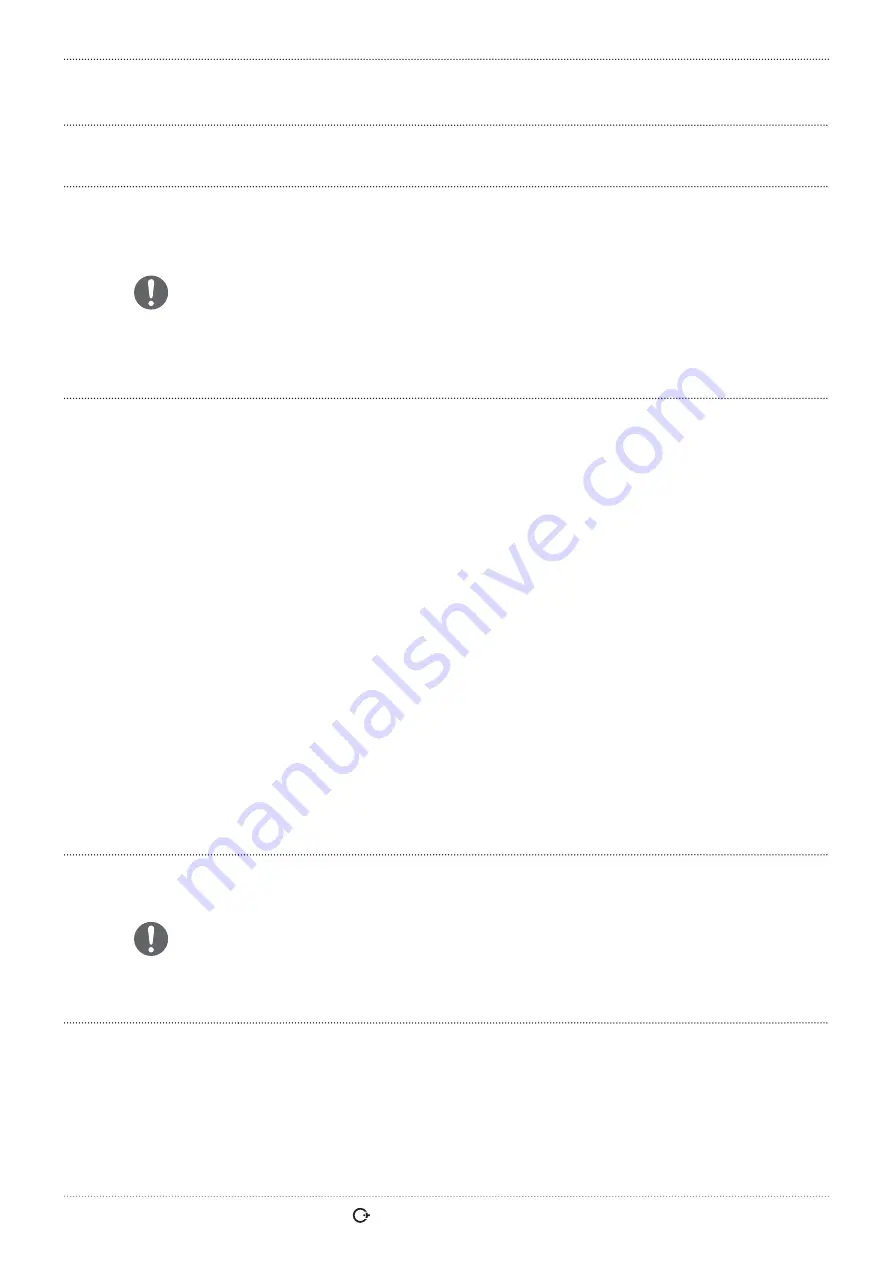
(01.2012) OM_BA_ORBIMAT_CA_01_EN
orbitalum tools
GmbH, D-78224 Singen, www.orbitalum.com, Tel. +49 (0) 77 31 792-0
| 33
ORBIMAT CA
| Operating instructions
OPERATION
CAUTION
Impermissible gas pressure inside the pipe. Penetration of melted metal into the weld head.
Damage to weld head.
[
Ensure that gas pressure does not build up inside the pipe.
X
XWhen using closed weld heads, ensure that the same gas type is used both outside
and inside the pipe, i.e. the same gas both for the machine (weld head) and that
which is fed into the pipe.
Different gas types can lead to an undefined mixture of both gases in the welding pocket
and thus to uneven weld penetration.
X
Do not use "classic" forming gases with up to 30% hydrogen content.
A small amount of hydrogen which ends up in the welding pocket from inside the pipe
via the pipe joint can lead to considerably greater penetration, as the hydrogen releases
additional energy during combustion.
Values gained from experience: An admixture of only 2% hydrogen has roughly the same
effect on penetration as a 10% increase in weld current.
8.2.3
Welding
Starting the welding process
X
Before beginning, read "Interrupting the welding process" see Sec. 8.2.4, Page 34 so that you can take action
immediately in case irregularities arise during a test run.
D
Power source programmed
D
Weld heads prepared for welding: Properly connected and positioned
D
Gas bottle secured and opened
D
Machine switched on
D
The main menu appears in the display
X
Press softkey 1 "Weld".
The machine is ready to start. The "Start" button in the display is red.
X
Press softkey 1 "Start".
– or –
X
Press START button on an external remote control, if connected.
– or –
X
Press red START/STOP button on weld head.
The water pump starts up, and the solenoid valve is opened. After the programmed gas pre-flow time passes, the arc is
ignited and the welding process begins.
The machine carries out the welding process completely.
Open the gas bottle and regulate to a small flow of forming gas mixture.
X
Observe welding process continuously and be prepared to take action at any time.
X
With open weld tongs: Ensure proper guidance of the hose assembly while the rotor is
circling.
Possible problems with the welding process:
•
Incorrectly set weld current
•
LP weld tong not tensioned tightly enough
•
Forming gas quantity too high, holes being formed
X
In these cases, interrupt welding process see Sec. 8.2.4, Page 34.
Welding process – Sequence
The machine carries out the welding process completely. During the welding process,
the machine monitors the welding process and the following parameters:
•
Cooling water flow: The welding process is stopped if the limit value of 0.8 L/min is undershot.
•
Gas flow: The welding process is interrupted if 3 L/min is undershot.
•
The weld current, weld voltage and weld speed process parameters:
Содержание ORBIMAT 165 CA
Страница 78: ...orbitalum tools gmbh Notizen Notes ...
Страница 79: ......