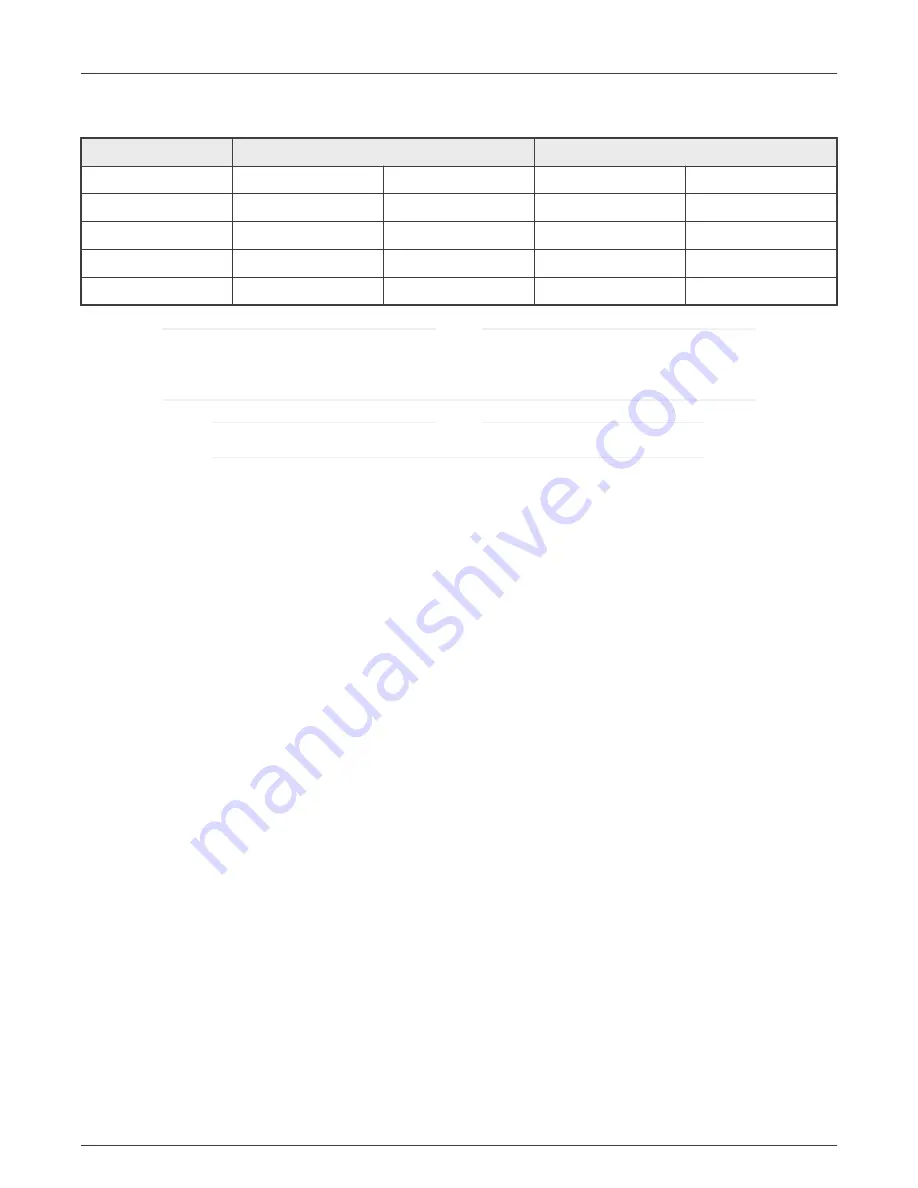
Table 5. i.MX RT1170 CPU load and memory usage (similar for RT1160) (continued)
debug configuration
release configuration
SRAM_DTC
-
-
-
-
SRAM_ITC
72 B
Usage 0.03%
48 B
Usage 0.02%
SRAM_OC
-
-
-
-
Speed Control
Position Control
Speed Control
Position Control
Maximum CPU load
5.49%
5.22%
4.5%
4.36%
The maximum CPU load is depending on executing functions from RAM or FLASH memory. Executing functions
can be speeding up in RTCESL_cfg.h header file by using macros RAM_OPTIM_HIGH, RAM_OPTIM_MEDIUM
or RAM_OPTIM_LOW.
NOTE
Memory usage and maximum CPU load can differ depending on the used IDEs and settings.
NOTE
NXP Semiconductors
RT crossover processors features and peripheral settings
MCUXpresso SDK Field-Oriented Control (FOC) of 3-Phase PMSM and BLDC motors, Rev. 0, 01/2022
User Guide
14 / 50