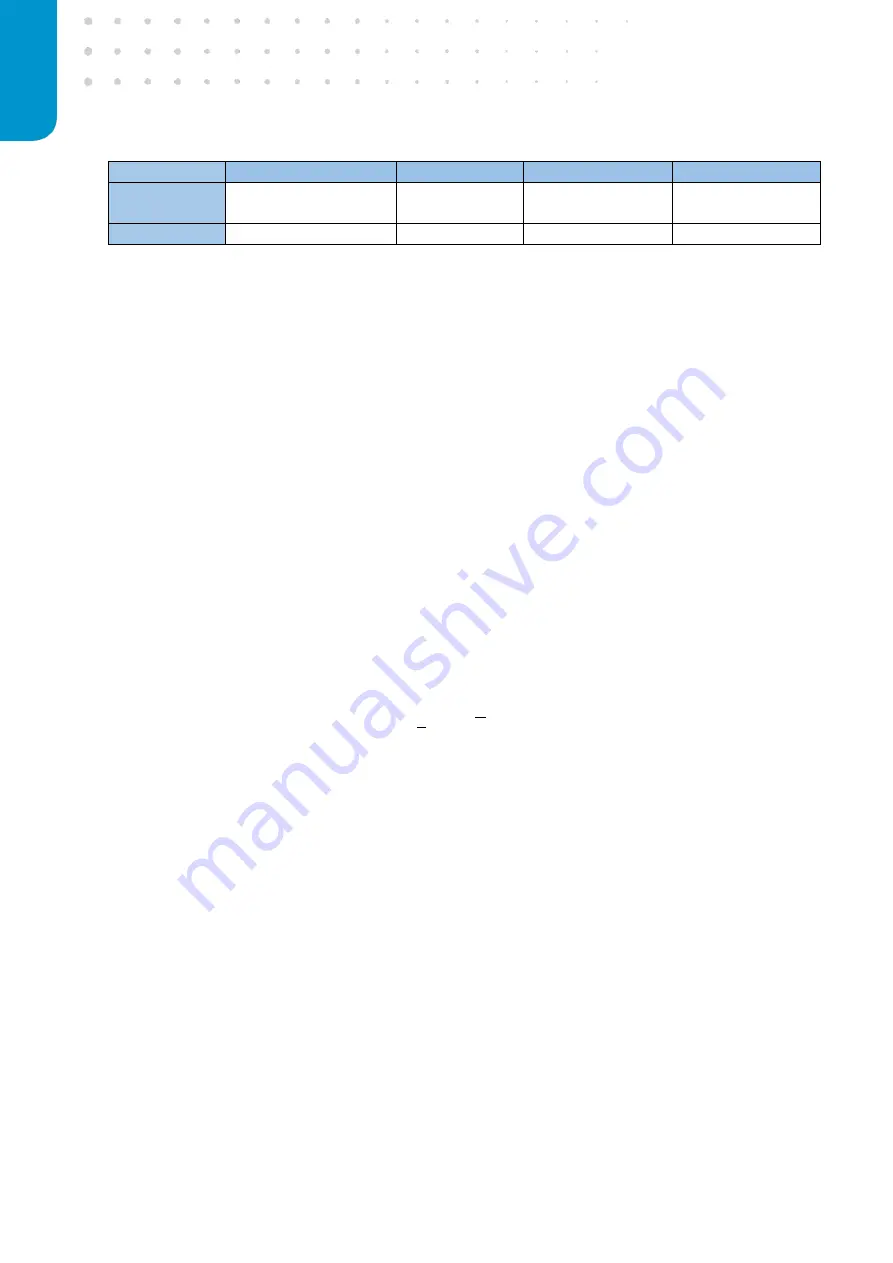
34
optics11life.com
Table 3:
Comparison of the three modes of operation.
•
Displacement control operates in an open-loop, meaning that only piezo displacement is
controlled but not load or indentation-depth. The actual load and indentation-depth will depend
on the stiffness of the sample and the stiffness of the cantilever (
-a, c).
•
Load control operates in a closed-loop, meaning that the load and time it takes to reach this load
(load-speed) is selected by the user.
•
Indentation-depth control works in closed-loop as well, but this time indentation-depth and time
needed to reach it (indentation speed) are set by the user. The piezo is adjusted accordingly to
induce a selected load profile on the sample (
-b).
•
Peak load poking mode operates in an open-loop in which piezo speed is controlled to reach the
maximum load that is selected by the user after which the probe is retracted at high speed. This
mode can be considered as a mode between Displacement control and Load control modes.
Operating in an open-loop makes this mode very fast and well suited for single cells in
combination with Hertz model fitting.
During all three modes of operation, the instrument is recording piezo movement (blue) and cantilever
bending (green) shown in
-a.
Indentation depth is calculated by subtracting cantilever bending
from piezo movement while in contact with the sample. The load is calculated by multiplying cantilever
bending with the spring constant of the cantilever.
The contact point with the sample (0 point in
indentation graph)
and effective Young’s modulus
is determined from the Hertz model to fit over the
initial load-indentation curve (
-e, red line):
𝐹 =
4
3
𝐸
𝑒𝑓𝑓
√𝑅 ∙ ℎ
3/2
𝐸 = 𝐸
𝑒𝑓𝑓
(1 − 𝜈
2
)
where
F
is load,
R
is the tip radius,
h
is indentation depth,
𝜈
is Poisson’s ratio,
𝐸
𝑒𝑓𝑓
is effective Young’s
modulus and
E
is
Young’s modulus which can be estimated with Poisson’s ratio is known.
Thus, if the
fitting has failed, the wrong contact point will be drawn in the graph. This can be corrected in DataViewer.
Changes to fitting in the main software can be done in
the “
Options
”
menu (
-b). Keep in mind
that this fit is just a preliminary one and one can change fitting parameters and contact mechanics models
in DataViewer.
D-mode
P-mode
I-mode
PLP-mode
Controlled
parameter
Piezo displacement
Load
Indentation depth
Piezo speed & max
load
Sample Circuit
Open-loop
Closed-loop
Closed-loop
Open-loop
Содержание PAVONE
Страница 1: ...PAVONE USER MANUAL ...
Страница 50: ...50 optics11life com Figure 42 Different stages of wellplate calibration process a b c d ...
Страница 64: ......