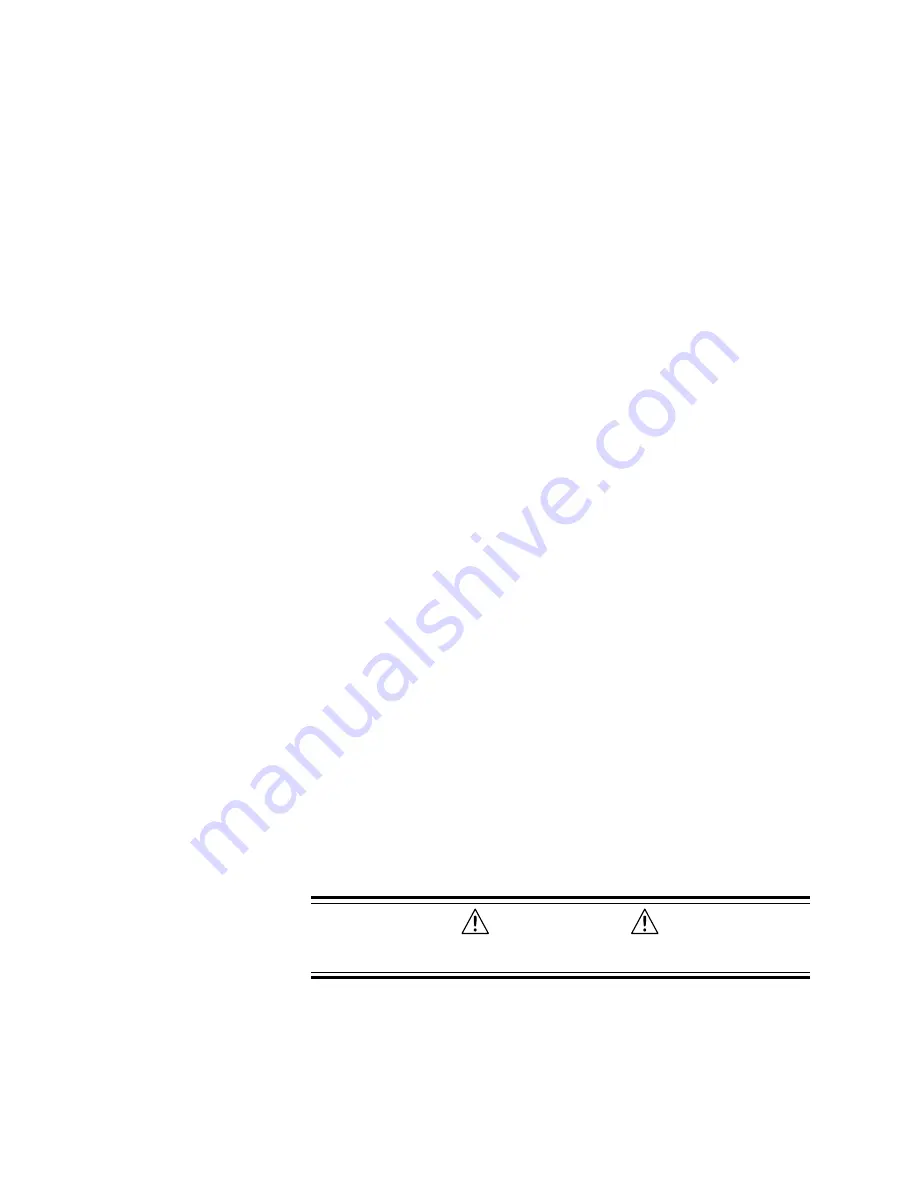
Chapter 3 – Configuration
31
6.
Connect a second channel of your oscilloscope to the drive’s ANALOG
MONITOR B (pin 22). Connect your oscilloscope’s ground to the drive’s ANALOG
GROUND (pin 25).
Adjust your oscilloscope to display commanded versus actual velocity. (The analog
monitors can be scaled, in percent, with the DMONAS and DMONBS commands.
You may need to set these to large values if the maximum velocity is small.)
7.
Enable the drive and observe your system’s response.
Ringing or an oscillating response indicates that the velocity loop bandwidth is too
high, or the velocity loop damping is too low. To eliminate oscillations:
• decrease bandwidth using the DVBW command; then, if necessary:
• adjust damping by using the SGVRAT command. Use the value that
gives the best performance.
• in applications with backlash or high static friction, disabling the velocity
integrator (SGINTE0) can help improve stability.
A sluggish response indicates that velocity loop bandwidth is too low, or velocity
loop damping is too high. To improve the response:
• increase bandwidth by using the DVBW command; then, if necessary:
• adjust damping by using the SGVRAT command. Use the value that
gives the best performance.
NOTE: Ringing, oscillations, or a sluggish response can also indicate inaccurate
drive settings for LJRAT or LDAMP.
8.
OPTIONAL: Null the Input Offset
First: command zero volts by using either of two methods:
• Method 1: connect your controller or command voltage source, and
command zero volts; or:
• Method 2: disconnect the controller or command voltage source, and
short CMD+ to CMD- (pin 23 to pin 24).
Second: Issue a DCMDZ command to null any offset at the command input.
9.
After you achieve a satisfactory system response, reconfigure the drive for velocity
mode (DMODE4). This completes the advanced tuning procedure.
If ringing or oscillations persist, and do not seem to be affected by bandwidth
adjustments, you may need to use notch filters or lead/lag filters. See the Filter
Adjustments procedure at the end of this Tuning section.
Position Mode Tuning
For most applications, the default tuning parameters for velocity and position
modes are set to provide good, stiff motor shaft performance for a given load
setting. With the default tuning parameters set in the Express Setup procedure, you
need only set the system load-to-rotor inertia ratio and your system will be tuned.
If your system has significant mechanical damping, you may need to set the
system damping as well. Should you wish to modify the default values and fine
tune your system for position mode, use the following procedures.
WARNING
This procedure causes the motor shaft to move. Make sure that shaft motion will
not damage equipment or injure personnel.
www.comoso.com