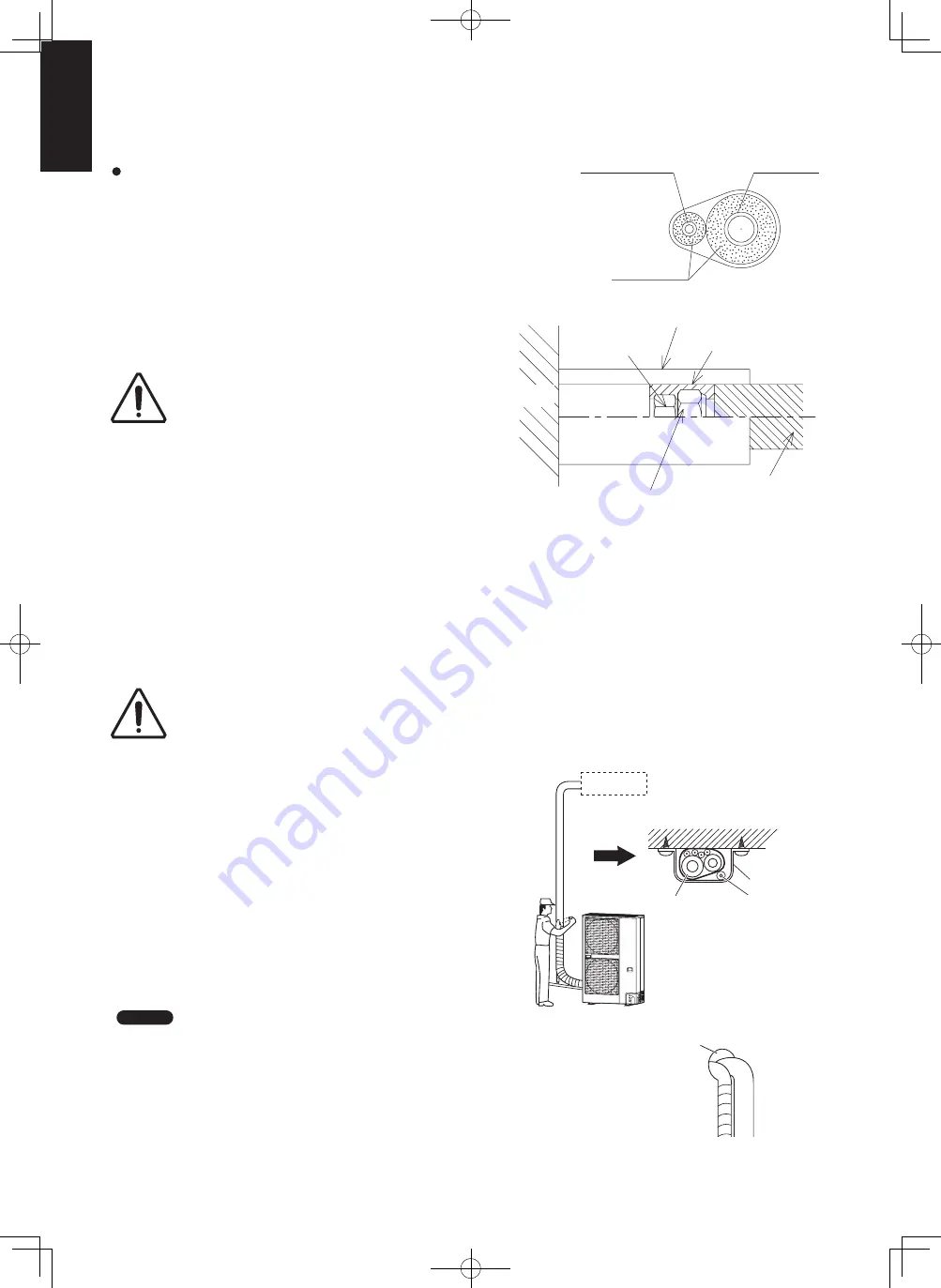
1-46
1
1
3. Insulating the Refrigerant Tubing
Tubing Insulation
Thermal insulation must be applied to all units tubing,
including distribution joint (field supply).
* For gas tubing, the insulation material must be heat
resistant to 120°C or above.
For other tubing, it must be resistant to 120°C or above.
For other tubing, it must be heat resistant to 80°C or above.
Insulation material thickness must be 10 mm or greater.
If the conditions inside the ceiling exceed DB 30°C and
RH 70%, increase the thickness of the gas tubing
insulation material by 1 step.
Two tubes arranged together
Liquid tubing
Gas tubing
Insulation
Fig. 1- 25
If the exterior of the outdoor unit valves has been
finished with a square duct covering, make sure you
allow sufficient space to access the valves and to
allow the panels to be attached and removed.
Taping the flare nuts
Wind the white insulation tape around the flare nuts at the gas tube connections.
Then cover up the tubing connections with the flare insulator, and fill the gap at the
union with the supplied black insulation tape.
Finally, fasten the insulator at both ends with the supplied vinyl clamps. (Fig. 1- 26)
WARNING
WARNING
Flare insulator (supplied)
Insulation tape
(white)(supplied)
Tube insulator
(not supplied)
Heat resistant
120°C or above
Flare union
Flare nut
Unit side
Fig. 1- 26
Insulation material
The material used for insulation must have good insulation characteristics, be easy to use, be age resistant,
and must not easily absorb moisture.
After a tube has been insulated, never try to bend it into a narrow curve because
it can cause the tube to break or crack.
Never grasp the drain or refrigerant connecting outlets when moving the unit.
4. Taping the Tubes
(1) At this time, the refrigerant tubes (and electrical wiring
if local codes permit) should be taped together with
armoring tape in 1 bundle. To prevent condensation
from overflowing the drain pan, keep the drain hose
separate from the refrigerant tubing.
(2) Wrap the armoring tape from the bottom of the outdoor
unit to the top of the tubing where it enters the wall.
As you wrap the tubing, overlap half of each previous
tape turn.
(3) Clamp the tubing bundle to the wall, using 1 clamp
approx. each meter. (Fig. 1- 27)
Fig. 1- 27
NOTE
Do not wind the armoring tape too tightly since this will
decrease the heat insulation effect.
Also ensure that the condensation drain hose splits away
from the bundle and drips clear of the unit and the tubing.
5. Finishing the Installation
After finishing insulating and taping over the tubing, use sealing putty to seal
off the hole in the wall to prevent rain and draft from entering. (Fig. 1- 28)
Apply putty here
Tubing
Fig. 1- 28
Insulated tubes
Drain hose
Clamp
Ensure to fi ll only with liquid refrigerant when refi lling.
If gas refrigerant is fi lled, the refrigerant composition will
not be balanced and will cause abnormal operation.
Cylinder with
a siphon tube
Liquid refrigerant
Siphon tube
Cylinder
Cylinder
Gas refrigerant
Possible
(For refi lling due to a leak)
Not possible
1-12. VACUUM PURGING
1-13. REGARDING REFRIGERANT FILLING
Precautions during refrigerant fi lling
Charging with refrigerant
If using cylinders as shown in the bottom left diagram; without
a siphon tube inside, turn it upside down and use it.
(It is recommended to use the manifold with the side glass.)
Use tools that are designed specifi cally for R410A, for pressure resistance and to prevent mixing impurities.
Fill the refrigerant from the 3-way valve’s service port on the liquid-side.
For fi lling and replacing all refrigerant
For refi lling refrigerant, fi rst collect all residual refrigerant and after vacuum dehydration using the vacuum pump. Refi ll the
refrigerant according to the prescribed amount stated on the placard affi xed to this unit.
Precautions after the pipes’ connection have completed
Ensure to open the 3-way valve after completing the piping installation, leak test and vacuuming. If it is closed during operation,
it can lead to compressor failure.
At the time of shipment from the factory, this unit is charged with enough refrigerant for an equivalent pipe length of 30m.
If the equivalent pipe length used will be 30m or less, no additional charging will be necessary.
If the equivalent pipe length will be between 30 and 120m, charge with additional refrigerant according to the equivalent length
given in the table below.
For standard type
Pump down operation
Please refer to the service manual for pump down method.
Liquid refrigerant
Model name
Add. gas amount
Equivalent length
Minimum length
m
5
m
0
2
1
m
/
g
0
5
A
8
E
2
E
P
0
0
2
-
U
m
5
m
0
2
1
m
/
g
0
8
A
8
E
2
E
P
0
5
2
-
U
Keep 3-way valve fully closed and pressurize through 3-way valve service port.
Do not pressurize to the default value at once. Pressurize gradually.
1 Pressurize to 0.5MPa (5k
g
f/cm²G) and then leave it for 5 minutes
to ensure that the pressure does not drop.
2 Pressurize to 1.5MPa (15k
g
f/cm²G) and leave it for 5 minutes
to ensure that the pressure does not drop.
3 For the test, pressurize to 4.15MPa and leave it for about 1 day
to ensure that the pressure does not drop.
Leak Tightness Test Method
Vacuum Purging
Use a vacuum pump (with back-fl ow prevention device) to vacuum
through the 3-way valve service port to achieve the pressure below
-101kPa (5 Toor).
Air and moisture remaining in the refrigerant system due to poor
vacuum drying can cause performance decrement and malfunction
of the compressor.
Outdoor unit
3-way
valve
Indoor unit
Use nitrogen gas for the leak tightness test.
Using fl ammable gas can cause an explosion.
Pressure
meter
Nitrogen
Refrigerant
meter
Vacuum
pump
SM830252-00_欧州_Single_天埋.indb 46
16/08/26 10:40:22
Содержание S-200PE2E5
Страница 70: ...1 64 MEMO SM830252 00_欧州_Single_天埋 indb 64 16 08 26 10 40 29 ...
Страница 86: ... MEMO 3 4 SM830252 00_欧州_Single_天埋 indb 4 16 08 08 13 11 45 ...
Страница 166: ... MEMO 7 16 SM830252 00_欧州_Single_天埋 indb 16 16 08 27 8 24 20 ...
Страница 188: ...201608 SM830252 00_欧州_Single_天埋 indb 1 16 08 10 15 45 43 ...