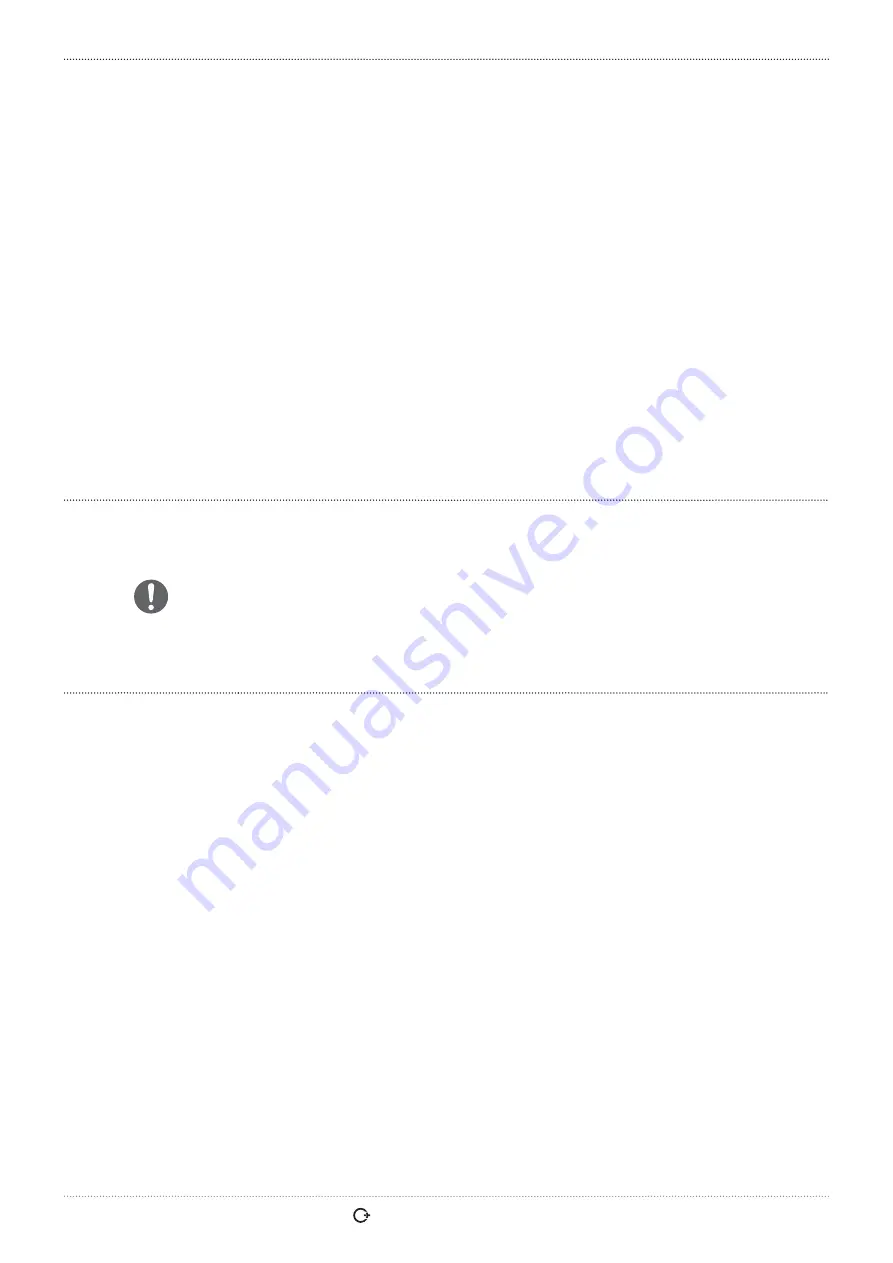
(01.2012) OM_BA_ORBIMAT_CA_01_EN
orbitalum tools
GmbH, D-78224 Singen, www.orbitalum.com, Tel. +49 (0) 77 31 792-0
| 41
ORBIMAT CA
| Operating instructions
OPERATION
nesses of around 4.0 mm. In these cases, the average value of both speeds is to be calculated for the resulting speed if
the high- and low-pulse times are the same length.
In principle, a high weld speed (up to max. approx. 200 mm/min makes sense) is only possible if the process does not
indicate tolerances (offset, wall thickness, air gap etc.).
At a somewhat lower speed, irregularities (e.g. minor fluctuations in the pipe wall thicknesses) are tolerated by the
process. With auto programming, average values are provided for this reason.
If a higher weld speed is required for an application:
X
Increase current to introduce the same energy (per section) into the process again.
For different weld speeds in the sectors:
When switching between sectors at different speeds, the motor is accelerated or braked linearly if a slope time has
been set.
Deactivating transition in the speed
1. In the main menu, select "System settings" > "Program settings".
2. Select the "No" option for "Speed without ramp".
The slope is deactivated in the current procedure.
3. Press softkey 5 ("Menu").
The machine is ready to start.
If you are working with different speeds in high- and low-pulse current:
XXDo not select pulse times shorter than 0.2 seconds to balance the inertia of the motors
and the machinery.
If the motor is to nearly stand still in the high-pulse phase:
XXEnter value "1" for the speed.
The motor continues running and does not have to overcome static friction when starting
up. This protects the motor and leads to higher precision while complying with the angle
of rotation while welding.
Auto programming automatically generates the value 1 for the weld speed in the high-
pulse time during operation in sync with the pulse.
Adjusting wire feed parameters
X
Only adjust wire feed parameters if a weld head is connected or was selected with cold wire supply.
With other weld heads, the input fields are grayed-out.
Wire feed parameters:
•
Wire start delay (in seconds)
•
Wire final delay time (in seconds)
•
Wire retract (in seconds)
•
Wire HP Speed (in mm/min)
•
Wire LP Speed (in mm/min)
Changing the wire feed quantity requires a change to the current, since more (cold) material is introduced to the wel-
ding process with an increased wire speed, for example. If the wire quantity is too high, it is difficult to control the melt
pool in the individual positions or it breaks away or drips off.
Wire start delay
: The time from ignition of the arc to the introduction of wire feed. The time corresponds with the time
for pool formation (start delay for the rotation motor). It cannot be longer than the pool formation time.
In special cases, it can be shorter than the bath formation time, so that the wire enters the melt pool while the rotation
motor is still not moving.
X
Do not set wire start delay too short, as the wire is not "taken up" if the melt pool has not yet been formed.
Wire final delay time
: Time during which the wire is still fed to the process during current slope-off at the end of
welding. Its minimum value is 0 and maximum value is as long as the current slope-off. With a value of 0, the wire feed
stops when current slope-off begins. If the time corresponds to the duration of the current slope-off, wire continues to
Содержание ORBIMAT 165 CA
Страница 78: ...orbitalum tools gmbh Notizen Notes ...
Страница 79: ......