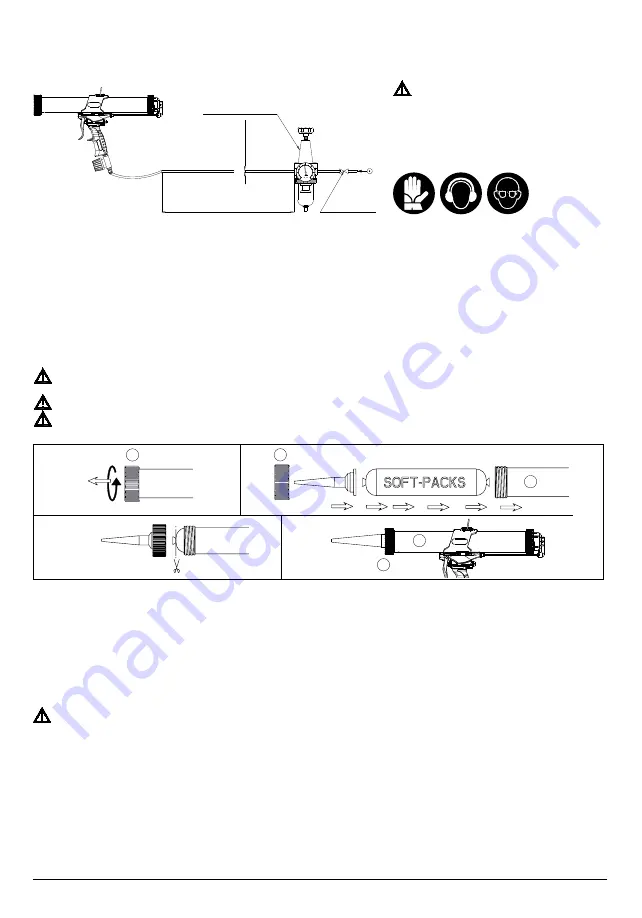
10
English
4.2.1 Unscrew the front ring nut counter-clockwise (2) and remove it from the machine.
4.2.2 Introduce and fix the bag nozzle to the front ring nut (2) (push the piston back in case it is forward); secondly introduce the
bag in the material holder tube (7); push the bag to the very bottom letting out only the part which is meant to be cut.
4.2.3 Cut the bag just under the closing metal band.
4.2.4 Tighten clockwise the front ring nut (2) to the material holder tube (7). The ring nut shall contain the plastic nozzle.
4.2.5 (Model CSG II 450 only) before introducing the bag in the material holder tube, make sure the bags extrusion kit has been
assembled, as outlined below.
Assembly of bag kit (Mod. 450)
Caution: this is the only operation to perform without the front nut. Before performing it, be sure that there are no
bags or cartridges inside!Carefully read the following!
4.2.5.1 Before starting, prepare two 13 mm spanners and a 5 mm Allen wrench.
Totally unscrew the knob of the pressure reducer on the machine anti-clockwise, then slowing slowly, clockwise with the
control level pressed until the piston inside starts to slowly move, stop pressing the control lever and remove the front nut
when the lever reaches it and stops. Afterwards, press the control lever again with one hand on the grip and one on the
pipe, as recommended, until the piston completely comes out of the pipe. Now disconnect or switch off the power supply.
4.2.5.2 Tighten the nut C with the two open ended spanners and unscrew and remove the locking nut A, also remove the metal
cartridge presser B (standard).
4.2.5.3 In the following order, tighten: the locking nut C (if removed to the previous position), the cartridge presser B, the (blue)
plastic support F, the scraper E, and with the 5 mm allen key the aluminium plastic bag presser D.
4.2.5.4 Ensure all components are tightened properly with the spanners and key previously employed.
4.1 Air feeding system
Connect the machine to a compressed air system featuring the following characteristics:
• Max. air humidity 5%; • Air temperature from -10° C to +70° C • System capacity 500 l/min at least • System equipped with lubri-
cator, pressure reducer and gauge.Lubrication must be: 3-4 drops of lubricant every 1000 l/min.
The machine is equipped with a ¼ gas male threaded connector, to which connection is possible according to specific needs. The
tube shall be a wound conductive tube for dynamic laying with resistance lower than 1 Mega Ohm and bursting pressure at least
twice the maximum pressure of the system. Air consumption is reduced and proportional to the number of times in which the
product supply lever is released.
4.2 Bag refill (Mod. 245 - 270 - 370 - 400 - 450* - 660 - 1100)
to be carried out by the operator
(*) These models are equipped with a bag conversion kit.
Always disconnect the machine from air feed during bag/cartridge replacement operations and any other time the front
ring nut is unscrewed from the tube. Accidental pressure on the lever may cause the violent unload of the bag the
crushing of fingers or any other risk for the operator and people nearby.
Always control the refill material expiry date.
Never introduce bags that are damaged or not perfectly intact.
Pressure reducer
with filter and gauge
Ø 6 mm
Fast tap
Max. tube length: 10 m.
Operating pressure: 4-8 bar
58/116 PSI
Before gun start-up and usage, wear the recom-
mended individual safety devices:
• Safety gloves
• Ear defenders
• Safety glasses
4. START-UP
to be carried out by the operator
4.2.1
4.2.2
4.2.3
2
2
2
7
7
4.2.4
Содержание P 600 B-2
Страница 51: ......
Страница 52: ......
Страница 53: ......
Страница 54: ......
Страница 55: ...USER S MANUAL CSG II SERIES MOD 210 245 270 370 400 450 660 1100 5010319 REV F 03 2018...