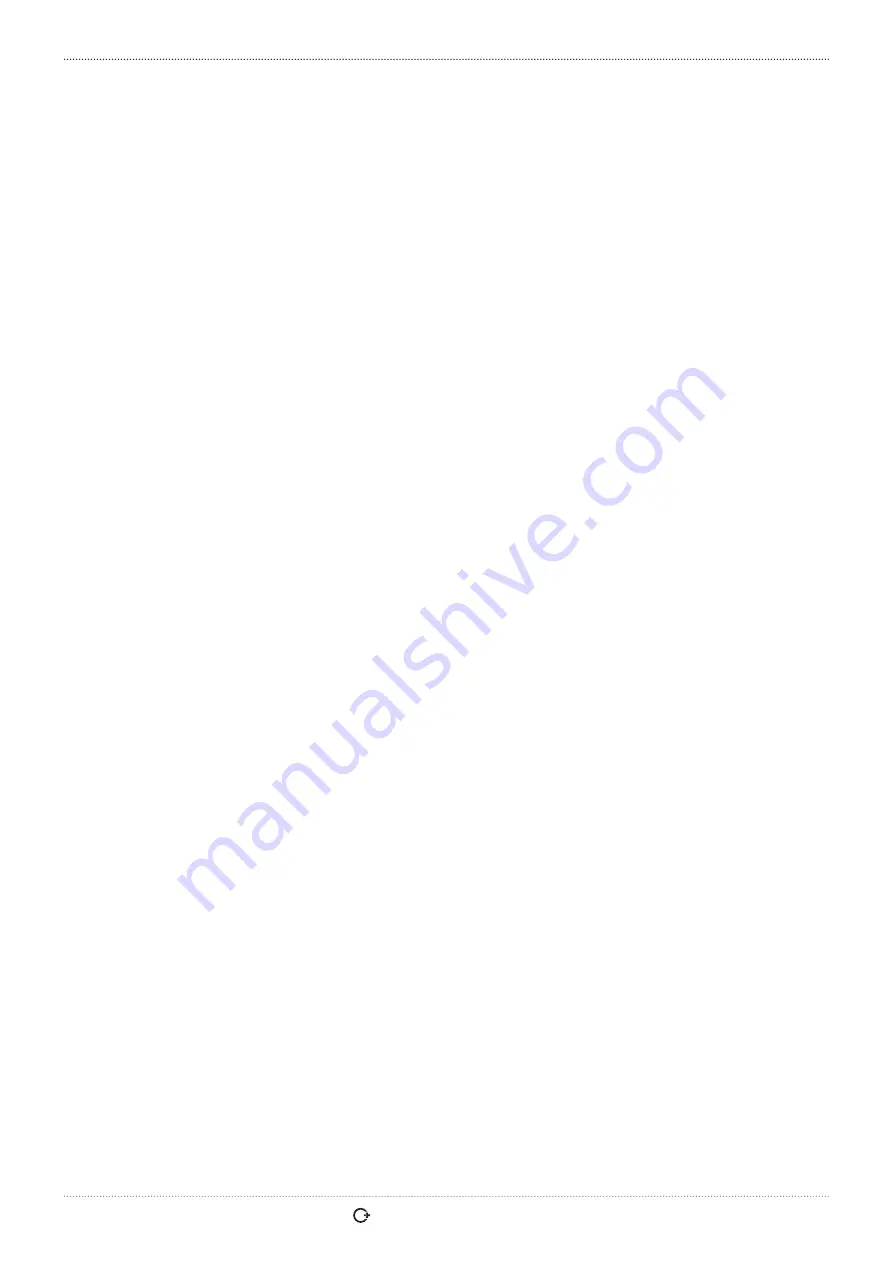
(01.2012) OM_BA_ORBIMAT_CA_01_EN
orbitalum tools
GmbH, D-78224 Singen, www.orbitalum.com, Tel. +49 (0) 77 31 792-0
| 35
ORBIMAT CA
| Operating instructions
OPERATION
X
Press EMERGENCY-STOP button on connected remote control.
The entire machine is disconnected from the mains network immediately and completely (both poles). No other
functions are carried out here: The gas flow is interrupted immediately. The current weld becomes unusable.
Stopping a running process
X
Press softkey 1 ("Stop").
– or –
X
Press STOP button on connected remote control.
– or –
X
Press red START/STOP button on weld head.
The weld current is switched off immediately. The machine remains in operation, the gas post purge time runs and the
water cooling of the weld head is carried out until the end of the gas post purge time.
A slight crater can arise in the seam on the workpiece, and this can be compensated for by over-welding it.
Premature slope-off of a running process
X
Press softkey 2 ("Final slope").
– or –
X
Press the "Final" button on the weld head.
– or –
X
Press slope-off symbol on connected remote control.
The machine slopes off the weld current as per the procedure. The weld head continues running during the slope-off
phase. After slope-off, the weld current is switched off, the gas post purge and pump continue running until the end of
the programmed time.
8.3
Adjusting the procedure
8.3.1
Reasons and steps for adjusting procedure
The auto programming of the machine cannot take all influencing factors into account during welding.
Procedures can be adjusted after the test run for this reason. Possible reasons:
•
Batch-dependent fluctuations in the material composition
•
Different dissipation (pipe on solid parts) etc.
X
Improve procedure step by step. When adjusting, change only one parameter at a time so that you can better judge
the influence on welding.
X
Save adjusted procedure.
X
After the adjustment, carry out a test run of the parameters.
X
Observe effects of the adjustment and carry out further adjustments if necessary.
8.3.2
Making percental changes
Reason:
Welding result even, but weld seam penetrated too lightly or too heavily.
The percental change affects all levels (sectors) on high- and low-pulse current.
After the test run, the "Correction factor" field is highlighted in the display.
1. Highlight a field.
2. Adjust and save value with rotary knob or keyboard:
Positive value: Increase weld current
Negative value: Reduce weld current
The settable value range can be limited in the program (e.g. only max. +5% and min. –5%).
X
Turn key switch to cancel limit if necessary.
Changing correction factor limit
1. In the main menu, select "System settings" > "Program settings".
The current limit is specified in the "Limit for correction factor" field, in which the operator can change the correction
factor in "completed" mode (production mode).
Example
: Specification "5%" – Change in range from –5% to +5% (absolute range: 10%).
Содержание ORBIMAT 165 CA
Страница 78: ...orbitalum tools gmbh Notizen Notes ...
Страница 79: ......