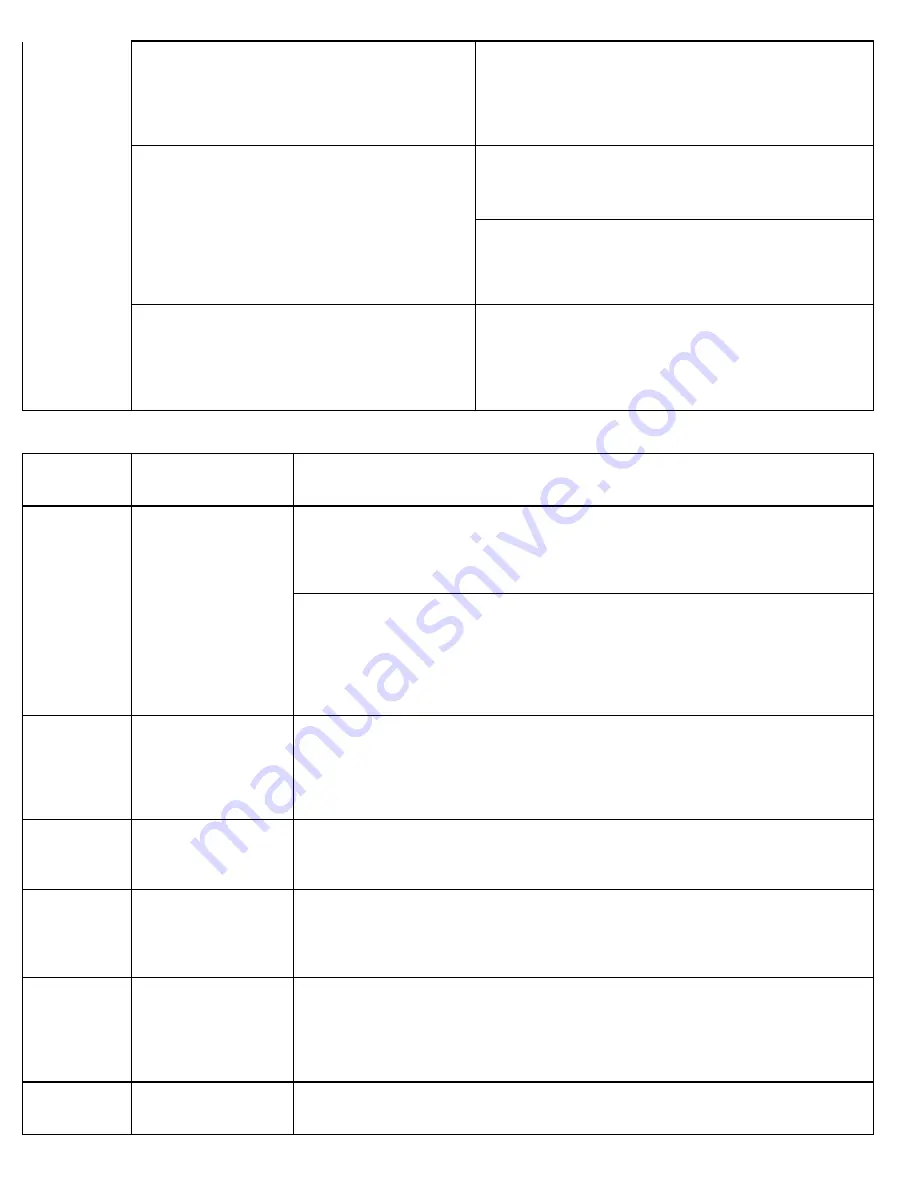
30
Check for 24 Volts between terminal F1 on
Sentry & Ground
1 – If 24V exists here but not at B1, indicates faulty relay
inside Sentry, contact NTI, replace control.
2 – If 24V is not present check for 24V at transformer.
– If 24V exists at transformer, check wiring and safety
limits. If 24V not present at transformer, check wiring
and replace transformer if necessary.
May be caused by an error in the reading of the water
temperature by the Sentry control. Watch cycle, and
ensure the Sentry is displaying the correct water
temperature and is modulating.
Water Safety Limit trips
(Automatic reset)
((Located in the supply manifold inside the boiler
cabinet))
This device protects the boiler from overheating due to a
lack of flow passing through the unit when the burner is
on.
FLOW MUST NEVER BE BLOCKED BY ANY VALVES
INCLUDING MIXING OR ZONE VALVES.
Install unit as described in the manual.
activated
when burner
light is on
(Fan is on
and Fenwal
not flashing)
Continued
Stack Safety Limit Trips
(Automatic Reset)
((Located on the front of the flue box))
This device protects the integrity of the plastic venting
material.
If the temperature of the flue gases exceeds 225
°
F the
limit will cut power to the control. Blocked internal tubes
can increase the stack temperature to an unacceptable
level. Flush out the boiler.
Problem
Detected
Problem
Solution
Two Flashes
on Fenwal
The Fenwal controller
thinks that there is a
flame prior to ignition.
If the combustion sequence is normal, and there is no flame prior to ignition, the
Fenwal control is defective, and must be replaced.
If the condensate drain gets blocked, the boiler will become flooded, and terminate
operation, as the flame rod becomes immersed. This will damage the flame probe.
To correct, free the drain blockage, and permanently prevent it from reoccurring.
Remove and dry off the probe. Reinstall the probe and try for ignition, if it fails to
ignite, leave the fan run for up to three hours to dry out the insulation and probe.
Three
Flashes on
Fenwal
Indicates Ignition
Lockout.
Reset Boiler so it will attempt to ignite.
Check for proper operation of ignition components. Make sure igniter glows and gas
valve opens.
Check for proper line pressure at gas valve when it opens.
If boiler lights check for flame signal between FC1 And FC2 on Fenwal control (If
lower then 1.2 micro Amps see “
Boiler will not stay lit
”).
Check combustion properties.
Boiler will
not stay lit
.
Indicates lack of a
flame signal. In order
to stay running the
flame signal must be
at least 0.7 micro
amps
If the Burner light on the Sentry is going out, go to “
Burner shutting off
”.
Check condensate drain for blockage and check the inlet piping for ingested snow or
water (if the flame rod gets wet, it may need to be replaced). Check for resistance
from flame rod to ground, must be an open circuit (O.L).
Check for proper polarity of line and neutral wiring to the boiler.
Boiler bangs
or hisses
Bangs or sounds like
a kettle while burner
is running indicates
insufficient flow
Ensure the plumbing is as shown in manual. Check to see if pumps are faulty or end
switches are stuck.
This problem can lead to boiler overheating!
Sentry
Controller
Locks-up
Excessive noise,
current, or voltage
spikes in the 120V
power supply.
Check for voltage at the wires going to the A-C-T terminals of the Boiler.
Check the magnitude of the line voltage power supply.
Check the Amp draw of output C1 and Ap (max 3 Amp).
Check the Amp draw of control on start-up (max 6 Amps)
Contact NY Thermal.
Display
Goes Blank
No power to control
or control failure
Check for 120V between terminals L1 and L2 at Sentry.
If 120V exists turn power off and remove line voltage harness from Sentry. Then
check for resistance between L1 and L2 of control, if the circuit is open (O.L) the
internal fuse has blown. Check for shorts in wires leading to circulators prior to
replacing controller.
If 120V not present, check wiring and for 120V at source.
Boiler Lights
rough or
pulsates
Typically an
imbalance in the Air
to gas ratio
Ensure that the venting lengths are in compliance with Section 3.4
Ensure that the line pressure during operation does not drop more than 20% from
the static line pressure.