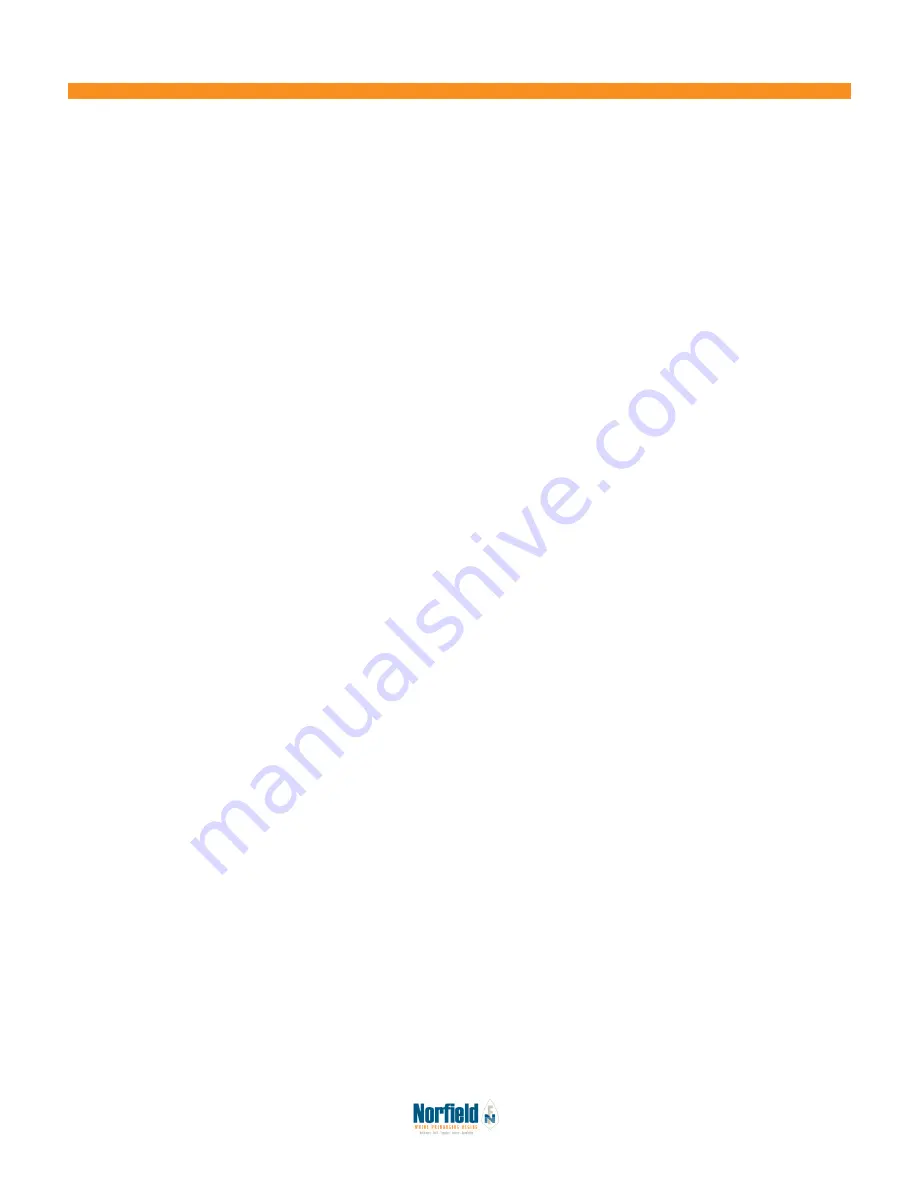
46
SPECIAL ADJUSTMENTS
4-16 LATCH PLATE MORTISE DEPTH:
To establish the vertical travel of the latch mortising assembly, lift the latch routing lever by activating the
button in the handle (no door in the machine and with the motor switch off). Check to see that the base of
the template guide on the control weldment does not touch the bottom surface of the template holder. If
it does touch the template, the control weldment must be lowered slightly by loosening the shaft collars.
When at rest, the template guide should now be touching at least 1/16” of the bottom of the template.
After the template holder is set at the correct height and the vertical travel is correct, the depth of the ac
-
tual mortise may be adjusted. To mortise deeper, loosen the micrometer and adjust the router up into the
casting the amount needed and tighten the micrometer. If the mortise is too deep, use same procedure
except lower the router.
4-17 MAIN BAR:
CALIBRATION CHECKS:
The Main Bar is the rectangular long tube assembly that is affixed to the width carriage assemblies. It
must be parallel to the outfeed rollers. To ascertain this, select a door that has just been sized and beveled,
measure it to make sure it has no taper, check the scale on the machine to see if it reads the exact width of
the door you just measured, and then place it on the outfeed rollers. Now, at each end of the door, mea
-
sure from the hinge edge down to the main bar. This measurement should be 2-1/2” at each location.
If the dimension of the door to the main bar are equal but are not 2-1/2”, the following procedure should
be used:
1. Calculate the difference of error from 2-1/2” , as an example if the actual measurement is 2-7/16” the
error would be 1/16”.
2. Move the door width scale pointer by the amount of the error, up for a measurement less than 2-1/2”,
and down for a greater dimension until you achieve the required 2-1/2”. After moving the scale you
will need to re-set the door width using the elevator buttons.
3. Re-calibrate the pointer on the undercut scale by loosening the pointer and moving it to the correct
reading. The reading of the scale should be the same as the undercut of the door sized.
4. The indicator lines on the undercut reference roller assembly may also need calibration, The red lines
should align when the door is 2-1/2” above the main bar.
If the dimension on the undercut scale is different than the measured door width, the following proce
-
dure should be used:
1. Re-calibrate the undercut scale by moving the pointer until it reads correctly, move just the pointer
without adjusting the assembly up or down.
2. Re-calibrate the undercut reference roller indicator until you have the 2-1/2” dimension and the
proper undercut, this may require repeating steps one and two several times.
3. Set the undercut scale to read exactly what the door width is by moving the pointer.
If the dimensions are not equal from the hinge edge of the door to the main bar, adjust the width carriage
on the outfeed end (right side) by moving the torque tube gear up or down as required, an adjustment
screw is provided at that location.