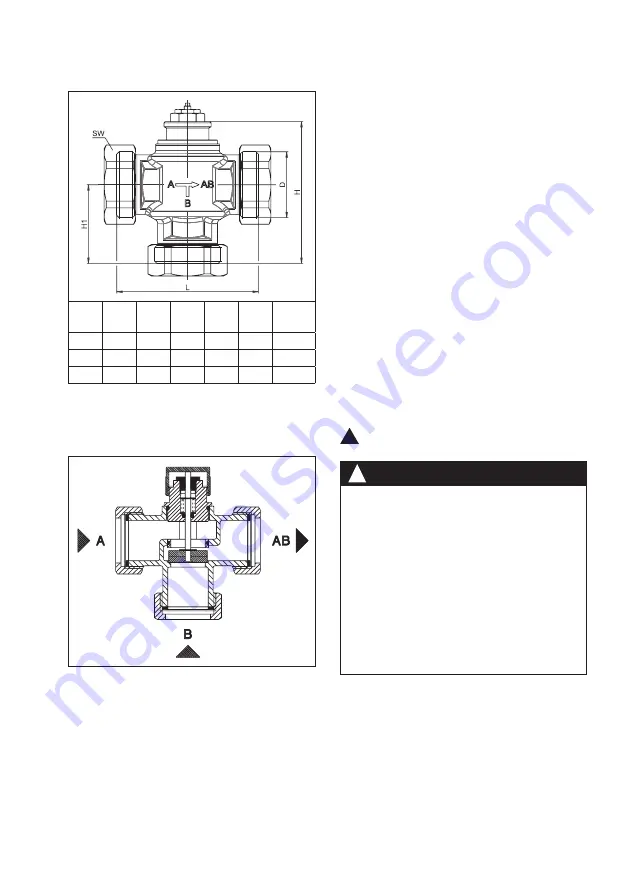
7
Illustr. 4.1 Dimensions
*SW = Spanner size
5 Construction and function
4.3 Dimensions
DN
D
ISO 228
L
H
H1
SW*
Weight
[kg]
20
G 1
80
88
47
37
0.8
25
G 1
1
⁄
4
90
91
50
46
1.2
40
G 2
115
106
64
68
2.2
Illustr. 5.1 Sectional view
Oventrop three-way mixing valves “Tri-M TR” have
two inlet ports (A and B) and one outlet port (AB).
Depending on the position of the valve disc, the cold
and hot water is mixed.
For commercial two point controls, electrothermal or
electromotive actuators with connection thread M 30
x 1.5 are used. The straight port (A-AB) is opened with
current “off” and the port opposite the actuator (B) is
closed. Reversed action with current “on”.
When using a steady control, Oventrop temperature
controllers with immersion sensor or Oventrop
temperature controllers with contact sensor are used.
These are proportional controllers working without
auxiliary energy allowing for intermediate positions.
With the temperature at the sensor rising, the straight
port (A-AB) is opened and the angle port (B-AB) is
closed.
Markings
Markings on the body:
OV
Oventrop
DN
Nominal size
PN
Nominal pressure
A, B, AB
Connections
6 Installation
Oventrop three-way mixing valves “Tri-M TR” are
supplied with collar nuts for the connection of weldable
tailpipes made of steel or solder or screwed tailpipes
made of brass.
The valve must only be installed into a clean pipework
system and must only be operated with a clean
unpolluted fluid. Installation is possible in any orientation.
Please observe:
Some electric actuators must not be
installed in a vertical downward position.
Observe warning advice under paragraph 2
(safety notes)!
!
PRECAUTION
!
– Do not use any lubricant or oil when installing the
fitting as these may destroy the seals. If necessary,
all dirt particles and lubricant or oil residues must
be removed from the pipework by flushing the
latter.
– When choosing the operating fluid, the latest
technical development has to be considered (e.g.
VDI 2035).
– A strainer must be installed in front of the valve.
– Please protect against external forces (e.g.
impacts, vibrations etc.).
– The pipes must be fixed additionally in case of
tensile or flectional strains.
– Provide expansion loops for thermal conditional
changes in length of pipes.
After installation, check all installation points for leaks.
Before commissioning, the installation has to be filled
and bled with due consideration of the permissible
operating pressures.