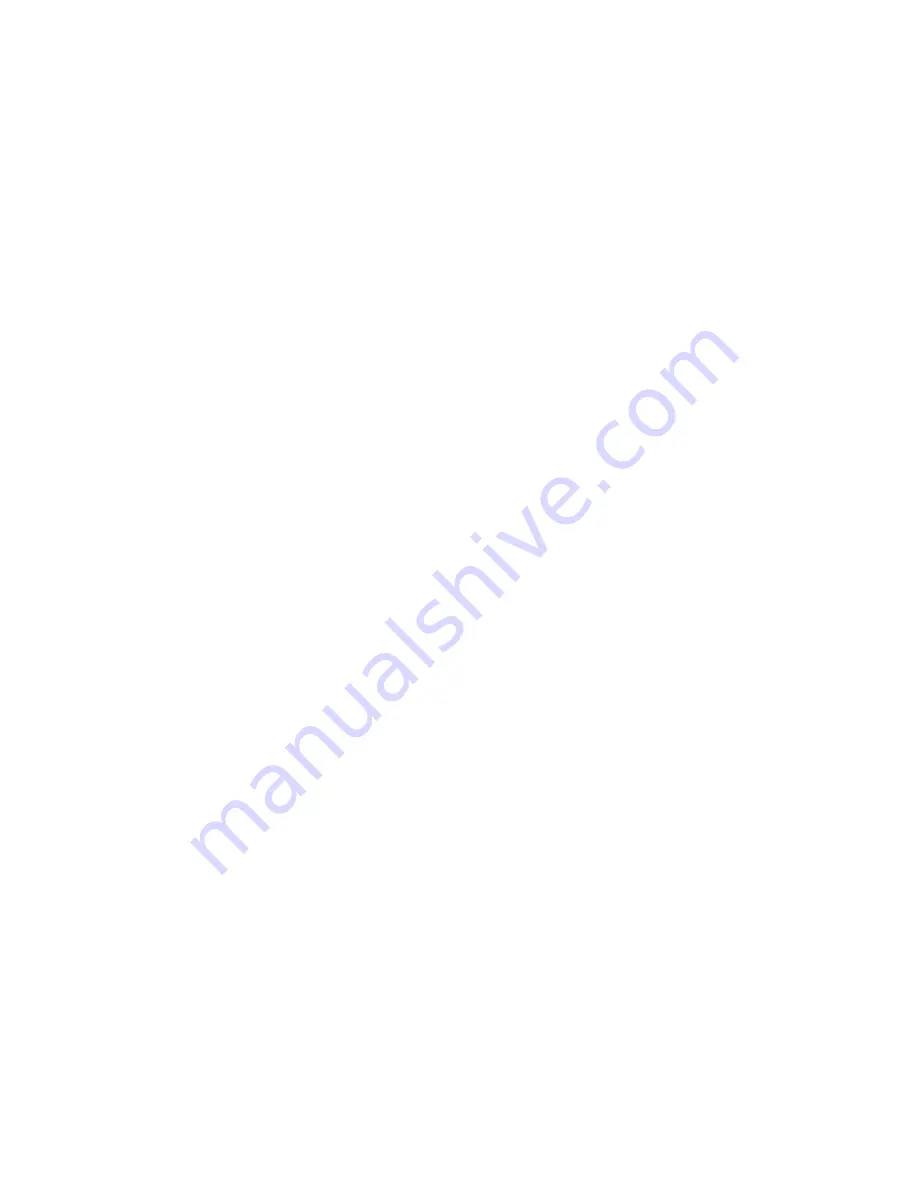
2.17
Radiant Heat: Hose and Seals can be heated to destruction
without contact by such nearby items as hot manifolds or molten metal.
The same heat source may then initiate a fire. This can occur despite
the presence of cool air around the Hose or Seal. Performance of Tube
and Fitting subjected to the heat could be degraded.
2.18
Welding or Brazing: When using a torch or arc welder in close
proximity to hydraulic lines, the hydraulic lines should be removed or
shielded with appropriate fire resistant materials. Flame or weld spatter
could burn through the Hose or Seal and possibly ignite escaping fluid
resulting in a catastrophic failure. Heating of plated parts, including
Hose Fittings and adapters, above 450°F (232°C) such as during weld-
ing, brazing or soldering may emit deadly gases. Any elastomer seal
on fittings shall be removed prior to welding or brazing, any metallic
surfaces shall be protected after brazing or welding when necessary.
Welding and brazing filler material shall be compatible with the Tube
and Fitting that are joined.
2.19 Atomic Radiation: Atomic radiation affects all materials used
in Hose and Tube assemblies. Since the long-term effects may be
unknown, do not expose Hose or Tube assemblies to atomic radiation.
Nuclear applications may require special Tube and Fittings.
2.20 Aerospace Applications: The only Hose, Tube and Fittings that
may be used for in-flight aerospace applications are those available
from Parker’s Stratoflex Products Division. Do not use any other Hose
or Fittings for in-flight applications. Do not use any Hose or Fittings from
Parker’s Stratoflex Products Division with any other Hose or Fittings,
unless expressly approved in writing by the engineering manager or
chief engineer of Stratoflex Products Division and verified by the user’s
own testing and inspection to aerospace industry standards.
2.21 Unlocking Couplings: Ball locking couplings or other Fittings
with quick disconnect ability can unintentionally disconnect if they
are dragged over obstructions, or if the sleeve or other disconnect
member, is bumped or moved enough to cause disconnect. Threaded
Fittings should be considered where there is a potential for accidental
uncoupling.
3.0
HOSE AND FITTINGS ASSEMBLY AND INSTALLATION
INSTRUCTIONS
3.1
Component Inspection: Prior to assembly, a careful examina-
tion of the Hose and Fittings must be performed. All components must
be checked for correct style, size, catalog number, and length. The
Hose must be examined for cleanliness, obstructions, blisters, cover
looseness, kinks, cracks,cuts or any other visible defects. Inspect
the Fitting and sealing surfaces for burrs, nicks, corrosion or other
imperfections. Do NOT use any component that displays any signs of
nonconformance.
3.2 Hose and Fitting Assembly: Do not assemble a Parker Fitting on a
Parker Hose that is not specifically listed by Parker for that Fitting, un-
less authorized in writing by the engineering manager or chief engineer
of the appropriate Parker division. Do not assemble a Parker Fitting on
another manufacturer’s Hose or a Parker Hose on another manufac-
turer’s Fitting unless (i) the engineering manager or chief engineer of
the appropriate Parker division approves the Assembly in writing or that
combination is expressly approved in the appropriate Parker literature
for the specific Parker product, and (ii) the user verifies the Assembly
and the application through analysis and testing. For Parker Hose that
does not specify a Parker Fitting, the user is solely responsible for the
selection of the proper Fitting and Hose Assembly procedures. See
instruction 1.4.
To prevent the possibility of problems such as leakage at the Fitting or
system contamination, it is important to completely remove all debris
from the cutting operation before installation of the Fittings. The Parker
published instructions must be followed for assembling the Fittings on
the Hose. These instructions are provided in the Parker Fitting catalog
for the specific Parker Fitting being used, or by calling 1-800-CPARK-
ER, or at www.parker.com.
3.3 Related Accessories: Do not crimp or swage any Parker Hose or
Fitting with anything but the listed swage or crimp machine and dies in
accordance with Parker published instructions. Do not crimp or swage
another manufacturer’s Fitting with a Parker crimp or swage die unless
authorized in writing by the engineering manager or chief engineer of
the appropriate Parker division.
3.4 Parts: Do not use any Parker Fitting part (including but not limited
to socket, shell, nipple, or insert) except with the correct Parker mating
parts, in accordance with Parker published instructions, unless autho-
rized in writing by the engineering manager or chief engineer of the
appropriate Parker division.
3.5 Field Attachable/Permanent: Do not reuse any field attachable Hose
Fitting that has blown or pulled off a Hose. Do not reuse a Parker per-
manent Hose Fitting (crimped or swaged) or any part thereof. Complete
Hose Assemblies may only be reused after proper inspection under
section 4.0. Do not assemble Fittings to any previously used hydraulic
Hose that was in service, for use in a fluid power application.
3.6 Pre-Installation Inspection: Prior to installation, a careful exami-
nation of the Hose Assembly must be performed. Inspect the Hose
Assembly for any damage or defects. DO NOT use any Hose Assembly
that displays any signs of nonconformance.
3.7 Minimum Bend Radius: Installation of a Hose at less than the
minimum listed bend radius may significantly reduce the Hose life.
Particular attention must be given to preclude sharp bending at the
Hose to Fitting juncture. Any bending during installation at less than the
minimum bend radius must be avoided. If any Hose is kinked during
installation, the Hose must be discarded.
3.8 Twist Angle and Orientation: Hose Assembly installation must be
such that relative motion of machine components does not produce
twisting.
3.9 Securement: In many applications, it may be necessary to restrain,
protect, or guide the Hose to protect it from damage by unnecessary
flexing, pressure surges, and contact with other mechanical compo-
nents. Care must be taken to insure such restraints do not introduce
additional stress or wear points.
3.10 Proper Connection of Ports: Proper physical installation of the
Hose Assembly requires a correctly installed port connection insuring
that no twist or torque is transferred to the Hose when the Fittings are
being tightened or otherwise during use.
3.11 External Damage: Proper installation is not complete without
insuring that tensile loads, side loads, kinking, flattening, potential
abrasion,thread damage or damage to sealing surfaces are corrected
or eliminated. See instruction 2.10.
3.12 System Checkout: All air entrapment must be eliminated and the
system pressurized to the maximum system pressure (at or below the
Hose maximum working pressure) and checked for proper function and
freedom from leaks. Personnel must stay out of potential hazardous
areas while testing and using.
3.13 Routing: The Hose Assembly should be routed in such a manner
so if a failure does occur, the escaping media will not cause personal
injury or property damage. In addition, if fluid media comes in contact
with hot surfaces, open flame or sparks, a fire or explosion may occur.
See section 2.4.
3.14 Ground Fault Equipment Protection Devices (GFEPDs): WARN-
ING! Fire and Shock Hazard. To minimize the danger of fire if the heat-
ing cable of a Multitube bundle is damaged or improperly installed, use
a Ground Fault Equipment Protection Device. Electrical fault currents
may be insufficient to trip a conventional circuit breaker.
For ground fault protection, the IEEE 515: (www.ansi.org) standard for
heating cables recommends the use of GFEPDs with a nominal 30 mil-
liampere trip level for “piping systems in classified areas, those areas
requiring a high degree of maintenance, or which may be exposed to
physical abuse or corrosive atmospheres”.
4.0
TUBE AND FITTINGS ASSEMBLY AND INSTALLATION
INSTRUCTIONS
4.1 Component Inspection: Prior to assembly, a careful examination
of the Tube and Fittings must be performed. All components must be
checked for correct style, size, material, seal, and length. Inspect the
Fitting and sealing surfaces for burrs, nicks, corrosion, missing seal
or other imperfections. Do NOT use any component that displays any
signs of nonconformance.
4.2 Tube and Fitting Assembly: Do not assemble a Parker Fitting with
a Tube that is not specifically listed by Parker for that Fitting, unless
authorized in writing by the engineering manager or chief engineer of
the appropriate Parker division. The Tube must meet the requirements
specified to the Fitting. The Parker published instructions must be
followed for assembling the Fittings to a Tube. These instructions are
provided in the Parker Fitting catalog for the specific Parker Fitting be-
ing used, or by calling 1-800-CPARKER, or at www.parker.com.
4.3 Related Accessories: Do not preset or flange Parker Fitting compo-
nents using another manufacturer’s equipment or procedures unless
authorized in writing by the engineering manager or chief engineer of
the appropriate Parker division. Tube, Fitting component and tooling
must be check for correct style, size and material. Operation and
maintenance of Related Accessories must be in accordance with the
operation manual for the designated Accessory.
4.4 Securement: In many applications, it may be necessary to restrain,
protect, or guide the Tube to protect it from damage by unnecessary
flexing, pressure surges, vibration, and contact with other mechani-
cal components. Care must be taken to insure such restraints do not
introduce additional stress or wear points.
18
Содержание MiniKrimp 94C-001-PFD
Страница 1: ...MiniKrimp Crimping Machine Technical Manual...
Страница 18: ...15...
Страница 23: ...20...