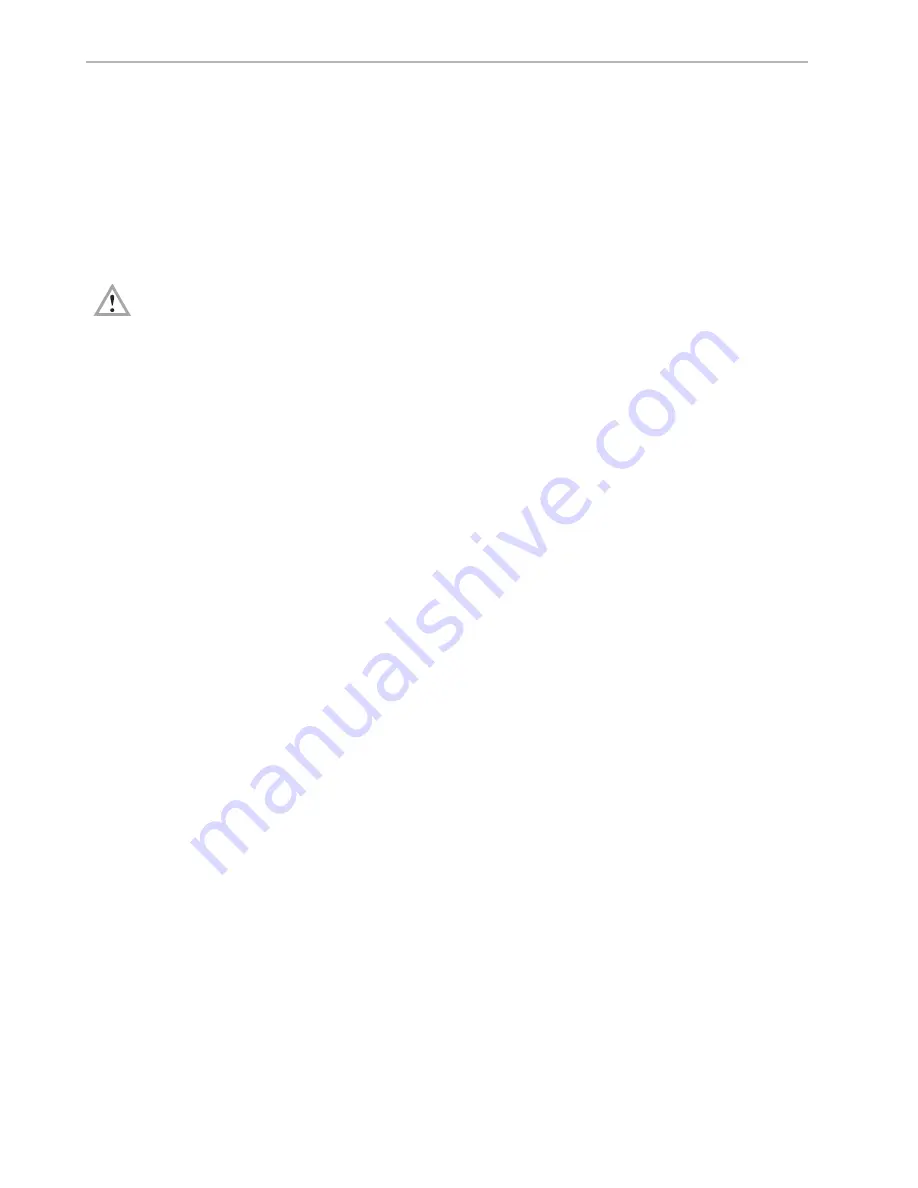
10
E
.0
4.
20
00
•
G
. 1
6.
11
.1
0
Flue connection
19. Flue connection
The prerequisite for perfect operation of the furnace is a correctly dimensioned flue.
Dimensioning is effected in accordance with DIN 4705 in consideration of DIN 18160 and based on the
boiler and burner outputs.
For operation on a sliding basis, provide flues as per DIN 18160 part, group 1. The flue gas mass flow
of the total rated heat output must be factored into the calculation. The effective flue height is counted from
burner level. Furthermore, we refer you to the statutory building regulations of the individual German fed-
eral states.
Select a flue design which minimises the danger of condensation or of a cold flue inner wall.
For exact adjustment and stabilisation of the flue draught we recommend the installation
of a draught limiter.
Thus:
•
any draught fluctuations are equalised
•
moisture in the flue is largely excluded
•
stoppage losses are reduced.
Connection pieces should be introduced into the flue with a gradient of 30° or 45° viewed in flow direction.
It is best to provide flue gas pipes with thermal insulation.
20. Flue gas thermometer
For flue gas temperature monitoring the heating system should be equipped with a flue gas thermometer.
The higher the flue gas temperature, the greater the flue gas loss.
Rising flue gas temperatures indicate increasing deposits that will reduce the degree of combustion effi-
ciency. In the event of an increasing flue gas temperature have the heating installation cleaned and read-
justed by a skilled person.
21. Maintenance
Depending on the quality of the oil used, we recommend the following maintenance intervals:
After more than 3 days downtime:
•
drain off residual water and sludge through the water drain cock in the burner tank,
Monthly:
•
Clean the filter in the supply tank or the unit tank and strainer on the floating suction unit
•
Remove and clean the feed pump filter
•
Remove sludge and residual water from the supply tank or unit tank
•
The quantity can be determined by using water indication paste and a gauging rod
•
Clean the photocell
•
Clean the ignition electrode and baffle plate and blow out the nozzle with compressed air, check the
spacing between the ignition electrodes (refer to checking dimensions for ignition electrodes)
Annually (before or after the heating period):
•
Carry out monthly maintenance as described
•
Clean the heating cartridges in the burner tank
•
Clean the ignition electrodes and baffle plate, blow out the nozzle with compressed air and check the
spacing between the ignition electrodes
•
Clean the burner tank, supply tank and unit tank thoroughly.
Содержание G100 Universal
Страница 1: ...G100 Universal Oil Burner Installation Maintenance Manual...
Страница 15: ......