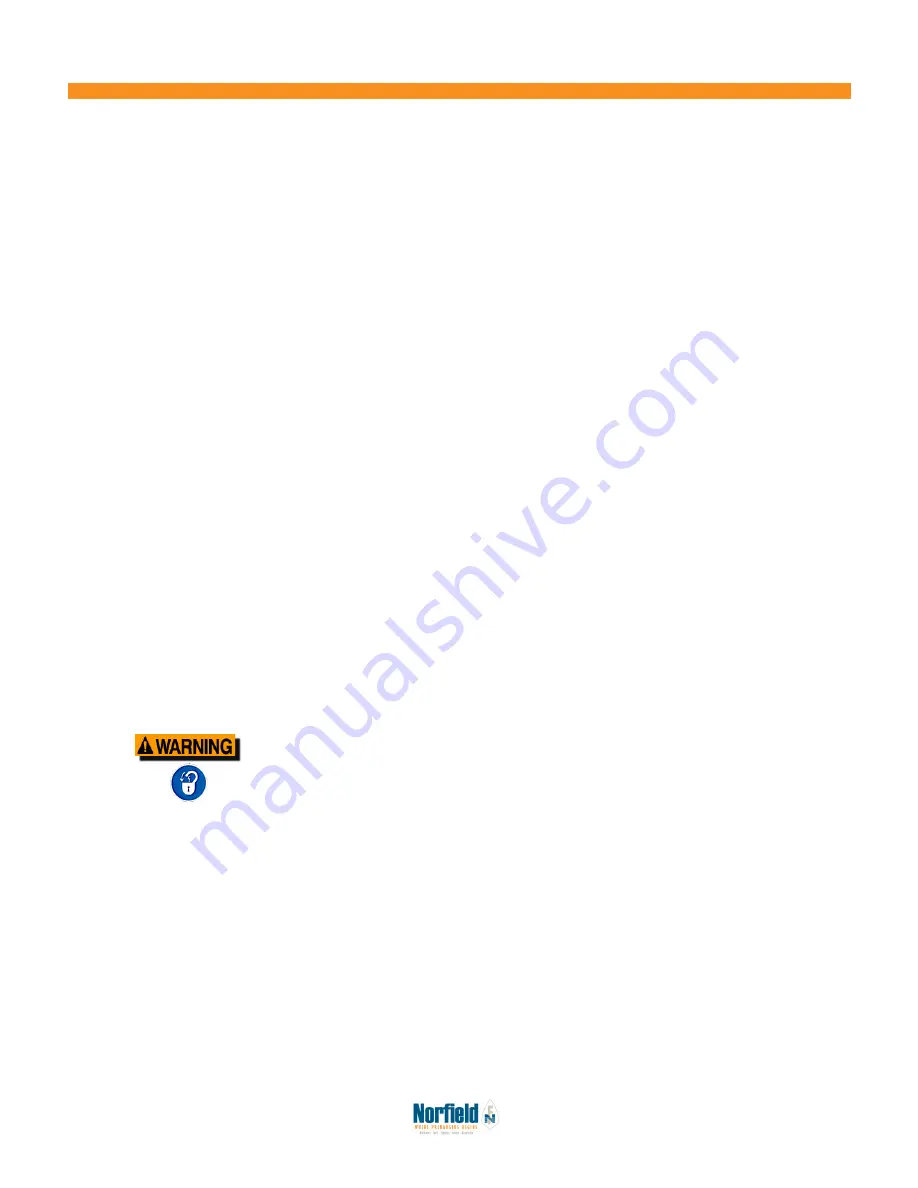
38
4-3 OUTFEED ROLLERS:
To the right of the outfeed bed, facing the machine, there are four rollers called outfeed rollers. They are
positioned at the factory and are referenced to the outfeed bed. It is not likely they will ever get out of
adjustment. Adjusting these rollers in the field by other than factory trained service people is not recom
-
mended. If there is a problem in obtaining a straight edge on the door the problem is most likely the cut
-
terhead or possibly the Infeed Bed. For instance, if an undersized cutterhead is placed on the machine or
if the Infeed Bed is tilted forward, the door will “bump” the outfeed bed and cause a “nick” in the door
edge 11” from the front end of the door. Investigate the cutterhead and/or infeed bed and make adjust
-
ments.
After years of use, the outfeed rollers will wear to the point that they will need to be replaced. Their use
-
ful life can be extended by keeping them and the shafts they turn on, clean at all times and by reversing
them on the shafts periodically. This is practical since only the high point of the bevel actually rolls on the
rollers.
4-4 CUTTERHEAD HEIGHT:
The “effective cutting height” of the cutterhead is a term used to describe the location of the long point of
the bevel on the door as it is being sized. The long point of the bevel is always towards the machine and
the door slides against a permanent reference, or fence. It doesn’t matter how thick the door is, the effec
-
tive cutting height of the cutterhead remains constant, assuming the diameter of the cutterhead and the
“set” of the blades remain constant.
The relationship between the effective cutting height and the outfeed bed is extremely critical. THEY
MUST BE THE SAME HEIGHT, or an uneven edge will result. If you change the cutterhead and the new
cutterhead is smaller in diameter or if the blades are set differently, and a problem with the sized edge
develops, you should determine what the problem is with the cutterhead and resolve it before making
adjustments. Adjust the height of the cutterhead mandrel to the outfeed bed only as a last resort, first
determine what has changed to create the problem.
4-5 CUTTERHEAD MANDREL:
Before beginning any service repairs, general maintenance, or adjustments you
MUST follow proper Lockout Tag-Out procedures. OSHA regulation 1910.147
establishes a minimal lockout tag-out procedure to assist employers in the develop-
ment of their own procedures.
Should the need arise to remove the cutterhead mandrel assembly from the machine to replace the bear
-
ings, or to install a new mandrel assembly. The following procedure is recommended, refer to figure 4-3.
1. Turn off all electrical power and lock and tag-out the machine.
2. Remove cutterhead shroud, pulley and belt.
3. Loosen lower set screw (inside machine just under mandrel) one turn.
4. Remove 4 bolts that secure mandrel to frame.
5. Install a new mandrel (or mandrel with new bearings).