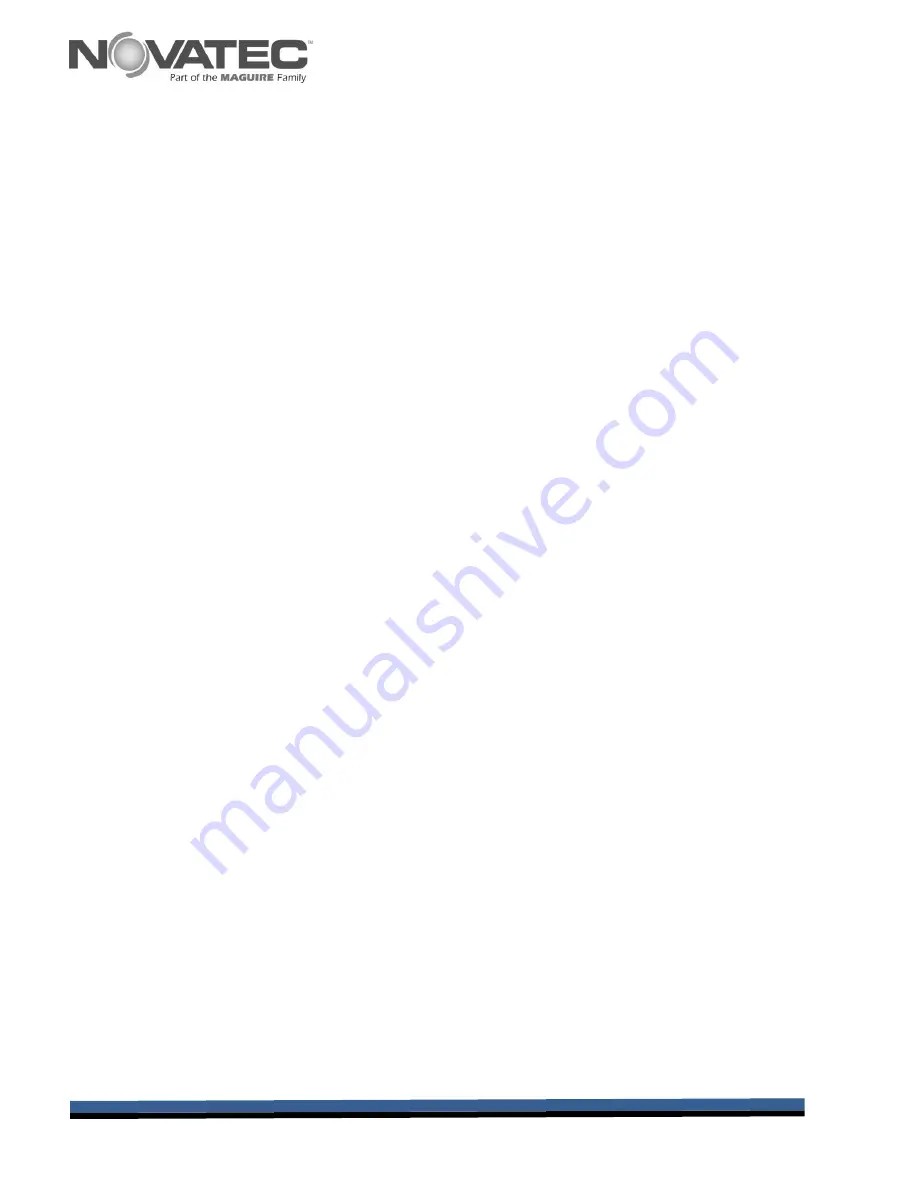
© NOVATEC, Inc. 2013 All Rights Reserved
VL-VLP IM 4-12-2013
4
1- PRINCIPLE OF OPERATION
NOVATEC vacuum loaders utilize a powerful motor to create a vacuum, which draws material into
a chamber. After the load time setting has expired, the vacuum motor is turned off and the
negative pressure in the chamber is relieved. Material in the chamber then falls through the
bottom, past the flapper while compressed air is pulsed through the filter to dislodge any
contaminants or fines that may have accumulated. This cycle is repeated as many times as
necessary, until the unit is shut off by the rise of the conveyed material in the area below the
loader which trips the level switch, removing the ‘demand’ signal.
Machine mounted units do not have a demand switch actuated by the discharge flapper valve, but
instead utilize a remote sensor for demand. The sensor is attached to an adjustable bracket that
slides along the length of a clear sight tube serving as a Just-in-Time (JIT) material hopper
mounted between the machine throat and loader discharge. The sensor height on the site tube
determines the level of material that triggers a demand for more material and a new load cycle.
The sensor may be either a capacitance style, with sensitivity adjustment, or a pair of
photoelectric sensors, an emitter and a receiver.
The bottom flange is normally supplied undrilled to allow the customer to drill the appropriate
mounting pattern for a particular machine.
2- UNPACKING AND INSPECTION
NOVATEC Vacuum loaders are shipped complete, with all controls for automatic operation. The
only utilities required are a 115 or 220 volt power supply (depending on voltage of control), and
clean, dry compressed air at approximately 80 PSI.
After receipt of the unit, completely inspect it for damage. Although the units are packaged
securely, vibration and mishandling during transit can cause damage.