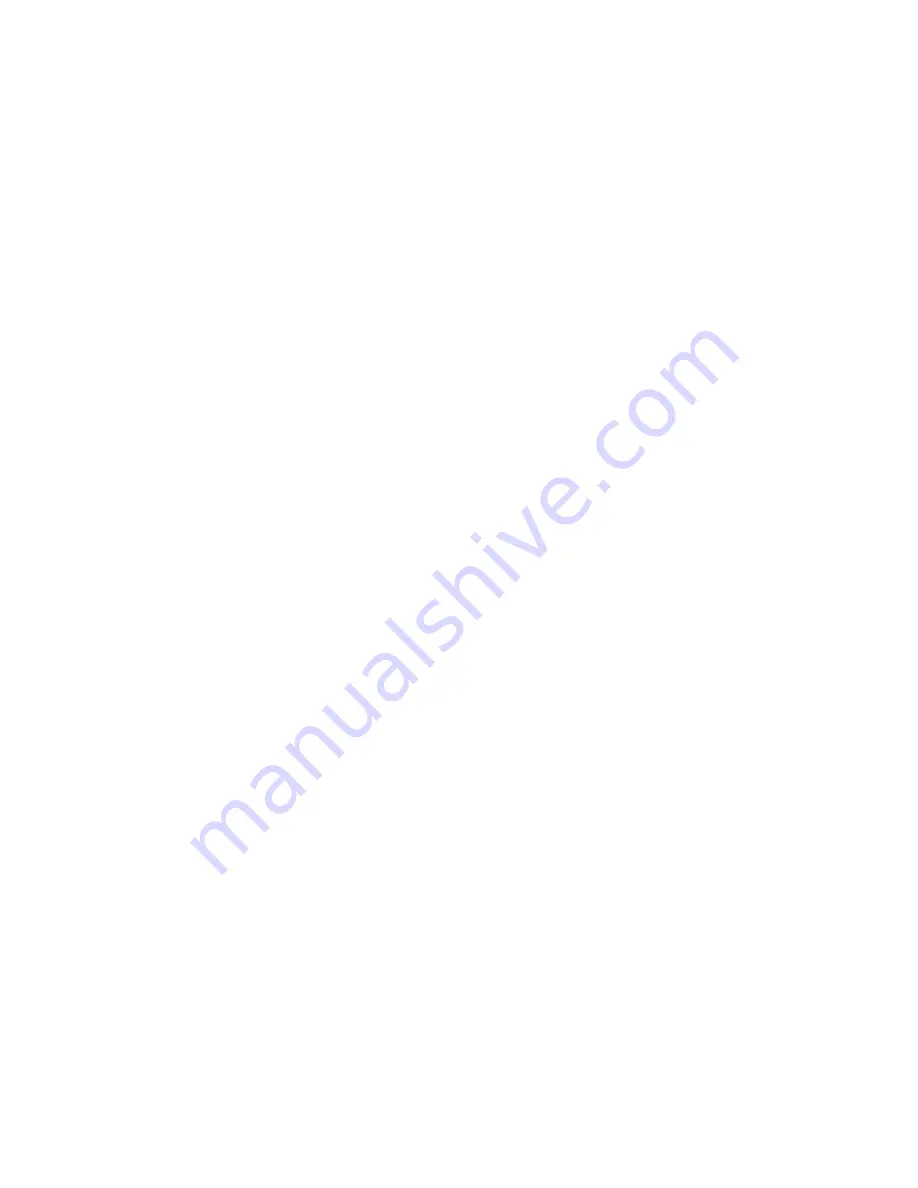
6-40
Programming Your Application
590 Series DC Digital Converter
Functional Description
The following block diagram shows the internal structure of the PID block.
PID is used to control the response of any closed loop system. It is used specifically in system
applications involving the control of drives to allow zero steady state error between Reference
and Feedback, together with good transient performance.
P
roportional Gain (PROP. GAIN)
This is used to adjust the basic response of the closed loop control system. It is defined
as the portion of the loop gain fed back to make the complete control loop stable. The
PID error is multiplied by the Proportional Gain to produce an output.
DIVIDER 1
Range: -3.0000 to 3.0000
This divides Input 1 by a factor (Divider 1).
DIVIDER 2
Range: -3.0000 to 3.0000
This divides Input 2 by a factor (Divider 2).
ENABLE
Range:
ENABLED/DISABLED
A digital input which resets the (total) PID Output as well as the integral term when FALSE.
INT. DEFEAT
Range:
ON/OFF
A digital input which resets the integral term when TRUE. The block transfer function then
becomes P+D only.
FILTER T.C.
Range: 0.000s to 10.000s
In order to attenuate high-frequency noise a first order filter is added in conjunction with the
differentiator. The ratio k of the Derivative Time Constant (Td) over the Filter Time Constant
(Tf) (typically 4 or 5) determines the high-frequency lift of the transfer function. For Tf = 0 this
filter is eliminated.
MODE
Range: 0 to 4
This determines the law which the profiler follows versus diameter.
For Mode = 0, Profiled Gain = constant = P.
For Mode = 1, Profiled Gain = A * (diameter - min diameter) + B.
For Mode = 2, Profiled Gain = A * (diameter - min diameter)^2 + B.
For Mode = 3, Profiled Gain = A * (diameter - min diameter)^3 + B.
For Mode = 4, Profiled Gain = A * (diameter - min diameter)^4 + B.
MIN PROFILE GAIN
Range: 0.00% to 100.00%
This expresses the minimum gain required at min diameter (core) as a percentage of the (max) P
gain at full diameter (100%).
PROFILED GAIN
Range: 0.0 to 100.0
The output of a profiler block which varies the gain versus diameter. This is primarily to be used
with Speed Profiled Winders for compensation against varying diameter and therefore inertia.
When MODE is not ZERO (see above) this overrides the P gain above.
PID OUTPUT
Refer to the DIAGNOSTICS function block description, page 6-18.
PID CLAMPED
Refer to the DIAGNOSTICS function block description, page 6-18.
PID ERROR
Refer to the DIAGNOSTICS function block description, page 6-18.
Содержание 590 series
Страница 12: ...605 Frequency Inverter HA389591 Issue 1 Contents Contents Page Cont 12...
Страница 16: ...1 4 Getting Started 590 Series Digital Converter...
Страница 22: ...2 6...
Страница 43: ...Installing the Converter 3 21 590D DC Digital Converter HA467078 Figure 3 6 110A 150A Stack Assembly...
Страница 44: ...3 22 Installing the Converter 590D DC Digital Converter HA467078 Figure 3 7 180A Stack Assembly...
Страница 45: ...Installing the Converter 3 23 590D DC Digital Converter HA467078 Figure 3 8 270A Stack Assembly...
Страница 46: ...3 24 Installing the Converter 590D DC Digital Converter HA467078 Figure 3 9 360A Stack Assembly...
Страница 47: ...Installing the Converter 3 25 590D DC Digital Converter HA467078 Figure 3 10 450A Stack Assembly...
Страница 48: ...3 26 Installing the Converter 590D DC Digital Converter HA467078 Figure 3 11 720A Stack Outline Drawing...
Страница 49: ...Installing the Converter 3 27 590D DC Digital Converter HA467078 Figure 3 12 720A Stack Outline Drawing...
Страница 64: ...3 42 Installing the Converter 590D DC Digital Converter HA467078...
Страница 82: ...4 18 Operating the Converter 590 Series DC Digital Converter...
Страница 90: ...5 8 The Man Machine Interface MMI 590 Series DC Digital Converter...
Страница 168: ...9 6 Control Loops 590 Series DC Digital Converter...
Страница 222: ...13 14 Standard and Optional Equipment 590 Series DC Digital Converter...
Страница 234: ...15 2 The Default Application 590 Series DC Digital Converter...
Страница 242: ......