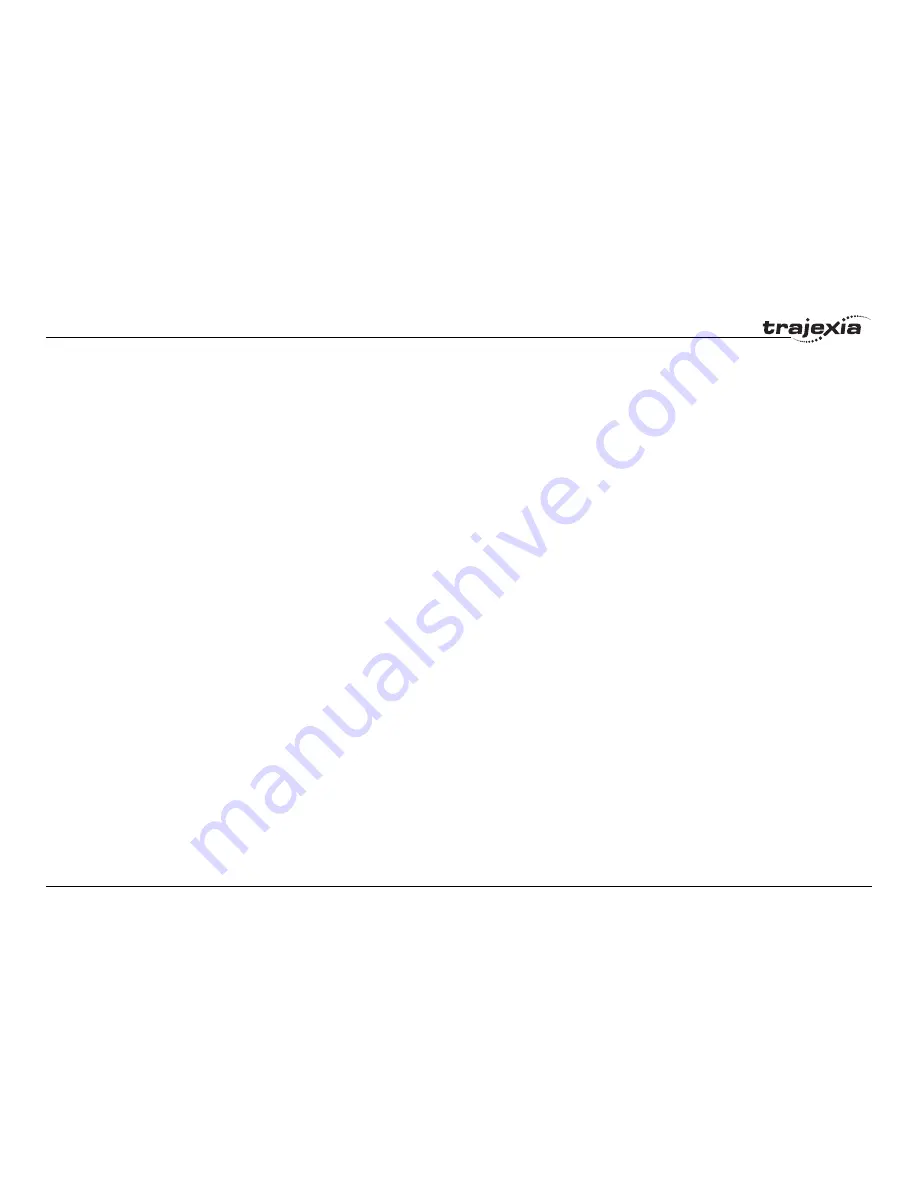
BASIC commands
PROGRAMMING MANUAL
97
R
e
vi
si
o
n
1
.0
3.2.125 FASTDEC
/i
3.2.126 FE
/i
3.2.127 FE_LATCH
/i
3.2.128 FE_LIMIT
/i
Description
The
FAST_JOG
axis parameter contains the input number to be used as the
fast jog input. The number can be from 0 to 31. As default the parameter is set
to -1, no input is used for the fast jog.
The fast jog input controls the jog speed between two speeds. If the fast jog
input is set, the speed as given by the
SPEED
axis parameter will be used for
jogging. If the input is not set, the speed given by the
JOGSPEED
axis
parameter will be used.
Note: This input is active low.
Arguments
N/A
Example
No example.
See also
AXIS
,
FWD_JOG
,
JOGSPEED
,
REV_JOG
,
SPEED
.
Type
Axis parameter
Syntax
FASTDEC
Description
The
FASTDEC
axis parameter contains fast deceleration ration. Its default
value is zero. If a non-zero
FASTDEC
is specified, the axis will ramp to zero
at this deceleration rate when an axis limit switch or position is reached.
Arguments
N/A
Example
No example.
See also
N/A
Type
Axis parameter (read-only)
Syntax
FE
Description
The
FE
axis parameter contains the position error in user units. This is calcu-
lated by the demand position (
DPOS
axis parameter) minus the measured
position (
MPOS
axis parameter). The value of the Following Error can be
checked by using the axis parameters
FE_LIMIT
and
FE_RANGE
.
Arguments
N/A
Example
No example.
See also
AXIS
,
DPOS
,
FE_LIMIT
,
FE_RANGE
,
MPOS
,
UNITS
.
Type
Axis parameter (read-only)
Syntax
FE_LATCH
Description
Contains the initial
FE
value which caused the axis to put the controller into
MOTION_ERROR. This value is only set when the
FE
exceeds the
FE_LIMIT
and the
SERVO
parameter has been set to OFF.
FE_LATCH
is reset to 0
when the
SERVO
parameter of the axis is set back to ON.
Arguments
N/A
Example
No example.
See also
N/A
Type
Axis parameter
Syntax
FE_LIMIT
FELIMIT
Description
The
FE_LIMIT
axis parameter contains the maximum allowed Following Error
in user units. When exceeded, bit 8 of the
AXISSTATUS
parameter of the axis
will be set. If the
ERRORMASK
parameter has been properly set, a motion
error will be generated and WDOG enable relay will be reset to 0.
This limit is used to guard against fault conditions, such as mechanical lock-
up, loss of encoder feedback, etc.
Arguments
N/A
Example
No example.
See also
AXIS
,
AXISSTATUS
,
ERRORMASK
,
FE
,
FE_RANGE
,
UNITS
.