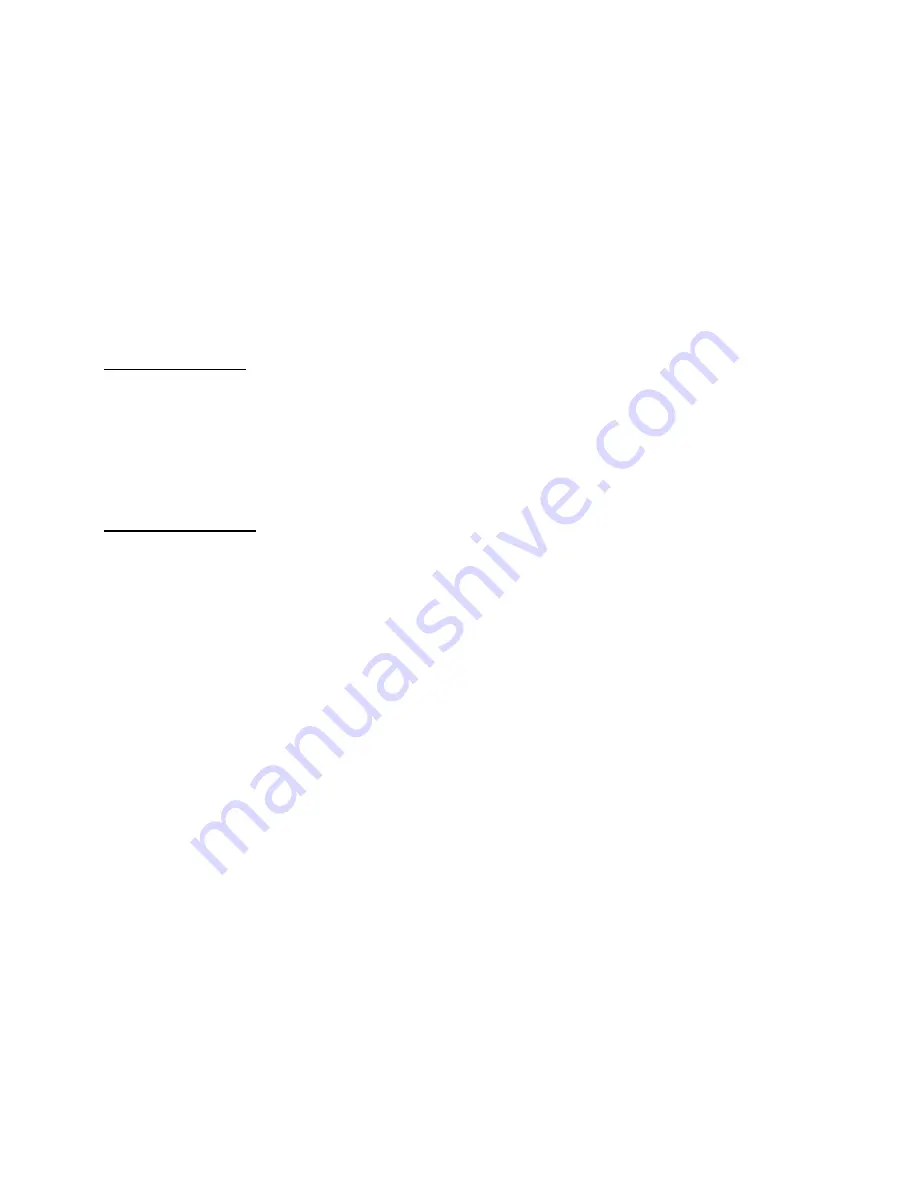
Appendix A – Resonance, Ringing & Damping
55
Anti-Resonance (AR)
Anti-resonance monitors the ZETA6xxx’s motor
terminals, and looks at power exchange between the
ZETA6xxx and motor. From this, it extracts information
about error in rotor position caused by resonance or
ringing. It modifies the internal motor current command
to correct for the error.
Anti-resonance is a general-purpose circuit. It corrects
rotor position error, without knowledge about the
system—whether the motor is large or small, or the system
inertia is high or low. You cannot modify the circuit’s
gains, or customize it for a particular application—but,
anti-resonance is easy to use. When enabled via DIP
switch, SW2-2, it works automatically.
Anti-Resonance Gain
Large rotor motors, or motors driving large inertial loads,
may require a reduction in anti-resonance gain. This will
be evident if the load becomes too responsive and settles
in an overly abrupt manner for your application. SW2-4
should be off if the system's inertia is 20 kg-cm
2
or less.
SW2-4 should be on if system's inertia is greater than 20
kg-cm
2
.
Anti-Resonance Phase
This switch allows a broad range of motors to benefit from
the anti-resonance damping technique. SW2-3 should be
off if your mechanical system's resonant frequency is 80
Hz or less. SW2-3 should be on if your mechanical
system's resonant frequency is greater than 80 Hz, if your
motor drives an extremely low inertia load, or if your
system has an extremely high torque to inertia ratio.
Active Damping (AD)
Active damping monitors the ZETA6xxx’s motor
terminals and, like anti-resonance, uses the same current
command modulator to modify motor current.
Active damping uses a different method to extract
information about rotor position error, however. The
circuit’s gains are adjustable—you can configure it for
your particular system. DIP switch SW2 allows you to
scale the circuit for motor inductance and static torque.
The AD rotary switch scales the circuit for system inertia.
The active damping circuit uses this information for two
purposes:
1. It determines error in rotor position very accurately.
2. It adjusts the gains of its feedback loop, based upon
how much inertia the system has, and how much
torque the motor can produce.
If the rotor rings or vibrates, the active damping circuit
will detect the corresponding error in rotor position. It
will then modify the motor current command to damp the
ringing.
DIP switches on top of the ZETA6xxx set the amount of
motor current during normal operations; this current is
constant. To damp ringing, the active damping circuit can
cause the ZETA6xxx to produce up to twice as much
current as is set by the DIP switches. The extra current is
only applied during damping oscillations, and lasts a very
brief time.
Electronic Viscosity (EV)
The ZETA6xxx uses closed-loop current control to
develop and maintain precise currents in the motor phases.
When EV is off, the current loops have a bandwidth of
approximately 1000 Hz. Because this bandwidth is well
beyond the knee of step motor speed-torque curves, the
current loop dynamics do not limit the response of the
motor.
EV monitors motor velocity, and turns on below 3 rps. It
“detunes” the current loop compensation values and brings
the bandwidth down to 150 Hz. With this lower
bandwidth, the drive electronics become “sluggish.”
Ordinarily, when the rotor oscillates, it generates current
in the motor’s coils; but with EV’s lower bandwidth, the
drive’s electronics impede the flow of current caused by
oscillations.
The effect on the motor is as if there were a viscous drag
on the rotor. At the end of a move, oscillations are
damped, and the rotor quickly comes to rest. After
accelerating or decelerating to velocities below 3 rps, the
rotor quickly settles at the commanded velocity. During
moves below 3 rps, EV significantly reduces low speed
velocity ripple.
EV is a “passive” circuit. It imposes viscosity on the
system, but has no feedback loop to monitor the effect of
the viscosity. EV keeps the amount of viscosity the same,
regardless of the response of the system.
You can adjust the amount of viscosity by using the
DELVIS
command. This allows you to tailor the circuit
for different motor sizes and system inertias, and adapt it
to your application.
Current Loop Gain
SW2-5 should be off for normal current-loop gain. You
can reduce the responsiveness of the current control loop
by setting the SW2-5 to the on position. This may be
necessary when connecting a motor with an extremely low
inductance value, on the order of 2 mH. If you hear a high
pitched (10kHz) oscillation from the motor, you can
decrease or eliminate the oscillation by reducing loop
gain. Excessive loop gain may cause motor faults at high
loads; reduce loop gain to eliminate this problem.
Artisan Technology Group - Quality Instrumentation ... Guaranteed | (888) 88-SOURCE | www.artisantg.com